Introduction: Cute and Tiny Stepper Motors
The general perception of Stepper Motors nowadays is the ones used in the 3D printers, that is Nema 17, but to my surprise, I came across some really weird stepper motors on one of my expeditions on Aliexpress, the fascinated by the fact that they are not just tiny motors but full-fledged bipolar stepper motors made me order some of them for just a bit of tinkering.
It turns out that the motors do not need much of a hassle to get them going, as they have very minimal current requirements(I don't know exactly how much), hence, can be directly powered through Arduino's Pins.
Let's get started!
For those who would rather watch a video tutorial, here it is, however, I would recommend watching the video to at least get the idea of how it actually works!
Step 1: Things Required
Not much of a list here.
1.) Arduino (I used mega, you can use anything Arduino compatible)
2.) Stepper Motor (I bought them off Aliexpress)
3.) Soldering Iron (To solder some wires to the motors)
3.) A computer to upload the program to Arduino
Step 2: Getting the Stepper Motor Ready
This is probably the most delicate part, considering the tiny size of the motor that has to be soldered on the wires to be connected to Arduino, most of the stepper motor of this size has flexible PCB attached which consists of four wires of two coils.
I separated the individual wires on the PCB by cutting through an old school razor blade so that it would be easy to solder on the wires connecting the coils.
After separating the wires, get rid of the insulation and solder the wires, for wires I used some 16 Guage Enamel coated wires usually used for winding motor coils.
Step 3: Connect the Motor to the Arduino
This is an easy part, the bipolar stepper motor has two coils so four wires, each of which will be connected to the digital pins of the Arduino in the following way.
Pair 1 -- Pin 8 and Pin 9
Pair 2 -- Pin 10 and Pin 11
Step 4: The Stepper Library
As described in the intro, the Stepper Library is inbuilt in the Arduino IDE so you don't need to install it, with this library the stepper motor can be driven directly through the pins of Arduino, this only works in the Full Step mode though.
I don't know the current requirement of the Motor but, being so small, I drove it directly off Arduino's pins for quite a while without any problem.
Step 5: Upload the Program!
Inside the Arduino IDE, go to Files->Examples->Stepper->stepper_oneRevolution. Upload the stepper_oneRevolution to Arduino, but make sure the pins associated with the pairs of coils are the same as you plugged in.
Finally, Upload and you will see your cute little Stepper motor up and running. If you want to see how it works, I recommend watching the video attached int the intro.
Thanks For Reading!!
Regards,
Tanishq
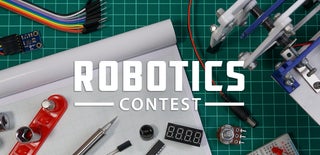
Participated in the
Robotics Contest