Introduction: Concrete Coffee Table
We were moving into a new house and the girlfriend hated our old Ikea coffee table, so we decided to make ourselves a new one. It's not made of pallet wood, so we're ok there, but we did use threaded pipe... Don't shoot us.
Parts:
- Melamine board for form making
- Dap/Silicone/crack sealer (DAP)
- 2 bags of concrete (Concrete)
- Poly fibres for concrete reinforcement
- 1" thick rigid styrofoam insulation (Rigid insulation)
- Threaded pipe fittings, 3/4" and 1/2" (Pipe Fittings)
- Threaded rod and nuts (Threaded Rod)
- Concrete sealer
- Sand paper
- Dust Masks
- Bucket for concrete mixing
Cost: The majority of the cost was in the threaded pipe fittings. They run close to $2 CAD each. We were fortunate enough to get a few things for free as well - Concrete sealer and poly fibres. Our total build cost was $160ish CAD but if we had to buy the sealer and fibres, we would have been about $200 CAD all in.
Dog: Gus had just been neutered when this picture was taken so he has his anti-licking shirt/onesie on. It is almost more ridiculous than a cone.
Step 1: Build a Form
We used Melamine for the form. The thin sheet on the bottom seemed like a better bet than a 3/4" piece simply due to the cost. We had a heavy board underneath it so it wouldn't be able to flex. The edges are 3/4" melamine.
You use melamine for it's smoothness. Any scratches, dents, blemishes on the form will show up on your finished concrete. If that's the look you're going for, good on ya. If you want smooth: go melamine.
After screwing the whole thing together, we sealed all the edges with Dap to ensure the corners would not leak.
If you look closely at the left "wall" of the form, you can see a pencil line. That line is at the 1/2" mark. In order to reduce the overall weight of the table, we decided to add rigid insulation to the core of the table. Remember how your parents used to have an empty jar or something similar in the toilet tank to take up space so you didn't use so much water? Well, this is the same idea. The insulation takes up the space that would normally be solid concrete, thus reducing the concrete volume used and reducing the overall weight.
Our total table thickness is 2": 1/2" Concrete 1" rigid insulation core 1/2" Concrete
The insulation is cut back about 2" from the long edges and 5-6" from the short edges. This gives us solidity around the whole table and a place to attach our legs directly into concrete and not into the insulation.
Step 2: Give It Some Legs!
While the dap dried, we put the legs together. We used 3/4" pipe for the vertical supports but reduced down to 1/2" for the horizontals. This saved us a bit of cash.
If you look closely, you can see the threaded rod and nuts sticking out of the flanges on the left side. These will embed directly into the concrete. More on that later.
Step 3: Call in the Reinforcements!
Again, in an effort to reduce weight, we opted to exclude re-bar or any other reinforcing metal. We went with poly fibres instead. A friend who works for a concrete company gave them to me. I didn't do any testing to see if it was stronger, but it hasn't crumbled yet. 3 months and counting!
Step 4: Pour It
Sorry, a bit of a jump ahead here we mixed and poured the concrete. My mix was a bit dry but it seemed to go in nicely. We followed the instructions on the bag but could have used more water. Pour 1/2" of concrete into the form, lay in the insulation, fill in the rest. We tried our best to smooth out the concrete, but our troweling skills aren't the greatest, but we like how it came out. A little rough around the edges
Step 5: Attaching the Legs
This is how the legs are attached to the table. I just used threaded rod and not bolts (as drawn). After we poured the concrete, we placed the legs on the wet concrete and pushed the rods in. They probably aren't gripping as well as we'd like, but they didn't really move after everything was dry, so we called it good. If they come out down the line, we'll just put glue into the holes where the rods were and then put the rods back in those holes and it shouldn't move again. But for now, the weight of the table is holding everything in place.
Step 6: Poured and Covered!
Sealing in the moisture is important so we laid some poly on top.
Step 7: Oooooo, Ahhhhh. Unboxed
We unwrapped it after an impatient 7 day cure. It came out of the form pretty well, but peeled a pit of the melamine paper off, which stuck to the table top. Hand sanding and a flap wheel attachment on my drill made quick work of that.
The sanding was taxing, but not terribly difficult. Especially since I just stood around taking pictures and not helping. All of the melamine remnants came off fairly easily.
Step 8: WE LANDED ON THE MOON!
We didn't get an absolutely flawless finish on the table top, but really, we didn't want it to be perfectly smooth. The pits and air bubble holes add texture and depth. We could have smoothed it out more by vibrating the concrete and having a wetter mix.
Step 9: Signed, Sealed, Delivered!
We were going to scratch our names into the bottom before it dried, but we waited too long. The nieces were on the driveway drawing with chalk so we decided to do the same. We signed the bottom with chalk and then sealed it in forever!
Step 10: Sealed and in Place
We sealed the table then added 4 coats of clear on top. Most of the pits and holes filled in a bit but there is still some texture. It's tough to see but it is really smooth! It looks at home in our place and Gus approves! Thanks for looking!
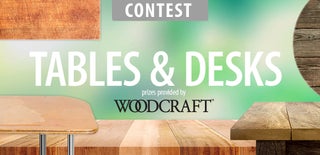
Third Prize in the
Tables and Desks Contest 2016
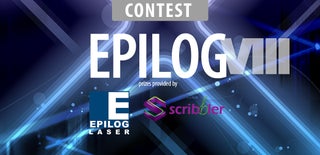
Runner Up in the
Epilog Contest 8