Introduction: Concrete Farmhouse Sink
My wife and myself are building our own home and love the classic farmhouse sink. Problem is that they’re very expensive and we want to save money wherever possible. So we started looking into how to DIY a kitchen sink yet couldn’t find much of anything so we went out on our own and now here we are making our first instructable on how we made our own concrete farmhouse kitchen sink.
Supplies
Quikrete
Styrofoam Sheets
Silicone sealant
3/4” plywood
Screws
Kitchen Drain assembly
White Waterproof concrete sealer
Angle grinder
Set of various polishing wheels
Work bucket
Concrete drill mixer
Paint brush
Circular saw
Drill
Utility knife
Caulk gun
WD-40
Step 1: Make the Mold
On this project I used high grade 3/4” plywood for the mold. It is very helpful to use a plywood that has a smooth finish as any shapes in the wood will imprint on the concrete when it cures.
To make the mold I had five pieces cut. One for the “bottom”, two for the length sides, and two for the width sides. The dimensions I used for these are,
1 bottom piece = 3' x 1.5'
2 length side pieces = 1.5' x 6"
2 width side pieces = 3' x 6"
Next you’re simply going to screw the four sides and bottom together creating a square bucket. I used two screws for each side, one on the upper side and one on the lower. This held the concrete perfectly.
I would recommend reinforcing the sides with 2x4’s possibly as the weight of the concrete actually warped one of the long sides outward. Not a issue for me because we actually wanted a slightly curved front and had a happy accident that gave us that.
Finally put a bead of the silicone in all the corners and smooth it out with your finger. Be liberal with the silicone as this is ensuring your mold doesn’t leak.
Step 2: Adding the Negative
Now we’re going to be cutting and glueing that foam to make the actual bowls of the sink. This is technically the negative of the sink where we made the frame to hold the concrete in before now we’re using the foam to shape where we don’t want the concrete in the frame.
To start we wanted the center divider to be slightly recessed and not flush with the entire sink so this is optional depending on your preferences. To put the recess in I cut one sheet of foam to ‘1',2" x 2',8" ’.
Next I cut six squares of foam in 1',2" x 1',3" squares. Once they’re cut I took 3 and glued them in a even stack on one side of the large piece lining the outer sides to be as smooth as possible. I used some of the silicone I had from the previous step to glue the pieces and it worked fine. Next do the same with the last three squares on opposite side of the large foam piece and let it all dry. Once it’s all dry take some sand paper and smooth out all the sides and corners of my sandwich. The smoother you get this the better it will be in the end since concrete is extremely tough to smooth. Once it’s smooth glue the entire sandwich piece in the center of the mold and not off side. For me using one giant piece I measured that each side had a roughly 2” space on all four sides. If you’re doing two pieces for your mold it will be 2” spacing on all sides with a 2” space between them as well.
Finally we’re gonna cut six 3.5” diameter circles of foam. This is going to be our stack for the two drains. Take three of the circles and glue them together just as before and sand them smooth as possible. I did not sand them and paid for it later so sand them. Do this again with your final three circles so that you now have two stacks. Once they’re smooth measure the exact center of the two square stacks and glue the cylinders in the exact center so that they are sticking up out of the mold and let the entire thing dry.
Step 3: Pouring the Concrete
Now it’s time to mix and pour the concrete. This is a relatively straightforward process, just follow the instructions on the bag. I can give you a few hints though, like mix small amounts of concrete and water at a time. Otherwise it will be too thick and difficult to mix properly and for me it actually grabbed my bucket and would just spin. So keep mixing in small quantities and once you get a fair amount mixed you’re going pour it into the mold. Before you pour though spray the entire interior of the mold with WD-40 so that the sink will come out of the mold easier when it dries.
Just keep mixing batches and pouring until your mold is full to the brim but not overflowing. Once your mold is full, grab a hammer and start tapping the sides. This releases all the trapped bubbles in the mix and you will see them float to the surface. This will take a while but keep doing this until the bubbles stop floating to the surface. For the last step of this process we’re going to smooth the top. I did this just with my hand but you can use whatever means you want. Once it’s smooth let it dry overnight.
Step 4: Removing the Sink From the Mold.
Now that the sink is dried, it’s time to remove it from its mold. To do this we are simply going to unscrew the sides and pull them off. Get the sides off and flip it off the bottom base board revealing all the foam we put in there earlier. Dig out all the foam using a utility knife until it’s all out. Voila we have a sink.
You might find that you have some holes in your sink from air bubbles that didn’t float up which were gonna have to fill. To fill these holes mix a little bit of concrete and rub it into the holes and once again let dry.
Step 5: Smoothing
Now that our sink is all dried and major holes are filled it’s time to smooth it out and polish. I purchased a pack of polishing wheels for my angle grinder with various grits. This is perfect for our needs to get a good shine and all the uglies off of it so pick yourself up a pack and go to town smoothing out all the sides. Keep getting finer and finer until you have a nice smooth finish.
Step 6: Painting
Painting the sink is where it all really comes together. Right now it’s just grey but we want classic white so I used white concrete enamel weatherproofing paint to seal mine.
Your sink might still have bubbles in it where the concrete didn’t fill correctly like mine did so to fix this I did numerous layers and put it on thick so don’t be scared to layer it on.
In my case I still had deep holes after using nearly all my paint since I used the wrong concrete so I had to cheat. I picked up some concrete caulk and painted it on by hand to smooth out the holes. You can do this if you want to try to hide any crimes you’ve had then sand it over after it dries. Then add one finishing layer of paint to make it pretty.
Step 7: Install the Drains
For the final step simply install the drains that you chose into our drain holes. The package should have instructions on it so follow those until you’re done.
Step 8: Closing
This was a fun and difficult project. I had never used concrete in this manner before so this was entirely new to me. Looking back on it I know I used the wrong kind of concrete as mine had lots of gravel in it and that's not what I was looking for and gave me a less than perfect finish but I'm proud of it for now. I still haven't installed it as of the writing of this since our home isn't ready for it yet but I will be sharing that process in the future. Thank you all for following along my first instructable.
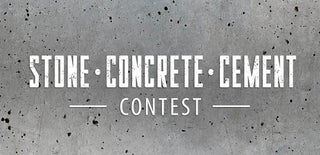
Runner Up in the
Stone Concrete and Cement Contest