Introduction: DIY Offroad Lighting
Hello everyone. First of all, thanks for checking out my Instructable! I have been a long time lurker and have never contributed to the community. This is my first submission; that being said, I hope it inspires you to create something of your own.
For this Instructable, my roommate and I were interested in creating LED Light Bars for our Jeeps. During the time that we were working on this project, Light Bars were still running in the $350-$400 dollar range. We frankly did not have the cash to spend on commercial bars. This is where things got interesting.
Neither of us have a background in electronics or anything fancy. We knew the basics and we went with it. Over three years later our design is still fully functioning. Without further ado, the build!
Step 1: Gathering the Materials
So to begin, we really just stepped into the unknown. This was geared with budget in mind, so we bought the cheapest stuff we could find. I apologize for not having specific links to the build list, but this overview should help you get a better idea of the process.
We decided that we would build "pods" that could interconnect, allowing us to make the light bar as big or small as we wanted. With this design we would be able to custom fit our pods to any particular spot on the vehicle.
Materials:
- eBay star board LEDs (I believe they were 5K, which is a very white light output). We purchased the bulk packs to save on cost and to have extra on hand.
- eBay star board lenses (Throws the LED light output into specific degrees for flood or spot lighting. It all depends on what angle of lens you purchase).
- eBay drivers to provide constant current to the LEDs (Prevents flickering and power spikes from reaching the LED).
- 3M double sided thermal tape to adhere the star board LEDs to the aluminum bar (Also transfers heat from the LED to the aluminum bar acting as a heat sink).
- Aluminum bar stock to mount the LEDs to (Acts as a heatsink and is hollow to allow our wiring harnesses to sit in).
- Foam Spacers go inside of the pod to allow the aluminum bar to sit higher for a snug fit.
- Positive and negative wire (We needed wiring to create our harnesses to essentially daisy chain the LEDs).
- JST Connectors (Allowed us to plug and play each pod to one another).
- Conduit boxes (These were the cheapest and most effective casing we could find for the design. They have a tough body and a removable face with a gasket. The conduit boxes also allowed for us to create our pod system, as they can be attached and removed from one another with small PVC inserts).
- PVC tubing (Allowed us to connect our pods (conduit boxes) to one another).
- Lexan (We used Lexan as our protective lens. It is designed to be vandal proof and can stand up to the elements.)
- Soldering gun and solder (We needed this to create our wiring harnesses for each individual pod).
- Dremel (Used to cut out the lexan lens and the pod lens opening).
- Screwdriver (Used to secure the pod lens to the body).
- Truck bed liner (We wanted to give our bars a rugged look that could take some beating).
Step 2: Cutting the Heat Sinks
Our first real project was cutting the heat sinks. Aluminum is relatively soft and can be cut with a number of hand or power tools. We measured the inside of the pod and transferred that measurement to our aluminum stock so we could create a perfect snug fit. This also ensured that we did not waste any material.
Step 3: Placing the Thermal Tape and LEDs
We created a stencil that allowed for a relatively perfect fit of 12 LEDs per pod. We outlined the stencil with marker and then placed our 3M thermal tape. After the thermal tape was in place, we placed the LEDs onto the tape ensuring that each LED was properly positioned for positive and negative daisy chaining.
Step 4: Soldering and Wiring Harnesses
This is unfortunately the least documented section of our project. We soldered each row of 6 LEDs to each other using small pieces of wire (positive to positive, negative to negative). We then created harnesses using our LED drivers, wire, and JST Connectors (placed at each end of the pods). Each pod was wired identically with a JST connector on each side to allow for easy addition or removal of pods. It's simply plug and play. At the end of the pod that will feed to your vehicle, you simply connect a longer positive and a negative wire.
We ensured each harness was shrink wrapped and very tidy to prevent crossing of wires. The picture above shows the basics of the harness in raw form. You are also able to see the PVC tube spacers and the foam spacers inside the pod.
Step 5: Prepping the Casings
During the process you are constantly ensuring fit, placement and functionality of all components. Once everything is ready, it is time to prepare for assembly. This is also the time to spray paint or bed line for that clean professional look.
Each conduit box comes with a top cover that is screwed in place on each side. The top cover conveniently has a water tight gasket beneath it. The hard part is cutting out the center portion of the top cover to allow placement of the lexan lens. We completed this using a dremel tool and lots of patience. The goal is to leave just enough of a lip so the lexan lens can be siliconed in place.
Cutting the lexan to size is another challenge, but is easily accomplished with proper measurements and the dremel tool again. Once the lexan is cut, you can silicone it to the inside of your top cover.
Step 6: Final Assembly
This is where things get really exciting. It's time to put everything together! It is so simple, it takes just a few minutes. We placed our LED units into the freshly painted pods (ensuring all connections were oriented correctly). We then placed the star board lenses on top of our LED star boards and secured them by screwing on our lexan top cover. Next we placed our PVC tube spacers (which were measured and cut to ensure complete seating of the pods). Finally we plugged all of the JST connectors together and seated the bar fully together by twisting and pushing. It took us some finagling to make sure all of the pods were level and at the same angle.
At this point our light bar was completed and ready to mount. This was easily accomplished by using a $20 commercial light bar harness and simply adapting the bar to fit our specific Jeeps.
Step 7: Operation and Moving Forward
During the course of the last three years the bars have taken a beating and continue to work flawlessly. We have had several comments and interest in our bars, so why not share the knowledge. They are obviously different and provide a unique look compared to the commercial products. We dabbled in selling a few, but the commercial products are too plentiful and cheap for any real market. They do pack nicely to ship though ;)
I hope you have enjoyed this Instructable! I will answer any questions that I can and look forward to posting more projects in the near future!
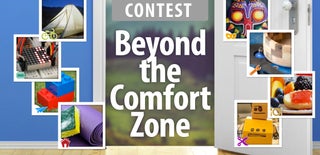
Third Prize in the
Beyond the Comfort Zone Contest
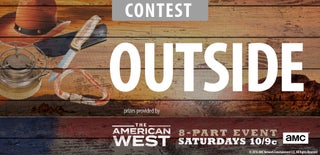
Participated in the
Outside Contest 2016