Introduction: Portable Suitcase Arcade
A little over a month ago a couple co-workers and I were talking about miniature arcade machines we had seen at Walmart, retailing for $250-$500. I figured it would be a fun project building a more powerful, portable arcade, while keeping it around that budget. It was a reason to build something to play with the 3.8-year-old girl at home, also thinking it would give me something to work on while watching our newborn that arrived November 11th.
Originally I thought I'd go with a Raspberry Pi due to space restrictions, but decided to use an old gaming PC that was collecting dust in the garage.
I wanted it to be portable, somewhat manageable in size, easy to upgrade, the ability to use deep classic-style arcade buttons and joysticks, room for high-quality speakers, a decent sized monitor, and HDMI out. Another bonus of the Seahorse case is that it's waterproof and supposedly crush resistant.
After seeing the quality and feel of cheaper Chinese button and joystick kits from Amazon, I decided to go for less of a budget build, instead using quality components from reputable manufacturers. There is no comparison price-wise, but the buttons and switches do feel more like an actual arcade cabinet, and should last for years.
This is my first Instructable, and I haven't written anything in a long time, hopefully the English works good.
Please vote vote for the portable arcade in the First Time Author contest at the bottom of the page if you like the project!
Supplies
1. A PC computer. Ideally with a low-form PSU, SSD's, and a PCI-e extension cable.
2. A case to hold everything, I used a Seahorse SE-920.
3. Monitor. 23'' Samsung TFT monitor from a thrift store.
4. Speakers. Pair of Klipsch shelf speakers found at a thrift store(Nice!)
5. Audio Amplifier. Kinter Tripath.
6. RGB controller/keyboard input. IPAC Ultimate I/O.
7. Arcade buttons. Industrius Lorenzo RGB buttons with Cherry switches.
8. Joysticks. Samducksa Quick-Release. They need to be detachable for the case to close.
9. 24 x 24'' sheet of 1/8th inch Lexan.
10. 12 x 24'' plate of 3/16th inch cold-rolled steel.
11. 2 x 4' sheet of 1/4 inch plywood.
12. Industrial-Strength Velcro tape.
13. Various machine screws, bolts and some corner brackets.
14. Vinyl wrap
15. HDMI splitter
16. 6 microswitches.
17. Power switch
18. Player buttons, two select/coin buttons, and four LEDs
Tools:
1. Tape measure/micrometer.
2. Screwdrivers/pliers
2. Circular saw/jigsaw.
3. Drill/drill Press.
4. Orbital sander.
5. Drill Bits, tapping bits, hole-saw bits.
6. Soldering iron/wire strippers
7. Razor knife
8. Tape
Step 1: Testing the Computer and Beginning to Layout Button Positions
I started out by disassembling the old tower and trying to clean everything as well as possible, leaving the aluminum plate and risers on the motherboard so it could be screwed to the plywood in the case. All the components were up on a table to see if everything still worked. It did!
I found several common button layouts through google, printed them, and taped them to a piece of cardboard to see which layouts were the most comfortable and best for the size of the control board. I went with a 7 button layout, the joysticks slightly closer to the buttons than standard, and both sets of buttons slightly canted toward where the player will be sitting.
While the Seahorse case was still in the mail I found a PDF with the schematics to the case, scaled it in Illustrator, and went to a local print shop to get a copy(Around $3.) I figured it would be an easy template that would be useful throughout the build. Unfortunately when the case arrived I discovered that almost all of the dimensions and screw locations were off by 1-3 millimeters in random directions.
Back to Illustrator I went, correcting them all after measuring the actual locations in the case with a micrometer. It was pretty tedious, but there isn't any tolerance for screw locations. I found a semi-local laser cutter who cut the steel plate for $20 + material, which I thought was a great deal.
Step 2: Layout the Base and Computer Components
I started this step cutting a piece of cardboard to place in the 'floor' of the case, setting the computer hardware inside to get a general idea of where everything needs to go.
After a lot of moving things around and deciding where it all would fit, I took the cardboard template and traced it onto some 1/4 plywood. Afterwards cutting it out with a circular saw and jigsaw.
Step 3: Mount the Speakers and Cut Holes for Power and Motherboard
For this step I drilled the appropriate size holes for the speakers, power supply, and motherboard inputs into another piece of 1/4 inch plywood.
After disassembling the speakers I decided to leave the driver attached to the plastic face-plate, keeping a gap between the soft rubber of the driver and the plywood, I used a jigsaw to cut the plastic to fit. After attaching the speakers, tweeters and control boards, I mounted it as flush as possible to the plywood in the base and sides of the case using corner brackets, using a tap to thread holes into the case.
Step 4: Tapping Control Panel Screw Holes, Attaching Plywood Base and Applying Vinyl
I originally intended to use Plexiglas along with the steel plate to create an infinity mirror effect, which I still think would have been really cool. Unfortunately the Plexiglas ended up being literally a millimeter too tall for the case to close easily.
Next I took an M40 drill tap and threaded the mounting holes in the base and lid of the Seahorse case, and also the steel plate. Using threaded machine screws will make it easier to work on without damaging the thin screw holes. Afterwards I used the steel plate as a template to trace a 1/4 inch plywood base the for Ultimate I/O board to attach to.
I used a drill press to drill all of the button holes, then sanded it all down with an orbital sander. I also sanded the steel plate to somewhat round the edges, making it slide into the case more easily.
I used rubbing alcohol, a lot of heat with a hairdryer, and a credit card to apply the vinyl, which turned out surprisingly well.
Step 5: Installing the Monitor
The monitor I found is a Samsung Syncmaster p2350, it has a nice picture and viewing angle for a TFT monitor, ideally it should have the output and power cable facing down, so no special cables or mods are needed to feed the cables through the bottom of the Lexan.
The first step was stripping the plastic case off of the monitor with a small flat-head screwdriver. 10 minutes later, a broken connector for the monitor buttons, and I was done. I ended up soldering the wires back to the monitor control board. One great thing about this monitor is that the buttons are touch sensitive, they work through the Lexan and could just be glued to the base of the screen.
After making sure the monitor and control buttons worked, I cut some pieces of scrap wood into braces(for lack of a better word) to attach to the back of the monitor, leveling and lifting it off of the lid of the case. To secure the monitor I used 'industrial' strength Velcro, leaving the monitor about a millimeter above the case edge so the Lexan would sandwich it into the case.
I began tracing the case lid template onto the Lexan, cutting it out using a jigsaw slightly larger than needed, and then smoothed the edges using an orbital sander with a fine grit sandpaper. It popped right in! Afterwards I cut out a 2 x 3cm rectangle at the bottom of the screen to feed the cables through.
I marked the holes on the Lexan using a sharpie, then drilled and tapped them.
Step 6: Wiring the Control Panel
Once the panel had the vinyl applied it finally felt like I was getting somewhere, the buttons can be installed!
I began screwing on the buttons, all angled toward the center of the panel.Then using some Velcro tape to attach the Ultimate I/O controller to the plywood, afterwards I began connecting all of the RGB, power and ground wires. I made sure to wire them in order so programming them is easier.
Soon I realized I hadn't ordered buttons for Player 1, 2, two coin buttons, and was short 2 micro switches. I picked up some cheap buttons and switches on amazon. The two player buttons didn't work at all, and one of the LED's on one of the coin buttons was broken. They also have poor action and feel cheap. There are more Industrius Lorenzo buttons in the on the way.
The switches on the other hand were really nice, I'm not sure what weight they are, but they feel about twice as hard to depress as the 75 gram Cherry switches, so maybe 150 grams. These worked great for button 7(the thumb button) on both sides of the panel, the extra weight allows you to rest your thumb on the button without accidentally depressing it.
Step 7: Finishing Wiring and Wrapping It Up
Now it's time to clean up the wiring, test the LED's, and do some finishing touches.
All the buttons were a breeze to get working correctly, aside from the ones from amazon. They also look great, I'm not sure if the pictures do justice. Actually programming the software to light the buttons on a per-game basis is a bit difficult and would take several pages to explain.
The Kinter amp was mounted in the opening where all of the power and PC wires lay, for easy access to the volume and tone controls. There's still enough room for a miniature wireless keyboard, the 12 foot power cord, an HDMI cable, the joystick tops, and possibly a game controller or two.
Finally, installing a power button for the PC, cutting some joystick dust covers out of some mirrored Plexiglas(the ones that came with the Crown joysticks were a bit too small) and installing a high-power 50mm fan between the speaker controllers to vent the heat.
Step 8: Finished..basically *Updated*
*Update with photos- the new buttons arrived, I wired them up, popped them in, and everything's working great! They feel a lot nicer and look better too in my opinion! Thanks for reading everyone!
Pretty much everything is wired and working correctly, aside from the four buttons at the top, which I am switching out for Industrius Lorenzo buttons and LED's, they'll be here in a day or two. I'll update the Instructable once the new buttons are installed.
Unfortunately, a week or two after mounting the monitor into the case it got a single row of dead pixels toward the right side, which was upsetting because the size and controls were perfect. I took it back out and checked the connections to the monitor board and cables, but no luck. On the bright side the Velcro makes it easy to replace, which will probably happen next time I come across the right size monitor in the 10-20 dollar range.
The speakers are LOUD, like boombox loud. This little Tri-Path amp rocks. The enclosure makes an excellent speaker box, the amount of bass it produces while playing games feels almost like vibration-feedback on a controller.
Setting up the software alone could be another ten pages of writing, I used BigBox for the arcade front-end, which boots when the computer starts. It gives a nice arcade look, and no mouse or keyboard are needed to navigate the menus.
Thanks for reading. I should have taken better pictures throughout the process, but didn't think they would be uploaded anywhere. Hopefully it can help people doing a similar project.
Being my first instructable I probably have forgotten a few things or not explained clearly enough. Feel free to ask any questions. I also entered in the First Instructable Contest, please give me a vote below if you like the project.
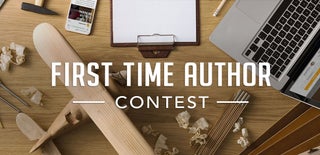
Participated in the
First Time Author Contest