Introduction: DIY Box Spanner
Each time I do an oil change on my van, I come across a bit of a struggle when changing the oil filter.
The reason is that the cap of the bowl in which the filter is, needs to be unscrewed (has a hex nut shape on the very top). Unfortunately, I haven't got a proper spanner for that job, and I either use an adjustable wrench or flat spanner, or both of them combined, since there isn't any space available in the engine bay, and I can't apply much strength to crack open the cap in the positions available.
Therefore, I decided to build my own spanner, dedicated for the job in question.
(which happens to be my first welding project)
Step 1: Needed:
Tools:
-arc welder (bought a very old but good one for 40 euros)
-angle grinder
-other stuff (file, metal brush, hammer...)
Materials:
-small metal plate but quite thick: 8mm (would probably work with thinner...but not under 5mm...depending on the application)
-metal tubes (a 20mm diameter tube, and a 25mm diameter one...around 40cm of each)
(All materials come from stuff at work that were supposed to be thrown away)
Step 2: Cutting a Stripe of Metal As a Chocolate Bar.
The first thing you want to do is to mesure the lenght of one side of the hex nut you need to make a spanner for.
Then you multiply by six (number of faces in the hex shape), to get the lenght of the metal stripe you need to cut.
I also recomment to add 6mm to that (which I didn't), so you don't struggle to much on adjusting in the next step.
The plate needs to be wider than the hight of the nut you're making the spanner for. (a few millimeters will be enough.
Once you have your dimensions, cut the stripe.
Then draw cutting lines to the lenght of one side of the hex nut. (That's when you would add a millimeter to it) You should have 6 equal sections.
Now you can cut on all these lines, at around 2/3 of the thickness of the stripe.
The result is a chocolate bar look alike metal stripe.
Step 3: Bending to the Hex Shape:
It would be most convinient at this step, to work with a quite hot stripe. (I didn't maintain a good temperature throughout the process, and haven't been able to bend it in one piece.)
Clamp the stripe over a solid edge, lined up with the cutting lines made earlier. One at a time.
Hammer down the section hanging out.
Check for angle match with a corresponding nut.
Repeat for each section.
As my stripe cooled down, the metal wasn't so bendy anymore, and it ended up breaking once I'd bended 3 sections. Which I ain't sure is a bad thing, since when I started to bend the fourth section, I had to grind a bit of metal of, inside the angles created, so that the nut fit nicely. (bending rounded the inside and I think that adding a millimeter to each section, or slightly more, can prevent the inside lenght to shrink to much).
So I ended up with 2 pieces of 3 faces each. (which might be the easiest way to do, rather than one piece that has to bent around the nut, as intended at first).
Make sure it wraps the nut nicely, but not to tight! (adjust by grinding of, if necessary)
Step 4: Welding the Hex Shape:
Now all you need to do is to weld the two pieces together. (I used 2.5mm welding rodes here)
And then, having checked if it still fits the nut, you can fill the cutting lines. (Used 3.2mm rodes)
Check again for fitment, because the heat created by the welding can moves things around.
(I double checked on the oil filter cap as well this time...(last picture))
Then grind the excess of, for a smooth looking shape.
Step 5: Welding It As a Box Spanner:
Once grinded, place it over the rest of your initial metal plate, and scrape the shape on it.
I opted for scraping the inside shape, and added a couple millimeters to that, but you could probably scrape the outside shape as well, and shade a couple millimeters of.
Then weld it on top of the previous piece. (2.5 and 3.2mm rodes)
(check again for fitment)
Step 6: Tube Welding:
Only now, this will become a tool.
I simply welded a tube on top that (which happened to be the right lenght for my one purpose only spanner...even though I could have used a couple centimeters more)
And then, after checking for the desired position on the van, I welded the handle bars on that first tube. (was a smaller diameter tube cut in 2 pieces)
I welded the handle bars at an angle, so that my hands had enough room to operate. (if welded at a 90* angle, my knuckles could have catched on the bonnet lock)
I could have welded the handle bar in one piece on top of the other tube, to over come that issue, but it turns out that the tube I used for the spanner, was at first, a tube that is very helpfull as an extension to crack some harsh nuts and bolts. So I needed to still be able to use it this way.
After a bit of grinding, and brushing, to make the overall look ok, I finished a can of black spray paint on it.
And that is it!
Step 7: Application:
This spanner I made is very purpose oriented.
It makes my oil filter change a real pleasure, and it stays in my van at all time, to be used as an extension when needed.
But I think that the way I built it can be applyed for many weird located nuts and bolts, or weird acces to them, that require a specific spanner, therefore, often very expensive ones!
This method is fairly easy (was my first welding project, and had only pratice my welds once before), quite quick to make (made it in about 3 hours, not counting the paint job), and pretty cheap (cost me none, but even if you need to buy the metal, there is not that much needed). So I will propably be making more of these in the future...
Hope you liked it, and I'd be pleased to see people make their own.
Thanks!
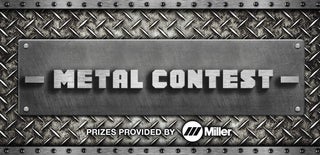
Runner Up in the
Metal Contest 2017