Introduction: Custom Built Micro Hexacopter Frame
As an avid RC-er I had always wanted to build a multrotor, however it seemed too daunting. I met a kid at college that helped me through the process and I am now addicted. This is my 2nd multirotor with the first being a large quad built on an x525 V3 Frame run by an aeroquad mini. When Hobbyking came out with their integrated micro hex (link to the frame below) I knew I had to have one. Being brushless it would be plenty powerful to lift small cameras and other payloads. I ordered all the parts and built it in a night. After tuning my KK2 control board as well as I could (having had no prior PID tuning experience) I flew it. I ended up having to borrow an ESC programmer to kill all the voltage cutoffs in each ESC so it wouldn't just drop out of the air. After a few board glitches that poor little silicon frame had shattered irreparably. I was quite distraught. I refused to buy another one as I didn't want to wait a month to get it, nor did I want to pay 20 dollars for a sub-sufficient frame. I set out and did some research. I was shocked by how little I found about the subject. Nobody had a micro hexacopter frame of any kind (the one exception being blueskyrc.com). I continued searching and stumbled across polakium engineering's build. I liked the basic layout with the basswood and metal plates and landing gear (though admittedly it's not a super light frame). I stole the idea for the landing gear and the basic plate and basswood design. I decided to simplify mine in a few places and make some changes other places.
First of all I didn't want any hard shapes to cut with tin snips in the metal (I used a piece of ductwork sheeting that was about 7 bucks for a 1x3 foot sheet at Menards). I decided to make rectangular landing skids rather than tapered ones. I also only wanted to make 3, with only 3 feet it would sit stably however I wouldn't have to be nearly so precise so that 6 feet would sit perfectly when resting on a flat surface.
For the main plate I knew I needed a bigger one because I would have to fit a fairly large receiver (Spektrum AR7000) I also opted for a hexagonal shape rather than a circle. I printed off a few different size hexagons until I had the plate size I wanted. I decided to add tabs that I could fold up to hold different things, on the front there was a large-ish trapezoid for holding my voltage alarm, it velcros on the front and holds it at a nice viewing angle for when the multirotor is resting on the ground. I added a tab on the top plate that I could then heat shrink my satellite receiver to. Because RF is a key thing to consider in every RC application I decided I needed a receiver on top and bottom. I put my main receiver on the bottom for cleanliness and my satellite is attached to the top plate.
For my power distribution I had the main hub in the front section of the craft. I had to drill a hole in the center to run the back two motors through and a hole in the front arms to run the side motor's power through.
Since I had a KK2 control board I wanted to take full advantage of the screen and on-board programming abilities. I decided that I could cut and drill a piece of plexiglas to act as protection for the board while still allowing very easy and convenient screen viewing so that I wouldn't have to take the plate off to tune it or change settings.
Another change I made also comes into play with the top cover. Instead of using standoffs I decided bolts would be good. I found adequately sized holes and ran my bolts up through the bottom plate, through the arms, through the top plate, then added a nut to hold the main chunk of the frame together. I then added another set of bolts, rested the plexiglas on those and added a set of locknuts to the top to hold the plexiglas on.
All in all I ended up with what I think is a gorgeous frame. The wood doesn't allow vibrations to reach the board, and the board is also vibration isolated through 3M foam tape that holds it on. The result is rock solid flight with no oscillations whatsoever. My frame ended up with roughly 7 inch arms (14 inches motor center to far motor center), is much much much more rigid than the original PCB frame and comes in at a mere 3 ounces heavier (yes I realize that's a fair amount at this scale but it's still got a payload of roughly a half pound, possibly with a higher C rating on my battery It could output more power and lift more.
Also, Since I couldn't seem to find any tuning data online I will provide mine, I have not tuned the self level, but found I don't need to, I am used to collective pitch helicopters that don't auto level themselves so it makes sense to have a multirotor that will behave similarly.
Aileron and Pitch (linked):
P Gain: 28
P Limit: 85
I Gain: 16
I Limit: 30
Yaw:
P Gain: 50
P Limit: 20
I Gain: 50
I Limit: 10
And Finally my Setup
6 x Turnigy T1811-2900kv
6 x 6Amp ESC
6 x 5x3 Prop (3CW & 3CCW)
1 x Hobbyking KK2 Board
1 x 1000Mah 2s 7.4v Turnigy Lipoly battery (I have 3 but run one at a time)
You will also need a radio system 4 Channel minimum (Throttle, Aileron, Elevator and Rudder) but I am running with my Trusty DX8 and using a Spektrum AR7000 for my receiver. If you get a 5 channel you can then turn the auto level on and off remotely.
Please tell me what you think of my frame and vote for me in the "Up! 3D printer contest"
Links:
Hobbyking Micro hex frame:
http://www.hobbyking.com/hobbyking/store/__24380__Turnigy_Integrated_PCB_Micro_Hex_KIT_.html
Bluesky RC Micro hex frame:
http://blueskyrc.com/index.php?main_page=product_info&cPath=5&products_id=43
Polakium Engineering Micro hex frame:
http://polakiumengineering.org/?p=1506
First of all I didn't want any hard shapes to cut with tin snips in the metal (I used a piece of ductwork sheeting that was about 7 bucks for a 1x3 foot sheet at Menards). I decided to make rectangular landing skids rather than tapered ones. I also only wanted to make 3, with only 3 feet it would sit stably however I wouldn't have to be nearly so precise so that 6 feet would sit perfectly when resting on a flat surface.
For the main plate I knew I needed a bigger one because I would have to fit a fairly large receiver (Spektrum AR7000) I also opted for a hexagonal shape rather than a circle. I printed off a few different size hexagons until I had the plate size I wanted. I decided to add tabs that I could fold up to hold different things, on the front there was a large-ish trapezoid for holding my voltage alarm, it velcros on the front and holds it at a nice viewing angle for when the multirotor is resting on the ground. I added a tab on the top plate that I could then heat shrink my satellite receiver to. Because RF is a key thing to consider in every RC application I decided I needed a receiver on top and bottom. I put my main receiver on the bottom for cleanliness and my satellite is attached to the top plate.
For my power distribution I had the main hub in the front section of the craft. I had to drill a hole in the center to run the back two motors through and a hole in the front arms to run the side motor's power through.
Since I had a KK2 control board I wanted to take full advantage of the screen and on-board programming abilities. I decided that I could cut and drill a piece of plexiglas to act as protection for the board while still allowing very easy and convenient screen viewing so that I wouldn't have to take the plate off to tune it or change settings.
Another change I made also comes into play with the top cover. Instead of using standoffs I decided bolts would be good. I found adequately sized holes and ran my bolts up through the bottom plate, through the arms, through the top plate, then added a nut to hold the main chunk of the frame together. I then added another set of bolts, rested the plexiglas on those and added a set of locknuts to the top to hold the plexiglas on.
All in all I ended up with what I think is a gorgeous frame. The wood doesn't allow vibrations to reach the board, and the board is also vibration isolated through 3M foam tape that holds it on. The result is rock solid flight with no oscillations whatsoever. My frame ended up with roughly 7 inch arms (14 inches motor center to far motor center), is much much much more rigid than the original PCB frame and comes in at a mere 3 ounces heavier (yes I realize that's a fair amount at this scale but it's still got a payload of roughly a half pound, possibly with a higher C rating on my battery It could output more power and lift more.
Also, Since I couldn't seem to find any tuning data online I will provide mine, I have not tuned the self level, but found I don't need to, I am used to collective pitch helicopters that don't auto level themselves so it makes sense to have a multirotor that will behave similarly.
Aileron and Pitch (linked):
P Gain: 28
P Limit: 85
I Gain: 16
I Limit: 30
Yaw:
P Gain: 50
P Limit: 20
I Gain: 50
I Limit: 10
And Finally my Setup
6 x Turnigy T1811-2900kv
6 x 6Amp ESC
6 x 5x3 Prop (3CW & 3CCW)
1 x Hobbyking KK2 Board
1 x 1000Mah 2s 7.4v Turnigy Lipoly battery (I have 3 but run one at a time)
You will also need a radio system 4 Channel minimum (Throttle, Aileron, Elevator and Rudder) but I am running with my Trusty DX8 and using a Spektrum AR7000 for my receiver. If you get a 5 channel you can then turn the auto level on and off remotely.
Please tell me what you think of my frame and vote for me in the "Up! 3D printer contest"
Links:
Hobbyking Micro hex frame:
http://www.hobbyking.com/hobbyking/store/__24380__Turnigy_Integrated_PCB_Micro_Hex_KIT_.html
Bluesky RC Micro hex frame:
http://blueskyrc.com/index.php?main_page=product_info&cPath=5&products_id=43
Polakium Engineering Micro hex frame:
http://polakiumengineering.org/?p=1506
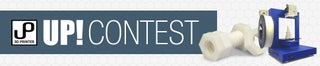
Participated in the
UP! Contest