Introduction: DIY Band Clamps | Step by Step Woodworking Tool
If you go to any woodworking or hardware store worth it's nuts and bolts, you'll probably find some band clamps for sale. They're not particularly cheap, a pair of standard size ones come in at around $20 for a pair. Depending on size, they're a touch cheaper or more expensive. They're built well. However, what if I told you that you could make an extremely affordable option for a fraction of the cost. In fact, for the same price as two, you could make a string of nearly twenty. Well look no further. These band clamps are awesome for applying pressure from three different points: top, bottom, and outside. They're clutch for applying hardwood or standard edge banding and are also good just as a hold for jigs or when you just need the assist from your invisible friend in the shop that doesn't exist. If you do have an invisible friend in the shop that does exist, I suggest getting professional help.
Supplies
27" long x 1 1/8-1 1/4 bicycle innertube
spring clamps (any brand will do but home depot has the anvil ones for .99/clamp)
box cutter or knife
marker/chalk/colored pencil... just something that you can mark with
bucket of water with a couple squirts of dish soap or simple green
small ruler or tape measure
scrap block for straight edge cutting
rope to hang the clamps on when you're done and to make a cool necklace
Step 1: Prepping the Clamps
These spring clamps usually come with a rubberized guard on the mouth. I go ahead and take all these off. If you're into being overly clean you can give your clamps a scrub down or even hit them with a wire brush in a drill. But in my opinion, for .99 cents I'm not going to take a ton of care with these so I just rip the rubberized guards off and call it a day. They're tools at the end of the day and they are going to get beat up.
Step 2: Inner Tube Prep
The most work is going to come from preparing your band, aka the inner tube. I cut mine into 5" lengths. You can go a bit shorter if you like, probably to about 4" at the smallest. I just try and not go too long because it reduces the clamp's ability to apply the third point of pressure, from the back of the mouth, which is the whole point of using these. I start by cutting out the valve stem first and then just measuring 5" along the way and slicing across the width of the tube. These cuts don't need to be perfectly square. You just need to get in the ballpark and the scrap block I have with a relatively straight edge is a good tool for doing so.
Then I measure an inch from either end and strike a cut from the center of the inner tube outward toward the edge. There's usually a seam in the rubber at about the middle so you can really just eyeball it. I then line up my ruler and strike down that seam to cut out a rectangular patch of the rubber. This helps make the piece between the jaws a bit more malleable and stretchy and allows for this to perform more like your traditional band clamp. I imagine you could just take the 5 inch tube, uncut, and try the same, but it would be stiff and probably semi-rigid at points and bind on itself.
After, to remove the talc on the inside of the tube (a YouTube viewer let me know what the inside powder was), I just wash the insides of the tube in warm soapy water in a bucket. You can do it at the sink. It doesn't matter. Then dry it off and you're ready for assembly.
Step 3: Assembly
Assembly is pretty easy. You slip each end on to one of the jaws of the clamp, the cut side faces inward toward the mouth. You tuck in the band between the jaws and you're done. No adhesives are required to keep the band fixed. If you want to, you could use some hot glue to help fix it, but it's really unnecessary. I also like the ability to be able to remove these in the event that one of the bands gets damaged. However, just for frame of reference, I made my first batch almost two years ago and I've only had to replace one band, so unless you're overly hard on these, you shouldn't have much trouble.
Step 4: You're Finished. Rejoice.
And now you've got a full set of band clamps to work with. You're finished. Rejoice. One of the great things about these band clamps is that the rubber is pretty resilient and resistant to finishes, glue, etc. When I've done a big glue up or lamination that involves them, the squeeze out is inevitable and it peels off the rubber like nothing happened. I like to keep these on a big long looped string that hangs on a hook in the shop, and that helps me have these all in one place and keeps me from losing them. They also make a lovely necklace. Tiny shop hacks for the win. In any event, if you're going to whip some up, be sure to tag me in your attempts or unique ways that you use them. If you have any questions hit me up in the comments below!
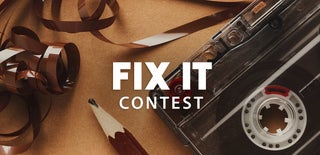
Participated in the
Fix It Contest