Introduction: DIY Magnetic Drill Press
The whole idea is based on our latest conversion of drill press by using a brushless motor from an old hoverboard and that went great So we decided to built a magnetic drill press and as the name say, it will be able to stick to any ferous metal surface and drill a hole perpendicular to the surface.
Now we are going to use a Hoverboard motor as its an outrunner brushless motor and has got alot of torque. The whole unit is going to be a cordless unit and strudy enough to drill holes through thick metal sheets.
So time to dismental our beloved hoverboard first...
Step 1: DIY Magnetic Drill Press
We are going to use this hoverboard that has 6.5in wheels and they are the most common ones and you can get one from a scrap yard thanks to Chinese bulk manufacturing.
As we unscrew the plastic cover with the screws provided at the bottom side, we have the acess to the motor mounting as we removed the PCB mounted on top of that.
Now if you have ever ride on one of these pieces of tech, you know the crazy amount of power they have got, the two motors together can get you balanced rightaway. The motors are placed within the tyres itself and they are direct drive mean no gearing nothing at all. These are outrunner brushless motors and they have got plenty of torque and those of you who are not familiar, believe me with that sized motor we can pull a bunch of horses with the right speed controller. Yes they are three phase motors and need an ESC (Electronic Speed Controller), well more on that later.
Step 2: Dissmentalling the Motor
As we have got plenty of torque so the plan is to mount the drilling chuck directly to the the motor front but before we do that we have to get the motor dissassembled. There are six screws provided on rear plate that allows to undo the motor.
The motor comes dissassembled in three parts. The drum, stator and the back plate. Obviously we have got nothing to with the tyre so here it comes off with WD40 and not so gentle push.
Now there are two reasons to get the motor dissassembled. One is to mount the chuck while we have got to do some twiking to the stator, more on that later...
Step 3: Mounting the Drilling Chuck
The drilling chuck that we have got is usually used in drill press and this one is mounted to a threaded shaft provided on the drill press.
To mount the chuck to the motor fron we are going to use a 6mm thich metal plate thats cut down to the required inner and outer diameter whioch helps to self centre the plate inside the fron seat of the drum and the chuck aswell. First we stick the plate to the drum using some hot glue and drilled three holes that will be used to mount the plate to the drum front using 5mm allen screws. Later the chuck is welded to the plate from the rear side making sure that is exactly in the centre.
The plate is the sanded to have a flush seat on the drum face and then painted. As the paint dried we have mounted the chuck to the drum front.
Step 4: The Twist
With all the pros of using the hoverboard motor the con is the fact that its a hoverboard motor and doest offers a whole lot of rotational speed. Besides its designed for 10s lithium battery means that it originally operates at 42v and still its way too slow.
Now and ESC with that much voltage range comes down for a heafty price tag so rather we decided to use our RC car ESC thats rated at 6S lithium battery pack which mean slow guts much slower.
Now with our calculations we need to get three times the speed that we can currently get with the motor in stock condition using 6s battery pack.
Now rewinding the stator is not an option as the poles are very close together and we have tried to do that and believe me its way too difficult, atleast we were unable to get it done that way. The other way is to rewire the current winding. The stator has 27 poles, since its a three phase motor so each phase goes through three sets and each set has three poles. Currently all three sets of a phase are connected in series so it take more time for the current to complete a cycle and thus slowing the rotation of motor for a given voltage. Now we are going to rewire the stator with all three sets connected in parallel and hopefully we can get the current to get through each phase within 1/3rd of time achieving three time as much speed as of the stock winding.
Ealier in our drill press conversion project we have done that rewiring using a bunch of jumeper connection but this time we have to repack the motor and guys time to improvise...
Step 5: Designing and Ordering the PCBs
To get the science implemented thats discribed in the previous step we have designed our own customized Printed Circuit Boards. All we needed to do is to spot the position if the coils that needs to be connected in parallel and finilized the layout of PCBs.
Here I would love to thank NextPCB for making this customization possible so flawlessly. As we designed the PCBs we headed to NextPCB website. The process to order the boards is preety straight forward. Just upload the gerber files and as you go through the option provided there you are all done.
They are providing a vast range of services for manufacturing your customized Printed Circuit Boards and their assembly throughout the globe at a very reasonable price. So be sure to check out their website for some great quality PCBs.
The PCBs arrived within just a week and as appears in the pictures the quality was really good.
Schemati and Gerber Files can be foun here.
Step 6: Sottering the Boards to Stator
Before we sotter the boards to the stator we have to identify the sets belonging to each phase. We have marked them b y using paper tapes and the symbols R, Y, G stands for red blue and green associated to each phase. Then we took off the series connection between each set.
As we are done identifying all the connections we have removed the enamled coating and then placed the boards on top of the stator winding. At this point we have to make sure that the start point of each coil matches the starting point of the corresponding phase while the end point of all sets belonging to each phase are going to be connected together and are shorted on the PCB.
One all the connections are sottered to the PCB we then sotter three phase wire and assisted them out of the motor through the hollow shaft.
Step 7: Making the Body Parts
To built the structure of drill press we have used 6mm thick metal sheet . The sheet is 6 inch wide and thats the width of the drill machine so to make up the front panel, sides and the magnetic plate we cut through the required lengths.
To join all the parts together we have used 22mm square metal tubes. Two of them were used to connect the front plate to the side plate, later its also going to hold the slides for linear bearings. The other 22mm square bar is cut to 6 inch length thats going to hold the side plates together.
Besides that we have cut down a 6mm thich 2 inch metal strip to 6 inch wide thats going to hold the motor. All the holes were drilled and some of them were tapped.
Step 8: Painting the Parts
All the metal parts are than buffed,washed and then painted. We have used matt black and off white paint on all the parts except the aluminium spacers and the slides for linear ball bearings.
Step 9: Assembling the Structure
Once the paint dried we asssembled all the parts together using allen screws. First the front plate goes in place and then the side plated that sandwiches the small metal bar.This bar is later going to hold the electromagnetic plate.
Now to slide the motor vertically we have used15mm linear bearing slides and a pair of linear bearings. The are usually used in heavy industrial machines like CNC and lathes and the have good percision and load bearing capablities. To make the clearance between the structure and the motor drum we have used aluminium spacers cut down to 22mm in length. Ones we mounted the linear slides in place over the metal bars we placed the linear bearing and mounted the motor mounting plate on top of that.
Step 10: Building the Electromagnetic Plate
To get the drill press stick to a metal surface we need to built an electromagnet. For that we have used 6mm thick metal and three metal studs cut down to exact 22mm length so as we mount the plate over the metal bar the front of the metal studs must stick to the metal surface perfectly.
Since we have decided to use a 6s lithium battery pack for this drill press so we have nearly 22.2v to operate the coil. After a bunch of calculation we settled for a magnetic coil thats ratted for nearly 100 watts (22.2v and nearly 5 Amps). For that we have used 100 grams of 27 gauge enammeled copper wire on each stud.
We wound the coil using a temporary reel that we have made out using a spare stud and a pair of metal plates mounted on a drill. Each coil is wound using 100 gram wire and to keep the wire in place we have used super glue. Once we are done winding three coils we drilled the holes and taped the studs with 5mm threads. Later we mounteds the studs on the metal plate using 5mm allen screws.
To protect the coils from damage from metal shaving that will come off during drilling we have prepared a mould using PVC pipe arround the coils and later poured epoxy arround the coils.
As the epoxy dried we removed the PVC supports and painted the whole plate. Later we mounted the plate over the metal square on the rear side. To restrict the plate piviting we have used two 5mm allen screws on either side plate at the opposite end sandwiching the plate inbetween.
All the three coils are connected in parallel and together they draw arround 5 Amps at 22v and the electromagnet is way too strong. We tested is over a 6mm metal plate and i was unable to move the unit or deattach it from the metal sheet when the coils are energized.
Step 11: Motor Assembly and Mounting
Later we assembled the motor and the stators seems to fit nicely with enough clearance between the PCB and the motor housing. Next we mounted the motor on the motor holder using the motor mounting plates from the hoverboard. The motor fits perfectly in the centre of the linear slides with 2mm clearance on either sides.
Step 12: The Handle Assembly
To make the motor travel verticallywe need a handle. The assembly for handle is made using a hexagonbal metal rod with support pieces cut out using 1 in angle iron. As we cutdown and drilled all the pieces we assembled them on the frame as shown in the pics.
To make the motor retract we used a pair of springs (They are generally used in brake assembly of the local bikes) and they seems to do the job nicely.
Step 13: Electronics
To drive the motor we are going to use an RC car ESC(Electronic Speed Controller) thats ratted at 150Amps and 6s lipo 22.2v. The speed is controlled using a servo tester.
Besides that we have used a heavy duty SPST switch ratted at 20Amps to energize the magnetic coils. The input for both the ESC and coil are connected to the XT-60 connectors.
To power the drill press we are going to use two 3s 5200 mah lipo batteries that are ratted at 30c discharge rate. These are high discharge batteries and have enough juice to power this drill press upto 15 mins of continious drilling.
With that being done it was time to test this thing out.
Step 14: Testing the Drill
Everything come up perfectly together for this project and the finish product product was sturdy byound our expectations. The drill is compact, the slides were preety acurate with no visible erroe during the travel. The best part was the centre of gravity, as with the motor being one of the largest part we were expecting it to fall forward and make us breake alot of our precious bits but thing turned out to be in our favour. The centre on gravity was on the rear side and help the drill stand independently without any support.
Next we connected the batteries and powered the drill. With the servo tester the speed of rotation can be precisely controlled. We started with a 5mm hole and move towards larger holes using 22mm hole say, and this thing has got tons of torque supported by a solid electromagnet. The drill offers a clearance of 6.5 inch dia hole and have torque to handle such kind of job.
Overall the end results were great and we had lots of fun during the project. If you like this project then dont forget to vote us in the Magnets contest and do visit our Youtube Channel for more of such project videos.
Regards,
DIY King
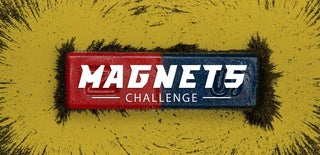
First Prize in the
Magnets Challenge