Introduction: Hammered Copper Coffee Table
In this Instructable I show how I made a coffee table using an old copper water cylinder and parts of a disused IKEA bed frame. The water cylinder was removed from a house as it had a hole in it and the "KURA" IKEA bed was my sons which he had out grown. The whole project is almost made entirely from items that were to be discarded but instead have been turned into a useful, practical hardwearing and not bad looking table.
TOOLS:
Angle grinder.
Tin snips.
Miter Saw (optional)
Hand saw.
Screwdriver.
Ball pein hammer.
Drill.
Paint brush.
Sander.
MATERIALS:
Copper cylinder or sheet.
40mm x 40mm wood (I used parts of Ikea bed)
18mm Plywood.
Glue.
Screws.
Paint
Primer.
Step 1: Have a Look at the Video Below.
Have a look at the short video above to see how I built the hammered copper coffee table from start to finish.
Step 2: Dismantle the Cylinder.
To start I just dove in and cut the top and bottom off the cylinder off with my 115mm (4.5 inch) angle grinder. Copper is a soft metal and is easily cut. If you do not have an angle grinder it can be easily cut with tin snips. The insulation that was surrounding the cylinder would have to be removed first though. Once the top and bottom were off I removed the coils of that are inside the cylinder. These were a little tricky to remove as it was difficult to get the angle grinder in at the right angle to cut the pipes. When I eventually got them cut they easily slide out. The pipe connections that enter and exit the cylinder were located down one side of the cylinder. I cut a line down either side of these the full length of the cylinder to remove them. I was then left with a sheet of copper albeit covered in insulation and in a circular shape.
Step 3: Flatten Out, Remover the Insulation, and Clean Up.
I placed the copper on a bench to flatten it out and remove the insulation. The insulation was pretty easy to remove, I just used the flat part of a try square to get between the insulation and copper and broke it off. The insulation left some residue on the copper which I could not scrape off. I did not want to push too hard in case I scratched the copper. To get the bulk of the residue off I used an electric sander with a fine grit sandpaper. There was a few imperfections in the copper so I had to use some fine sanding pads and do these by hand.
Step 4: Cutting Copper Size.
I wanted a coffee table 100cm x 55cm in size but as you can see in the pictures and video the copper was bigger than that so a bigger table could have been made or even some smaller ones. When the copper was flattened out I realised the was a seam in the copper where it had been joined in the cylinder manufacturing stage. The plan before I started the coffee table was to have all the top finished with the hammered effect but when I noticed the seam I didn't know what I was going to do! If I had done the whole top with the hammered effect I do not think it would have looked great with the seam in it. I thought about trying to cut the seam out but would have had to make the table smaller. In the end I decided to keep the seam in but just have the hammered effect up to the seam and then keep the rest smooth. I set the top out around the seam, planning to have approximately 3/4 hammered and 1/4 smooth. I marked the copper with a pencil allowing approximately 100mm (4inches) extra all around to allow for the copper to be folded down the sides and underneath. I cut the copper to size using a tin snips and set aside the rest to be recycled at a metal recycling facility at a later date or make something else from the leftovers.
Step 5: Table Frame. Cutting List.
I wanted to keep the frame as simple as possible, both in making it and in design. I decided to go with just a simple 40mm x 40mm frame using parts of the IKEA KURA bed frame. The frame consists of a top section an identical size bottom section and four legs connecting the whole lot together. The cutting list for the frame is :
4 @ 1000mm x 40mm x 40mm (45 degree cuts both ends)
4 @ 550mm x 40mm x 40mm (45 degree cuts both ends)
4 @ 330mm x 40mm x 40mm (Square cuts)
I predrilled some holes for plugs to cover the screws then I glued and screwed the top and bottom sections first before gluing and screwing them together with the four leg (square cut) pieces .
Step 6: Finishing the Frame.
After allowing the glue to cure, I filled and sanded any imperfections in the wood frame. I applied a coat of wood primer and let dry. I then applied 3 coats of a black water based paint giving the frame a light sanding before the final coat.
Step 7: Table Top.
The copper is only about 1mm thick so it needed a support to hold it up and also attach it to the frame. I got some 18mm (3/4 inch) plywood and cut a piece 1000mm x 550mm and cut some strips about 75mm (3inch) wide. I glued and screwed these strips around the edge of the top to make the top seem thicker.
Hammered effect
The hammered effect in the copper is simple to achieve, it just takes a lot of stamina in your arm!! You will need a ball pein hammer https://en.wikipedia.org/wiki/Ball-peen_hammer to get this effect and it is simply a matter of hammering the copper! You will get a feel of how hard you need to hit it after a few goes.
Attaching the copper to the plywood.
After my arm had recovered from all the hammering I stuck the copper to the plywood with some strong silicone. I used Tec7 . After applying the silicone I added some heavy weights to the plywood and copper to ensure any lumps were flattened out and that they bonded together correctly.
Folding the corners:
As I said earlier copper is a soft metal and pliable. The corners need to be cut to fold it properly so I set out some pencil lines of where to cut (see pics and video) and cut these with the tin snips. I then folded it as far as I could by hand and then using the flat side of the ball pien hammer hammered the copper around the corners as neat as possible. When I folded it around the bottom side I used some nails to hold the copper in place.
What finish?
I used a compound paste to clean the copper one last time. In the end I did not put any finish onto the copper as I want it to darken up and colour over time. To keep the shiny polished look a lacquer can be added .
Step 8: Joining the Top and Frame.
The joining of the top was very easy. I just had to place the top onto the frame and the attach it with some 60 - 70 mm screws. As the table was going to be on a wooden floor I attached some felt floor protectors to the bottom of the frame.
Step 9: The Finished Piece!
And here is the finished piece!! Let me know what you think of it and what if anything you would change or do differently. Thanks for looking.If you would like to see more projects from me visit my YouTube channel here: Eamon Walsh DIY
Thanks again.
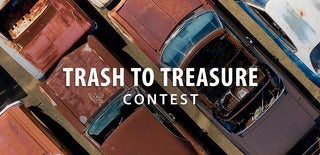
First Prize in the
Trash to Treasure Contest