Introduction: DIY Concrete Swimming Pool
Building your own pool is not for everyone, but it can be done, with great results. When I got bids around $30,000 , the choice was to build it myself, or forget it.
For around $7000, and a lot of work, my son and I built a very solid 13' x 22' x5' oval concrete pool off our deck.
We built it on flat ground , but it could also be built in a hole and backfilled.
Keeping the plumbing simple also cut costs.
Block pools can have problems because they lacks the steel needed.
We used lintel block (normally used over doors and windows) to wrap rebar around the pool every 8 inches horizontally.
Stacking the blocks with cores lined up put a rebar vertically every 8 inches.
We cut the sides out of the base row of block to let rebar and concrete connect the wall and pool floor.
The result was a pool that could stay solid on the 3 ft. of rock backfill behind our retaining wall.
We plastered and waterproofed the pool ourselves with white surface bonding cement, and 2 years later hired a pro crew to do a finish coat of prettier blue cement plaster.
Step 1: Design
This pool had to be very strong, because it sits on backfill in an earthquake area next to the Sea of Cortez. The backfill was all rock, not dirt, which settles.
Block pools can have problems because they lack horizontal steel and they can leak where walls meet the floor.
Curved walls are much stronger than straight, so I chose an oval. I wanted #4 rebar every 8" vertical and horizontal in the walls and continuous through the floor. This is impossible with standard block, but lintel block has notches which let you add horizontal bars every 8"
We kept the pool 30" away from the retaining wall to allow access for plumbing and pump.
To use a small spa 1/2 hp pump we kept the 2"return and 1.25"supply lines large and close to the pump.
A cartridge filter completed the plumbing.
Waterproofing comes from the cement plaster inside a pool. Any crack in the structure means a leak, as the crack will continue through the plaster.
We used fiberglass reinforced plaster inside and out to hold the blocks solid until the concrete was poured cured. This alone waterproofed the pool.
Step 2: Structural Steel Reinforcing
Once the ground was flat, we poured a shallow footing for the block. This was to stabilize the walls until the floor/wall cores were poured. The pool weight load is spread evenly on the pool floor when filled with water so the strength this footing is not important later.
One row of block was set in mortar below the pool floor as a level base for the rest.
We ground all the block flat top and bottom. Then we glued (construction adhesive) one row of lintel block with inside cut out level with the soon to be 6" thick floor. A bent rebar is fed through every core, overlapping the 1' on center rebars in the floor. Every horizontal row of block gets a rebar in the notch of the lintel blocks, making a continuous rebar circle every 8 inches. The result was a pool that would stay solid on the 3 ft. of rock backfill with no wall/floor crack. The floor and wall cores are poured at one time.
Step 3: Wall Stack and Plaster
We drilled holes in the blocks for all the return and pressure pvc pipes, and cemented them in with expansive cement. Fittings are available to point the water flow in the direction you want it to circulate.
A floor drain tube ( 2" in our case ) gets positioned at the low point of the pool. Your temporary screeds should all go downhill to this drain so crud gets pulled to the pump/filter.
Installed the pvc return weir with expansive cement following their instructions. Normal cement shrinks, and leaves a crack.
Blocks are stacked with no overlap so cores match up. Any rebar is overlapped a foot and tied with wire. Blocks are stacked to the waterline. The inside and out of the block is plastered with 1/16" minimum thickness surface bonding cement to hold the block while concrete is poured. A rubber float makes spreading this easy. It dries quickly, so mix just a little at a time, and clean tools every 10 minutes, or kiss them good by.
Surface bonding cement (it has latex glue and glass fibers in it ) holds blocks better than mortar, and also waterproofs the wall. Our pool was was waterproof with a second coat on floor and wall after the pour.
A solid 12"concrete bond beam gets formed with 14" plywood. We wanted a vanishing edge so that part is formed an inch below the final water line to leave room for tile. This edge needs to be angled (we did down on the outside ) so water will not sit on the tile. We built a large catch basin below the edge, but I won't get into that. It is not easy to design the size of the basin.
Now you are ready to pour wall and floor.
Step 4: The Pour (get a Pumper)
We pumped ready mix over the house and first on the floor, then into the cores and bond beam in a continuous pour. Without the pump, you need a dozen strong men to hoist the concrete up in buckets- It is a lot of concrete, and you have to do it without stopping. The concrete cannot be runny, so you need a spud vibrator to consolidate the concrete in the cores and into the floor pour. You can rent these, or buy one for $100 at harbor freight.
The concrete should be 6.5 sacks/cubic yard and have both fibers and a water reducing superplasticizer admix. The pumper will want to add water for easy pumping, but you should add more water reducer instead of water. Too much water and you will get shrinkage cracks.
Remove any rocks or bricks holding up the rebar. The rebar must be in the middle of the 6" floor. Too high or low and it will rust and break the concrete.
Leave the surface rough, as in broom or wood float finish. The plaster bonds much better to rough concrete.
Cure the concrete for a full week. The floor is easy- flood it the next morning. Leave the bond beam forms on for a week and keep the top moist. The plaster on the walls keep them moist.
Step 5: Plumbing
It can be as simple as hooking up an above ground pool pump and filter with hoses over the edge.
We did ours with conventional pvc and a 20 year old 3/4 hp spa filter pump, later replaced with the same size, but two speed. You don't need a big pump. It just uses more electricity.
Step 6: Steps
If you do steps add them after the pour and the area below them is waterproof. They can take a lot of concrete. Next time I would go for narrow steps and more pool space. We poured a layer ( step) at a time and ended up adding lots of rocks and bricks as filler inside the concrete.
Step 7: Deck
Since our pool was free standing, we added a deck on two sides, all conventional concrete that overlapped the pool edge, leaving us with nice spot to enjoy the sunsets of San Carlos, Sonora, Mexico.
Approximate Costs
Lintel Block $600
Concrete 21 yards @$140/yd $ 2940
Steel $440
Plaster $160 (We made our own)
Glue $70
Pump $240
Filter $180
PVC plumbing $280
Total- about $5000
+ heFinal plaster and edge tile $2400 (two years later by pool plaster contractor- It is much prettier and smoother than my plastering )
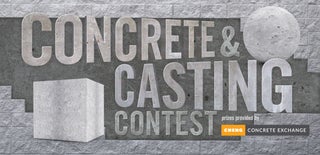
First Prize in the
Concrete and Casting Contest
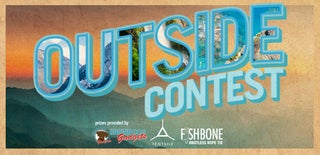
Participated in the
Outside Contest