Introduction: DIY Professional Furniture for Amateurs
We live in a world where buying products and goods couldn't be easier and yet we are also surrounded by endless resources to complete projects and make things ourselves. As a middle school technology, engineering, and design teacher and avid maker/tinkerer, I enjoy and encourage the value in creating one of a kind DIY products while learning new skills and abilities.
Recently, I moved into a new home and found myself in the position of needing some new furniture. Now of course I could have bought some new or used things from countless sources, but I wanted custom furniture that fit my needs and constraints. This would have costed me a small fortune to order.
Now I am not a woodworking novice but would not I call myself a professional either. However, I set out to make some HGTV quality furniture in an amateurs maker space with some basic tools and a tight budget. Through this Instructable, I will guide you through the same process.
Step 1: Planning for Success
Before setting out to build your furniture, or any project for that matter, planning is key for success. As I said, I am far from an expert so I found myself browsing the internet for plans and project ideas. Instructables of course is filled with great tutorials and project ideas, as is Anna White's website in regards to furniture plans.
I also looked at some of the old, cheap, and falling apart furniture that I was replacing to get a sense of size and needs. For example, my old TV stand that I wanted to replace couldn't fit my server, stereo, and speakers in a concealed way and that was something I wanted to accomplish with my new piece.
It also helps to create your own sketches and cut list even if you find plans online. I found some plans for inspiration but I made my own modifications based on my budget and desires. By making your own cut list, or even some basic CAD renderings in something like Tinkercad, Fusion360, Sketchup, or OnShape, you get a better grasp of what materials you will needed which will set you up for more success (and savings).
Step 2: Tools and Materials
There is not one way to complete any project. To make furniture in the best possible way, you would want to have access to an industrial materials processing lab with extensive machinery and resources. Now as that isn't an option for many of us, I wanted to share the minimum requirements, as well as some intermediate resources that would make the process easier.
Basic Tool Necessities:
When buying your tools, you have many brands to sort through. Some great entry-level brands are Ryobi, Black and Decker, Porter Cable, and Skill. Some higher quality and more durable brands are Dewalt, Bosch, Milwaukee, and Festool. Choose your tools based on you budget, and the demand (amount of times you need to use it).
- Safety Glasses
- Tape Measure
- Level
- Carpenter Square
- T-Square
- Basic Bar Clamps
- Hand Drill
- Drill Bit Drivers
- Drill Bit Index
- Spade Bits
- Circular Saw
- Jig Saw
- Palm Sander
- Kreg Jig
- 18 gauge Brad Nailer (and compressor)
Intermediate Tools:
The following tools are not necessarily needed, but would make completing a large-scale project much easier.
- Miter Saw
- Table Saw
- Scroll Saw
- Router
- Router Table
- Router Bits
- Drill Press
- Shop Vacuum
- Large Bar/Pipe Clamps
- Forsner Bits
- Countersinking bits
- Plug Cutters
- Hole Saws
Professional Equipment:
These are tools that a professional may use to streamline the process even more.
Materials:
Selecting your materials depends on your project, budget, and resources. If you do not have access to surface planers or jointers like me, then you are going to want to purchase wood that is pre-cut rather than rough finished. Buying select Pine boards from Home Depot will cost more than buying rough-cut hardwoods from a lumber superstore, but its more accessible to most and cuts a lot of the initial work out that needs some heavier machinery.
I built this set of furniture out of an assortment of select pine from Home Depot, 1/2" birch plywood, and some of Home Depot's pre-laminated pine project panels for the tops. This is not how a pro would do it, but it was the best option for me based on my resources, budget, time, and other constraints.
In addition to wood, you will need screws, nails, glue, stain, paint, and other things needed for assembly and finishing (discussed in later steps).
Step 3: Processing, Cutting, and Ripping
Once you have your plans, your tools, and your materials, its time to start to build! This is where the age-old saying "measure twice, cut once" comes to play. Follow your plans, but check your measurements as you work. I have made furniture two different ways, each with their own set of pros and cons:
- The first is to make your cuts as you assemble. The pro is that it will be immediately apparent if something doesn't line up or fit and you can make adjustments as you go. The con is that this is a very slow process, and making adjustments as you work tends to take you away from your original plans which could be catastrophic.
- The second is to make all your cuts, then assemble with minor tweaks and adjustments. The pro is that this is a more organized and quicker way to work. The con is that if something is off, you may discover that after you've run through all your materials. This method works very well if you have put a lot of time into your planning, which typically takes practice.
As you work, remember safety. All of the tools I listed in the previous step are dangerous and can cause serious harm or injury. Reading the manual isn't quite enough if its your first experience. Browse youtube and instructables for tutorials and make sure you feel comfortable using the tool while remaining aware of the danger. Always wear safety glasses and ear protection and never work completely alone. Make sure someone knows where you are and that you are working with machinery so they will check in.
Step 4: Joinery and Assembly
Once you have your material cut down, it is time to assemble through joinery.
"Joinery is a part of woodworking that involves joining together pieces of timber or lumber, to produce more complex items. Some wood joints employ fasteners, bindings, or adhesives, while others use only wood elements"
Professionals create cuts and grooves that allow for wood to fit seamlessly together using nothing but some wood glue. Amateurs can rejoice to know that there are plenty of methods to fasten your boards together cleanly and with ease.
A popular tool is the Kreg Jig, one that creates pocket holes to fasten wood together using concealed and hidden screws. The Kreg Jig is easier, efficient, and cheap but made even stronger when combined with wood glue. I used pocket holes to assemble panels, drawers, shelves, and even attach the tops on my furniture.
Another great tool is the 18 gauge brad nailer. This is phenomenal for attaching trim, especially when you plan to paint the furniture which will conceal the nail holes. The brad nailer should not be used for structural demands, but can be strengthen when combined with glue.
Putting glue on two pieces of wood and clamping them together works as well, but can often be difficult to keep flat or aligned. I suggest you combine glue with the Kreg screws or brad nails for the best result.
Step 5: Finishing
A mentor of mine once told me that "finishing is the easiest and fastest way to ruin a project". He said this because people often feel as though the project is over and rush through it which can take beautiful craftsmanship and make it look like garbage. Now theoretically you can almost always sand down your finish to take the project back to wood, but you may lose detail or quality and definitely lose time.
Before finishing, test fit all of your parts, shelves, tops, and drawers before beginning the finishing process. Now is the time to make adjustments if needed. As you test fit, and before you start to paint or stain, sanding is an incredibly important step. Sanding wood removes imperfections and defects, as well as allows your finish to stick while keeping your project smooth. Some sanding must be done by hand but other parts can be done using an electric palm sander for consistency and to save time. You should start with a low grit (80 or 100) and work your way up to a higher grit (220 or 300) before applying your finish.
Choosing whether to paint or stain your stain your project usually falls to personal preference, but there can be a few factors that may make your decision easier.
- If it is a beautiful piece of wood, or an expensive hardwood, it would be a shame to paint over it. Consider a light oil or clear varnish instead.
- If you are blending plywood with hardwoods or multiple types of wood, it may be difficult to apply an even and matching coat of stain across your project. Pre-stain conditioner can help alleviate this problem but it some cases painting may be a more professional finish
- If your project has gaps, cracks, holes, or other imperfections you want to cover up, use caulk or spackle to fill and then paint your project instead of stain.
- Projects that are a combination of painted and stained is a timeless look and may be a good option if you combined budget saving manufacturing methods.
Now when actually applying your finish (paint, stain, oil, varnish, or whatever it may be) there are many methods and sciences to follow. People far more skilled than me have documented these methods on the internet and I suggest you flip through. From what I can tell, there is never one way to do it and when I personally try to get fancy or follow a scientific procedure I always end up spending lots of money and making a mess of it. See my simple, trusted, and true methods that I use below which haven't let me down yet.
- Don't cut corners with the sanding, you will notice
- Always apply finish in a well lit, ventilated, clean, dry, and warm environment
- Never shake your cans of finish, always stir gently
- Always clean your projects with tac cloths before and in-between each coat of finish
- Use a light-weight spackle to fill cracks, apply with your finger and then lightly sand over once dry
- Apply paint with a spray gun for the best finish, or use high-density rollers to mimic a spray gun
- Apply stain with white cotton rags evenly, wear nitrile gloves
- Use polyurethane for clear coats and either apply using a spray gun or a nice (not cheap) brush, clean your brush thoroughly after each coat and throw away after each project
- Use purple scotchbrite pads to sand after each coat of polyurethane dries, then wipe with a tac cloth before applying the next coat
- apply at least 5 coats of polyurethane every time
- Wax paint using a cotton rag and finishing wax to smooth and protect
- Wax finished wood using steel wool and finishing wax to smooth and protect
Step 6: Unlimited Possibilities
I hope that this instructable has answered some questions you may have had, or just gave you that extra bit of inspiration needed to start your next project. There are countless and endless possibilities when making DIY projects and I hope you are as excited about that as I am.
I appreciate your support and feedback, as well as you sharing your own projects for me to get inspiration from. Be safe and happy making!
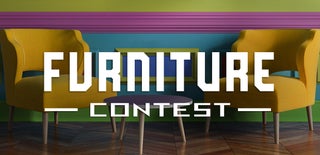
Participated in the
Furniture Contest 2018