Introduction: DICE STOOL
In this instructable I show how I made a dice stool out of a block of solid Ash. There is a mix of chainsaw, angle grinder, router work & sanding! Overall it is quite an easy project and would be an ideal project for a beginner to start with. The dots are routed into the block on each side and highlighted in black paint. I will go over a few other options later on how you could do this differently. Lets begin!!!
Supplies
Materials:
Block of wood
Black paint
Varnish
Tools:
Chainsaw (rough cuts)
Planer (preferably electric)
Angle grinder (shaping & sanding)
Router
Sander
Extras:
Flap disc
Cutter for angle grinder
Paint brushes
Sand paper
Router bit (straight cutting)
Try Square
Hammer
Panel pins
Measuring tape.
Step 1: Have a Look at the Video Below.
Have a look at the short video above to see how I built the dice stool from start to finish.
Step 2: Ash Wood Timber Block.
I used a solid block of Ash that I had in my shed for a few years but any wood could be used for this project. The Ash had being well seasoned by the time I used it so the chances of shrinking and cracking were minimal. The tree was felled in 2017. If you do not or cannot get a block of wood that size you could always glue multiple pieces of timber together until you get the required size needed.
If you want to have a look here is another similar project I made using a similar size block of wood from the same tree. Twisted Stool
Step 3: Marking & Cutting Rough Shape. (4 Sides With the Grain)
The maximum size I could get from the Ash I had was 360mm (14 inches +) To make a template I got a scrap piece of wood, marked and cut a square 360mm x 360mm and placed it on the end grain section of the block of wood and marked the outline of the square.
A chain saw is the quickest and easiest way to cut out the square..Health & safety!!!!! Please read, understand and follow all precautions when using tools and machinery.... I free hand cut out the rough square , my chain saw was not big enough to cut all the way through in one go so I had to cut as far as I could on one side then swap sides and finish the cut from the other side.
Step 4: Plane and Straighten the Sides (4 Sides With the Grain)
The chain saw cut leaves a rough cut and finish so I used an electric planer to smooth and straighten out the edges. Regularly check the sides are square by using a try square. I took my time doing this step as I wanted to be as accurate as possible.
Step 5: Marking & Cutting Rough Shape. (end Grain)
Now with the 4 sides squared and cleaned up I was able to mark and cut the last two sides . I used the template I used at the start to mark the top and bottom. This time I was able to use the try square to mark all the around the piece so it would be easier cut with the chain saw. Having the two square lines makes it easier to cut rather than doing it by eye. Once again the chain saw made easy work of this and I tidied up with the planer. It is a lot harder to planes the top and bottom as it's the end grain. When all that is done you should be left with a perfect cube!!
Step 6: Marking to Look Like a Dice.
If you wanted to you could leave it totally square but I wanted to add more detail to it. With the template used to mark out the size (360 x 360mm) at the beginning but now reduced to 320mm x 320mm I used it to mark where I was going to be adding some curves. I added curve to the sides and rounded the corners like in the pictures. The size of the curves are totally up to you. Just remember the bigger the curves to more material that will have to be removed. I centered the template on each of the six sides ad drew the outline with a pencil.
Step 7: Shaping the Curves.
To shape the curves I used my 4.5 inch (115mm) angle grinder fitted with a cutter. The one I used was a speedcutter or Termit cutter from Graff. There are many other make of cutters like these so use whichever you can get, just be careful when using them as they can sometimes kick back. This part of the shaping and sculpting is all done by eye. I just started by removing a little material then rotating the piece again and again ensuring that I was keeping all the side uniform in shape. I kept at this until I was happy with shape and that it looked equal on all sides. I then switched the cutter to a flap disc (80 grit) and started to smooth out any imperfections left by the cutters.
Step 8: The Dots.
To router out the dots I again made a template. The template just ensures that all the holes are the same size. I cut a hole in a piece of wood with a hole saw but you could also use a jigsaw or coping saw. The hole saw I used turned out to be a little over 65mm (2.5 inches) in diameter. Obviously a dice has sides with 6,5,4,3,2and 1 dots so I divided them up accordingly. I centered the template then pinned it to the dice using some panel pins. These are small nails and are strong enough to hold the template in place while routing but easy to remove an only leave a small mark which is easy to fill or sand away. Using a straight cutting bit in my router with a collar I set the router depth to only about 4 mm and removed the material on all the dots.
Step 9: Painting the Dots.
I was initially going to use epoxy to fill up the dots but when I did a test the epoxy seeped into the grain especially on the end grain parts and did not look very well so I decided to just us some black paint to highlight the dots. Another ways to do it would be to add an inlay with a different color wood to highlight them or just do nothing at all and leave the natural.
To paint the dots I used a regular black paint and gave it two coat. It is better to over paint the dots as when you are giving the dice a final sanding it will give you a nice clean line around the dot.
Step 10: Sanding.
After all the black paint had dried I gave the whole dice a good sanding, I started with a belt sander reducing grits to finally sanding by hand with very fine sanding pads. The finer the sanding the better the final piece will look when it is finished.
Step 11: Finishing.
There are many ways the wood could be finished e.g.. wax, lacquered, painted, stained etc. but I choose to go with a hard wearing varnish. It will protect the wood and also show off the beautiful grain of the Ash wood. I applied three coats of the varnish allowing drying time between coats and giving it a light sanding before the final coat.
Step 12: The Finished Piece!.
And here is the finished piece! I am really pleased on how it turned out and it has now taken residence in my daughter's bedroom. Let me know what you think of the build and what if anything you would change or do differently. Thanks for looking. If you would like to see more projects from me visit my YouTube channel here: Eamon Walsh
Thanks again.
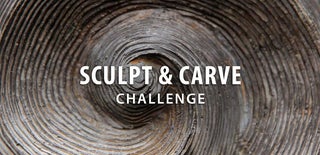
Runner Up in the
Sculpt & Carve Challenge