Introduction: Create Your Own Headphones From Raw Materials
Here we will create some personalized Headphones, starting from raw material!
We will see the working principle, how to make a poorman™ version of a speaker with just a few raw materials, and then a more refined version using 3D design and 3D printing.
There are several steps so this Instructable is a bit complex.
Supplies
- Software for 3d design
- 3D printable material (liquid resin for 3d printer)
- Optional - materials for electroplating
- enameled copper wire
- magnets
- 3.5mm jack connector
- Stereo audio wires
Step 1: How Do They Work?
A speaker is basically made up of the following parts:
- A vibrating membrane.
- A coil, connected to an audio source (PC, smartphone, mp3 player)
- A permanent magnet
Here you can see two different ways to create a speaker:
- Method A: a permanent magnet (small, with a good magnetization force) is glued to the membrane. The membrane is free to oscillate, fixed only on its perimeter to the speaker body. The coil is glued to the speaker body.
Method B: a permanent magnet (small, with a good magnetization force)
is glued to to the speaker body. The membrane is free to oscillate, fixed only on its perimeter to the speaker body. The coil is glued to the membrane.
Step 2: Building the Poorman™ Version of the DIY Speaker
These are the basic steps to make the poorman™ version of the DIY Speaker:
- Take about 3 meters of enamled copper wire, 0.1mm thickness
- Cut a rectangular piece (about 6x20mm) of membrane retrieved from an envelop (the slightly opaque ones work better)
- Wrap the rectangular piece around a pen, keep it closed with a tiny drop of superglue
- Wrap the enameled copper wire around the membrane cylinder, leving about 3-4cm free at each end
- When you have finished wrapping the coil, put some tiny drops of superglue to keep in shape the coil
- Remove the coil from the pen, and with some patience, you should be able to remove the membrane cylinder, leaving only the copper wire coil
- Take any cylindrical piece as the body of the speaker. Here we used an almost empty roll of tape.
- Cut a disc of membrane retrieved from an envelope, same size of the "body of the speaker".
- Glue the border of the disc to the "body of the speaker".
- Glue the copper wire coil to the center of the membrane disc.
- Using the solder, remove the insulation of the copper wire at the to ends and put some solder on it
- Solder an audio jack, even recovered from old heaphones, to both ends of the coil
- Glue some magnets to a piece of solid cardboard. They will have to fit under/inside the coil, without touching the coil or the membrane. You may have to move the magnet up or down until you find the optimal distance.
- Connect the jack to an audio source (if it is a phone, set colume to max), and enjoy!
Step 3: Toward a More Refined Version
Now that we have seen that the concept works, the next step is to make them even more refined.
I had some ideas for this next version:
- body 3d Printed with a resin 3D Printer
- two different materials for the headphone body and the heaphone holder
- same working principle of the poorman™ version
Step 4: 3D Design and Preparing to 3D Printing
This step requires some 3d Cad modelling skills.
- First I downloaded a reference 3d model of a ear: https://grabcad.com/library/ear-model-like-iec-of-...
- Then imported it into 3D Cad Program
- I started modelling an ergonomic support for the headphone
- As a separate body, the shell or body of the speaker
- I also modeled a protective grid to preserve the delicate membrane
- After some hours of work, I ended up with some STL files ready to be 3d printed
You can find the STL files attached, ready to be 3D printed.
At this point, you need to add supports for 3D Printing with resin. This is easily done with ChituBox software (free).
Step 5: 3D Printing and Post Processing
To make things even more interesting, I decided to use Glow in the dark 3D printable resin: https://www.lumindustries.com/3dresins/hzartglow
After 3D Printing, you need to clean very well the 3D Printed parts (with IPA, alcool, or other cleaning products.
Now it is time for UV port curing with UV Lamps.
To make the final product even cooler, I decided to do copper electroplating on the headphone supports.
I suggest to check for separate tutorials for this step, that involves spraying the 3D printed part with graphite and silver spray, then put the part into a chemical solution with constant electrical current for about 20 minutes, to allow depositation of a thin layer of copper on the 3D Printed part.
Note: check the 3D Printed parts size by assembling them and trying to wear them, before time consuming finishing of the part. You may need to rescale the parts.
Step 6: Assembling Your Headphones
This step is basically the same of assembling the poorman™ headphones.
After some tweaking of the magnets position, the final result is quite nice!
I have a friend ( https://www.instagram.com/andrea_crazer/ ) who is very good at designing with Z-brush, a 3D modelling software that is quite complex, so he designed for this project some cool skull-themed shell for the 3D Printed speakers. 3D printing this part with glow-in-the-dark 3d resin made this part super cool to see!
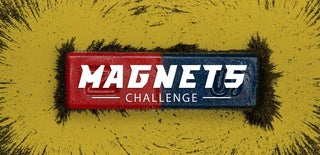
Second Prize in the
Magnets Challenge