Introduction: Custom Dress Watch From Scrapped Seikos
While browsing ebay one day, I came across an interesting Seiko movement, a 6347, with automatic winding and a moon phase watch. I ended up the only bidder, and a couple weeks later it arrived on my door!
I decided to build it up into a classy, moon phase, dress watch where I could practice adding a sunburst finish to watch dials. Little did I know how hard that could be.
Supplies
I use a number of specialised tools throughout this project including a watchmaker lathe, sandblaster, and DIY surface grinder. If you don't have access to such tools, I am hoping this still inspires you and gives some ideas. If you would like specific recommendations for tool, do let me know.
The watch is made from the aforementioned 6347 movement and a 6309 case. This is possible because the 6347 is essentially just a higher jewel count version of the 6347 with some of the dial side components replaced to facilitate the moon phase in place of the day complication. The dial and moon phase disk are made from zirconium. And the dial markers are made from 0.9mm diameter 304 stainless rod.
Step 1: Design
I use adobe illustrator for just about all my engineering and aesthetic design. I'm sure there are better tools out there for far cheaper but I do like that I can flesh out ideas aesthetically and then easily turn them into files for my laser cutters. In any case, here you can see some of the other designs I was trying, mostly in the same vein. My cousin convinced me to ditch both the date window and minute markers which I agreed would make for a cleaner look. I definitely did not remove them because I was not confident I could pull off either feature 🙃 (cut me some slack, the minute markers would be 0.3mm diameter!)
Step 2: About Zirconium
Both the dial and the moon phase disk are made from a sheet of zirconium metal. I chose zirconium because heating zirconium results in a layer of oxide forming that gives the metal this beautiful, lustrous, black/gun-metal grey finish. The deepness of the black depends on how polished the underlying metal is so because we are giving the dial a sunburst finish, the black won't be quite as dark as if the dial were highly polished before heating. Generally a watch dial would be made from brass or other copper alloy which might make some of the fabrication steps easier but I like the idea of the final finish being intrinsic to the metal, and it is far easier to do than trying to give the dial a nice painted or enamel finish.
Step 3: Preparing the Zirconium
I start by cutting the zirconium into manageable size squares with a hacksaw, comparable to the size of the final dial and moon phase disk. I then marked the centre of each square by drawing in the diagonals and drilled a small (1.6mm) hole at that centre. Finally, I marked a circle and roughly hacksawed off the the corners, then roughly ground the blanks into something slightly more circular.
Step 4: Polishing the Zirconium
To polish the zirconium I sanded on a flat slab of marble through sandpaper of the grits 240-320-600-1200-1500-3000-5000-7000. I then polished with a cotton buffing wheel and some polinum polishing rouge.
This was by far the worst step of this whole process as every time I messed up the sunburst finish or messed up later down the road, I would have to go back and re-polish the dial/moon phase disk all over again from 600 or 1500 grit. I think I would have repeated this polishing close to 50 times by the end of the process and it is quite long and physically taxing!
I also found that gluing the component to the superglue arbour that I would eventually use to apply the sunburst was a really good was of applying a consistent final polish as all the polishing mediums I used left some scratches so it was nice to at least have them be consistent.
Step 5: Sunburst
A close second worst step, also due to the number of times I had to repeat it to get the finish I wanted, was applying the sunburst finish on the dial and moon phase disk. I have tried a straight grained finish or a circularly brushed finish before which are both reasonably easy provided you do well on the polishing step. To get a straight grain, the dial simply needs to be brushed in a single direction on a fresh section of sandpaper and for a circular brushing you can apply sandpaper to a part bring spun in the lathe. But for this project I wanted to challenge myself a little more and try a sunburst, a classic finish for watch dials.
To arrive at this finish, a large abrasive disk is spun fast againts the part approximating a straight line across the surface from the centre to the edge. The part is then spun slowly resulting in lines radiating from the centre of the dial out. While it seemed reasonable in principle, i found that it was very hard to get a consistent finish with my setup.
I used a 3M radial bristle brush as the abrasive. In this case I used a 150mm/6inch, 400 grit (blue) wheel. I mounted it in a foredom style rotary tool using a hub I made from a stainless steel bolt on the lathe, and some laser cut disks made from acrylic (though I think they really should be made from polycarbonate or something besides acrylic as I was very afraid of the acrylic shattering at the speeds I was running the disk.
The rotary tool was then mounted to my mini lathe's tool post using a mount I cut from 6mm acrylic on the laser cutter. This allows me to feed the abrasive disk into the dial in a very controlled manner as it is spun by the lathe.
The dial was held in the lathe by a super glue arbor I cut from a length of 20mm diameter brass rod. This arbor was faced, and grooves were added to hold the glue (and help me centre the dial when gluing it to the arbor by lining up the hole in the dial with the central groove).
To actually apply the finish I ran the lathe at the slowest speed it would run consistently. I had to experiment with the speed of the rotary tool as it needed to be fast enough to approximate a straight line, but also slow enough that the bristles would conform to the flat surface of the dial and actually brush across the whole length rather than bouncing or bending away. Once I had run the tool for a couple seconds, I sharply pulled the rotary tool away, reversed the lathe, and repeated the process. This is where I would often get errors with uneven marks across the dial or discover that I had missed a scratch during polishing that would cause me to need to go back to the polishing step.
I also noticed early on that I was getting a ring or a number of rings of a different finish when I did this, I determined that the bristles were likely bouncing, causing a ring of second starts of the brushes. I remedied this by using some 180 grit sand paper to sand the bristles while they ran so that the tips of the bristles were not so pointy.
Step 6: Blackening the Zirconium
Once I was finally happy with the sunburst it was time to blacken the zirconium. This step is actually quite forgiving, all you need to do is heat the zirconium to a cherry red. I use a propane torch for this. I have found that the finish is not sensitive to the exact heat, nor how even you heat, nor how long you "soak" it in the heat. Once it has been blackened, the zirconium oxide layer is actually quite hard, albeit very thin. This means that there is less risk of leaving a scratch in the finish from say, dirt on your fingers, but it will still scratch if dropped or something.
I also had a little trouble at this step with my zirconium as two of my zirconium pieces ended up with small white dots that completely spoiled the finish. I noticed that these spots seemed to run perpendicular to the direction of the sheet so I am wondering if they are caused by residual stressed in the material. In the end, I used a different piece of zirconium to remedy this.
Step 7: Moon Phase Disk Sandblasting
The final finishing step for the moon phase disk was to mask off two circles to maintain the blackened sunburst finish and sandblast the rest back to bare zirconium. The masks are made from "sharp lines" blue masking tape cut on my CO2 laser. A flame tests reveals that this tape does in face contain chlorine so I DEFINITELY recommend getting proper, laser-safe, sandblasting tape instead of following me here. I originally tried sandblasting with my normal 50/50 mix of fine aluminium oxide sandblasting media and fine glass beads but this resulted in a very dark finish that was hard to differentiate from the blackened zirconium in some lighting. So I switched out my media with 100% fine glass beads which resulted in a lighter finish but with less sparkle than with the aluminium oxide added.
In the last photo you can see that on a couple attempts, I marked where o place the masking tape on the fibre laser to get things more accurate, but no matter how light I marked the zirconium, the circle still showed up in the final, sandblasted finish, so I wouldn't recommend doing this.
Step 8: Thinning the Zirconium
The zirconium was then thinned to the final dial and moon phase disk thickness (0.4mm and 0.15mm respectively) on a homemade surface grinding attachment for my belt grinder. You can readily buy such attachments, or even thin the parts by hand, but I personally made this surface grinder specifically to avoid doing either of these things!
In the photos you can see a couple of the techniques I use to get good results. I mark a hatch pattern with sharpie to see where material is being removed
Step 9: Cutting the Dial and Moon Phase Disk
The dial was cut on my 20W fibre laser cutter. Conventional wisdom suggests never buying a fibre laser under 30W and not using anything under 60W for actually cutting (as opposed to engraving) but I got a good deal locally on my 20W fibre laser, and though each of these cuts takes upward of 3 hours each, I still really love having it! The insane prices for fibre lasers are the only reason I don't recommend having one in every shop.
In any case, for both the dial and the moon phase disk, I glued the zirconium stock down before laser cutting it. This lets me spray water onto the cut to keep everything cool without fear of moving the part. For the dial, I then do enough passes with my first cutting file to cut a shallow pocket for the dial feet, and to give clearance to the moon phase disk. I found in a previous attempt, that the sharp inside corner of a simple pocket cut into the dial will actually show up on the finish on the front of the dial. So for this attempt, the centre pocket is actually made of a number of passes of circles of increasing diameter such that I no longer have a sharp corner on the pocket. I was afraid some artefacting would still show through but this actually worked perfectly and the dial ended up perfectly clean.
From there I load my final cutting file to cut out the dial, holes for the markers, hole for the hands, and hole for the moon phase.
You can see in the video that for the moon phase disk, I originally intended to cut a pocket in the back of the new moon phase disk for the old moon phase disk to fit into. This worked superbly to hold things in place! However, I never got it to work while leaving the finish on the front pristine so I scrapped this idea and ended up just thinning the moon phase disk all the way down to 0.1-0.2mm thickness with no lip to catch the old moon phase disk. This meant that cutting the moon phase just needed a single cut file to cut the outside and central hole and I cut from the front this time to ensure I was centred on the moon phases properly. Doing things in this order, however, left serious burn marks on the zirconium. Not such an issue in this case as the burn marks are not visible through the moon phase cut out, but it means I still don't have an optimal order of operations for future zirconium dials.
Step 10: Drilling the Dial
The hour marker holes were drilled to 0.7mm with a 0.7mm carbide drill bit. You can buy sets of 0.1-1mm carbide drill bits from Aliexpress or similar vendor for very cheap. I have a number of packs as even the larger carbide bits of this quality are very brittle, let alone at sub 1mm diameters! That said, I don't use anything special drill press wise to drill such small holes, just a second hand Ryobi drill press. You don't get very much feedback from the drill press handle with this size drill but you can still see a lot about how the drill is cutting provided you have enough light and good enough eyes! While drilling I covered the face in tape I cut on the CO2 laser with holes around each marker hole. I would have preferred to just use regular tape and drill from the back, however, the central clearance ended just at the edge of the marker holes and I was afraid the bit might wander if drilled from the back.
I then went under the microscope and using a 1mm carbide drill, chamfered each hole. Using a drill is not the cleanest way to make a chamfer but as the chamfers will end up under the final dial markers anyway, it is not such an issue.
I also drilled the centre hole to 2mm but I got so excited about the next steps that I forgot to do this until after gluing the hour markers and dial feet in
Step 11: Cleaning the Dial and Moon Phase Disk
Cleaning was actually a far more involved, and interesting, process than I expected. After laser cutting the dial, there was heavy residue embedded in the texture of the dial. I initially assumed this was just superglue and left the dial in acetone in the ultrasonic cleaner which didn't remove everything. I ended up with two stubborn stains.
1. Large, dark staining across the dial
This stain was resistant to my normal solvents (IPA and acetone) and I didn't really wan't to scrub too hard as it was all across the centre of the dial. I ended up removing this staining with a mix of ammonia and IPA in the ultrasonic
2. Small sections of light staining near the edges of cuts.
These stains got smaller to a point when using both IPA or acetone as a solvent, but at some point, they stopped diminishing. Looking as close as I can with my microscope, I suspect these are areas that got too hot and the finish there is mechanically ruined. However, as these sections are near edges, I am ok with it.
For final cleaning, I find there is nothing better than Windex. It wets the surface really well, picks up oils from your hands really well, and does a great job leaving a streak free finish #notsponsored.
Step 12: Making the Indices (hour Markers)
The indices are made from 0.9mm 304 stainless steel rod. I originally designed the watch to have minute markers as well but after receiving the 0.3mm stainless rod and seeing how thin it was I decided that may be too hard for my current skill level!
The shape I was trying to make for the hour markers is shown in the second image. I used a basic watchmakers lathe (interestingly, the lathe was manufactured only a couple minutes drive from where I currently live in the late 40s/early50s!) which is similar to a Lorch 6mm lathe.
This is the first time I actually used a watchmakers lathe so I made maybe 7-8 to practice before making my final 12. The whole process is better shown in video but starts by rounding the end with the graver. Then I use the 3mm square graver to mark out where I need to reduce the marker to fit into the 0.7mm holes drilled in the dial. Then I used the smaller (roughly 1mm square) graver to reduce the pin. I measured with a set of dial callipers and stopped when the diameter reached ~0.64-0.66mm as I found any bigger was hard to insert, even with a chamfer on the dial holes and the dial holes presumably measuring >0.7mm after drilling.
After reducing the pin, the domed end was roughly polished with 3000-5000-7000 grit sandpaper glued to popsicle sticks and then a final polish was applied with some polinum polishing compound on a stick of pegwood that I had whittled a flat onto.
Finally, the pin was parted off leaving 0.4-0.5mm to the pin length. Before the marker was fully parted off, I applied a chamfer to the back of each pin with a graver for easier application into the dial.
P.S. For the real watchmakers asking, I am also using gravers I made for hand graving and didn't want to resharpen unnecessarily, hence why the smaller one has a heel
Step 13: Gluing the Indices to the Dial
Once made, the indices are simply placed into their respective holes, and glued from the back with Loctite 480. I apply the loctite with a cheap watch oiler. I then sanded down the slight protrusions on the back of the dial with a diamond stone.
Step 14: Gluing the Dial Feet to the Dial
The dial feet are also glued in with Loctite 480. In my rudimentary testing, Loctite 480 works better than jb weld or regular superglues for this application. The dial feet were roughed up with a knife before gluing in to give more surface area for the glue to bite into. On the dial side, the fibre laser already leaves a rough surface, perfect for glue adhesion.
Step 15: Gluing the New Moon Phase Onto the Old Moon Phase
My original plan with the moon phase disk was to separate the wheel from the disk and use only that glued to the new disk. However, I didn't like my chances of messing something up and a new moon phase disk would be hard to come by so I decided to just glue the new disk directly on top, hence the shallow pocket I cut from the dial to give the disk extra space for the added height. I used gs hypo cement for this task, first placing a few dabs between the two disks, and once that was dry, I went around the seam at the back.
Step 16: Servicing the Movement
I disassembled, cleaned, reassembled and lubricated the 6347, while stealing newer parts from a nicer, more readily available, 6309 where possible. I am not a great watchmaker, still very much learning, so I would not be comfortable giving advice and servicing is beyond the scope of this Instructable but do let me know if you need recommendations of how to learn.
The only interesting parts about servicing the movement was 1. the train of wheels on the 6347 is actually slightly taller than the 6309, as is the movement ring. I didn't realise at first but these modifications are in place to give a tad more room for the moon phase and supporting components. So I originally assembled with the 6309 train of wheels and was very confused why my hands didn't reach the tubes there were supposed to seat on!
And 2. I left off the date wheel when reassembling as the way I designed the moon phase disk and dial, the date wheel is no longer visible, and can only serve to foul on the moon phase.
Step 17: Final Assembly
Final assembly time! I first pressed in a new mineral glass crystal from Cousins UK. I used the same crystal gasket though as cousins only stocks white and I definitely wanted a black gasket for this watch.
Then I placed the new dial on the watch, advanced the time until I saw the moon phase change (as I want this to happen at midnight) and installed the hands pointing at 12:00. The hands are just dauphine hands off ali express for an NH35 (same sizes for the 6347) but be wary as there are varying quality hands out there. These particular ones are really nice though!
Finally, I could do a final clean under the microscope, case the watch, add a black leather strap, and enjoy my work!
Step 18: Closing Thoughts
Finally, here are a couple more pictures of the watch under different lighting, and some final thoughts.
- Finishing is hard and takes a lot of time. I didn't expect what essentially amounted to two components to take me so many hours to get right.
- The 6347 actually doesn't fit perfectly in the 6309 case as the dial on the 6347 sits slightly further from the dial to allow extra space for the moon phase disk. All this means is that I had to use a smaller o-ring on the stem as otherwise, it was too close to the case back. This very likely affects the waterproofness.
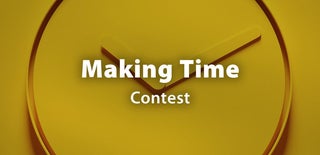
Runner Up in the
Making Time Contest