Introduction: DIY TMS, RTMS, Transcranial Magnetic Stimulator, 15 Pulses Per Second, for Treating Depression and Addiction, Monophasic
A simple monophasic repetitive Transcranial Magnetic Stimulator (rTMS) unit is shown here, built from relatively cheap materials, with an emphasis on high voltage safety.
CAUTION:
- rTMS PERMANANTLY CHANGES THE BRAIN, USE ONLY AS A LAST RESORT
- OPERATORS SHALL BE CPR CERTIFIED: SIEZURES HAVE BEEN REPORTED
- DO NOT APPLY rTMS WHERE METAL PLATES WERE EMBEDDED IN THE SKULL
- DO NOT APPLY rTMS TO PEOPLE WITH EPILEPSY
- TMS RELEASES DOPAMINE, MAKING rTMS POTENTIALLY ADDICTIVE
rTMS may be effective in treating depression, addiction, PTSD, etc. Many sufferers can't get help from existing institutions. My aim was to develop an rTMS design for the Maker Space. Hopefully makers can treat sufferers close to them.
rTMS was first approved by the FDA in 2009, for treating "untreatable" depression. More recently the National Institutes of Health (NIH) conducted a study, hoping to help people suffering from Cocaine Use Disorder (CocUD), using the same protocols. Pulse width is 100 microseconds. Pulse repetition rate is 15 Pulses Per Second. Pulse trains are 4 seconds long. Rest period is 15 seconds, between pulse trains. This system meets these specifications. Clinical units can deliver up to 750 Joules. This design is relatively underpowered by comparison. It only delivers 45 Joules of energy. Not to be scoffed at, this design is well liked by addicts.
This design isn't likely to exceed Muscle Twitch Threshold (the peak energy selected for many therapies, including the the NIH study on CocUD sufferers). No attempt is made to adjust pulse energy. Field strength can be adjusted downward, by retracting the applicator coil away from the patient, inside the unit. This adjustment is made using a Philips screwdriver.
45 Joules may sound small. Don't be fooled by that. Radiated peak power is 2.7 Megawatts.
Supplies
A Field Service technician's case was chosen for a cabinet. An 1/8" thick aluminum baseplate was cut to fit inside. High power components are mounted to this. We mount the baseplate to angle brackets. These are affixed to the case with 1/4" inch Pop Rivets. Each angle bracket is fitted with Riv-Nuts (8-32 threaded inserts), so the baseplate can be screwed down.
A small "Boxer" fan was installed in the bottom of the case. Airflow enters here, through a perforated stainless steel grille. Fan and grille mounting screws are secured by Nyloc nuts.
Another perforated stainless steel plate was cut to form a front panel. This is mounted behind the telescopic handle, using 4-40 screws and nylon lock nuts. Cabinet airflow exits here.
Pushing the retractable handle into the home position forces a power switch OFF, thus functioning like an Emergency OFF Button. The fully retracted handle protects front panel controls from impact in shipment.
Attachments
Step 1: Power Control Timer Board Fabrication
Construct board as shown.
Our desired protocol requires a four-second pulse-train, followed by fifteen seconds OFF time, then repeating. A 555 Timer IC serves this function. An off-board 12 Volt supply powers this timer and an applicator-coil cooling fan. The low-going 555 timer output drives an off-board 50 Amp Triac, which applies primary power to the high-voltage (HV) transformer.
The fan motor generates a 12 Volt square-wave tachometer signal. This signal enters the Timer Board, and is required for high voltage activation. Fan failure detection prevents applicator coil overheating.
12 Volt fan power and the Triac-controlled HV section are energized by the power switch. The first four-second pulse train appears about twenty-five seconds later, repeating every nineteen seconds.
A red LED indicates 555-Timer Output=LOW=HV ON. With the fan's tachometer signal present, a yellow LED indicates the HV ON drive signal will activate the offboard Triac.
A 100 Ohm Triac Gate resistor is mounted above the board because it runs warm. Insulated wires enter the board through holes. Wires are stripped and tinned near where they attach. This provides strain relief.
Timer Board Testing is covered in the Test Data Sheet. The fan, the 12 Volt power supply, and the timer board, shall be tested together. An incandescent light bulb can be substituted for the High Voltage Transformer in the test phase. Testing should be completed before final mounting is done.
Step 2: Pulse Driver Board Fabrication
Install components as shown.
Ideally each SCR should be laid flat, and screwed down to the board using 4-40 hardware.
Insulated wires enter the board through holes. Wires are stripped and tinned near where they attach. This provides strain relief.
This board mounts on standoffs. An inductor assembly stacks on top of it. Full testing shall be completed before the Pulse Driver Board is installed (see the test data sheet).
Step 3: Switch Deck Assembly
Holes are drilled and tapped into the heatsink to mount boards and devices.
Two tapped holes mount the dual SCR module (8-32).
Five tapped holes mount two circuit boards (6-32, 5 places).
A third Snubber Board mounts between the two end boards.
Small angle brackets were helpful for anchoring the three boards together. My board layout made it difficult to isolate all high voltage electrical connections from each other and ground by at least 3/8" inch.
Two through holes are drilled for mounting the heatsink to the baseplate (#10 stud size). I attached #10 studs to the baseplate. These projected up through the holes in the heatsink. Nuts were placed immediately below the heatsink. Nyloc nuts and flat washers secure the assembly from above.
Three number-#4 through-holes accommodate mounting the TO-247 diode packages to the heatsink. Aluminum Oxide insulators are placed under the TO-247 diode packages. Nyloc nuts secure the screws.
Heatsink Grease is used under the SCR module, and under the TO-247 diode packages.
High voltage resistors are covered with heat-shrink tubing, and anchored to boards using Ty-Wraps. (In past systems, vibration broke high voltage resistor leads in transit.)
.02 uF snubbing capacitors are affixed to snubbing resistors with hot glue. This is also done to avoid vibration-induced lead breakage.
Teflon Gate Drive windings on the pulse transformer are double insulated, using fiberglass/silicone sleeving. This is done to avoid corona.
The neon indicator I used looks nice, but mounting it was a hassle: these have stainless steel mounting tabs. Soldering them won't work. Nor does drilling: the metal is too springy. I had to punch holes into them, sized for 2-56 mounting screws. Any other standard neon bulb would work (NE2 is suggested).
This assembly is overly complicated. Semiconductors used here don't dissipate much heat. The whole design could be constructed on a flat circuit board, with heavy copper lands placed under the diodes and SCRs, to spread the heat. Pulse current carrying conductors should remain #14 AWG wires (or equivalent).
Attachments
Step 4: Construct Ringback Inductor Assembly
We need one primary winding from a microwave oven high voltage transformer. (Two windings went into this assembly, but only one was used.) Microwave oven high voltage transformer cores come welded together. The welds don't penetrate very far into the core material. Using a hacksaw or bandsaw, we cut into the welds, down to about 1/4" inch depth, right along each seam. Then the I-Core section can be separated from the E-Core section.
Primary windings come glued into transformer cores. Winding removal is eased by first knocking out inductive shunts, located between the primary and secondary windings. A pin punch assists in doing this (see photo). Tapping with a rubber Malott can break the primary winding free. Prying force is then gently applied between the heater and high voltage secondary windings, to lift both the heater and primary windings gently off the core. This helps avoid scuffing primary-winding insulation. Primary windings are often made of soft aluminum magnet wire. Care should be taken in the removal process, not to dent or gouge the winding. Separate the heater winding and discard it.
This inductor runs warm, so it should be placed in the path of minor forced-air circulation. In this case, it's near the inlet of the Applicator Coil Fan.
The inductor is subjected to high AC voltage, so it shall be mounted in an electrically insulated assembly. G-10 Fiberglass mounting plates were fabricated for this purpose. Mounting plates should be at least 1/8" thick. A 1/4" inch thick G-10 Fiberglass baseplate was used here.
Nuts and 6-32 stainless steel threaded rods pull these mounting plates together, thus clamping Inductor windings in place. Dual lock-nuts are cinched together at one end of each 6-32 threaded rod. This forms a long hex-head screw. A Nyloc nut secures the other end of each threaded rod. Bellville washers are inserted into the washer stack, to maintain uniform compression, allowing for minor thermal expansion of the windings. (Nyloc nuts aren't cinched down completely.)
Large holes were drilled into the G-10 mounting plates, alongside the windings. Two-Ton Epoxy (from Tap Plastics) was poured into the holes, along the windings, thus affixing them to the mounting plates.
(Something similar could be done to mount a single primary winding, clamped between two G-10 plates, surrounded by 6-32 threaded rods.)
Step 5: Stack Inductor Assembly Atop Pulse Driver Board
Test the Pulse Driver Board and Switch Deck (together with the Pulse Repetition Rate selector switch), per the test datasheet, prior to final mounting.
Step 6: Fabricate Snubber Assembly
We electrically isolate resistor and capacitor mounting hardware by anchoring these parts to an 1/8" inch thick G-10 fiberglass backboard. These resistors are only rated for 1 KV AC, with respect to their mounting brackets. Metal mounting plates run down the center of each, making them less than ideal for high voltage applications. By floating the mounts, we shouldn't exceed the peak rated voltage. Inductance isn't an issue, so any other wirewound resistor would work just as well (10 Ohms, 50-100 Watts). These two microwave oven capacitors were selected for having matched capacitance values (but nearly-matched capacitor values should be fine). By floating the capacitor cases, we run them at about half their nominal AC operating voltage. This is appropriate because we subject them to faster risetimes than would normally be encountered.
Step 7: Fabricate the Capacitor Bank
As a general rule, we shall use nylon-insert lock nuts (Nyloc) wherever we attach anything to plastic. Plastic can deform over time. This tendency is called "cold flow." Our concern here is when a pinched spot gets thinner over time. It might be okay for hardware's grip to loosen somewhat. It's definitely not okay for hardware to loosen up, fall off, and rattle around inside the cabinet. Nylock nuts won't fall off if things loosen up. Medium Strength Loctite is used where screws attach assemblies held down by standoffs.
Brutal pulse current requires us to use two #14 Gauge wires, run in parallel, to each capacitor terminal. Sixteen Gauge wire would survive. But the Slip lugs tend to fail. (They loosen up after repeated disconnections.) Slip-lugs can be squeezed with pliers, to get them to mate again tightly. Despite this effort, pitting appeared under lose slip-lug connections. Putting two lines in parallel should eliminate this tendency. Always tug-test crimps, and slip lug grip strength.
We want our bleeder board connected directly to the capacitor terminals. Resistors shall remain connected at all times, even when the pulse lines are disconnected. (This is good high-voltage practice in all energy storage capacitor applications.)
Capacitor clamps are anchored to a 3/8" inch thick Polycarbonate mounting plate using custom-cut angle brackets. (Custom capacitor clamps could be fabricated from sheet metal, with mounting tabs oriented downward, for direct attachment to the Polycarbonate mounting plate.)
2.2 megaohm high voltage resistors are covered with heat-shrink tubing, and anchored to the bleeder board using Ty-Wraps. Neon bulb tips are anchored to the bleeder board with little loops of bare copper wire, which are pulled tight, then soldered together behind the board. Proper component anchoring prevents lead breakage, due to vibration in transit.
We're using 34 uF 660 VAC Motor Run Capacitors. Manufacturers often label such capacitors: 1,500 VDC, in addition to the 660 VAC rating. 2,700 volts peak appears in this application, distributed across two capacitors in series. We're applying 1,350 Volts Peak to each 1,500 Volt DC capacitor. But there is an AC component, which exceeds each capacitor's AC RMS Voltage rating. Peak currents of up to 1,400 amps are delivered, requiring foil-film construction. Capacitor survival requires us to isolate the capacitor cases, and let them float. (This is how we avoid applying 2,700 volts peak to the terminals of a grounded 1,500 volt DC capacitor.)
2.2 Megaohm high voltage bleeder resistors are placed directly across each capacitor. An additional 2.2 Megaohm resistor is placed across each capacitor, powering a Green Neon Bulb. These can indicate correct voltage balance in operation, or residual voltage, after primary power removal. If a capacitor was shorted, the corresponding neon bulb would fail to glow. Green neon bulbs aren't necessary: any regular neon bulb would work (like the orange NE2).
As a general rule, we want our cap bank substantially discharged within a few seconds after primary power removal. That presents a tough engineering challenge here. Required bleeders would be large. They would get hot. Lost power would detract from system performance. Instead we dissipate capacitor energy promptly by keeping the switching section active between pulse trains. This does not, however, discharge the capacitor bank quickly when primary power is interrupted.
Multiple neon bulbs exist in this system. Each may show lingering high voltage. This cannot be relied on, when servicing is attempted. Indicators can fail. So whenever we service the unit, we should turn the pulse off first. Disconnect the primary power a short time afterwards. This allows ongoing switching action to discharge the cap bank. Whenever the electronics are exposed for service, we should manually discharge high voltage points with a shorting stick.
Always practice good high voltage safety:
- Get CPR Certification for your whole team
- Install a shorting stick
- Install an overhead pull-cord, poised to disconnect primary power from all workstations, in the event of an emergency
- Keep a telephone (landline) active nearby
- Never work on energized circuitry alone
- Wear safety glasses
- Stand on an insulating surface, or wear dry rubber shoes
- Whenever testing energized circuitry, keep one hand in your pocket at all times
- Any arm-to-arm AC shock should be followed by a 24 hour observation period, spent in a Coronary Care Unit (at your local hospital)
- If someone gets shocked or appears injured, activate the Emergency Medical System immediately, by calling 911
- Whenever working around dangerous voltages: make yourself comfortable
Step 8: Fabricate Applicator Coil
A mandrel is constructed from Polyethylene round stock. The area for coil-winding is tapered slightly, to ease coil ejection. Snout diameter is 1.37" inches at the tip, 1.4" inches at the side-wall. First winding width is .85" inches.
Three Socket Head Cap Screws are installed to eject the finished coil. These don't impinge directly on the coil. Instead they drive 5/16" inch diameter dowel pins forward, toward the coil. 3/8" inch diameter rubber bumpers are placed in front of each dowel pin, to gently eject the coil. So we begin each ejector-screw hole with a tap-drill for 1/4-20 thread size (#7 or 13/64").
On the coil side, we first counterbore a 5/16" diameter passage, but only deep enough to accommodate the fully-retracted dowel pins. Then we counterbore the face that mates with the coil, 1/8" inch deep, 3/8" inch diameter, to retain the rubber bumpers. (I wished afterward that I made my 3/8" counterbores an interference fit, to retain the rubber bumpers. Plasticine was needed to hold my rubber bumpers in place.) At the other end of each ejector-screw hole, we drill a 3/8" counterbore, but only deep enough to accommodate the heads of the Socket Head Cap Screws. We tap what remains with a 1/4-20 tap.
The winding is constructed from #12 AWG HAPTZ wire. (Ordinary Magnet wire will work just fine.) A through hole is installed in the mandrel, the size of the wire, to hold the "start" lead, prior to the beginning of the build. The "start" wire is left 4" inches long, extending into the headstock of the lathe. Plasticine putty is plugged around the wire within this hole, to keep Epoxy out during the winding process. The wire gets stuffed into the hole, and kinked over at a 90 degree angle, in preparation for starting the winding process. A large clip is mounted to the tool rest of the lathe, which has rubber grippers, to hold the wire taught between operations. Clamp the wire there temporarily.
Thin strips of G-10 Fiberglass (~10 Mills Thick) are cut, sized to be inserted under each layer of the winding. The first layer, placed directly on the mandrel, will be .85" inches wide, 4.4" inches long. The rest of the G-10 fiberglass strips get sanded rough on both sides, to enhance Epoxy adhesion. But the first strip of G-10 Fiberglass isn't sanded rough. We will remove this inner-most layer, after the Epoxy sets.
Guide caps are needed to hold each winding layer in place, especially as the winding reaches the edge of the mandrel. My guide caps were cut from the "dome side" of NordicWare Dual Egg Poachers, using hole saws. The smallest guide cap is mounted to the mandrel first, before the first winding gets laid down. It measures 1.54" inches in diameter. The next layer guide-cap measures 1.8" inches in diameter. The largest guide cap measures 2.3" inches in diameter.
The first un-sanded layer of G-10, gets pulled tight around the mandrel initially, using a small strip of masking tape, which is placed toward the outer edge, for easy removal (after a few turns of wire are laid down).
A foot pedal switch assists in controlling the lathe motor. The Back Gear on the lathe is engaged, for slow speed operation. A turns-counter is constructed using an Omron brand "event counter," attached to a Reed Switch with an integral magnet. A steel vane is attached to the lathe chuck, which interrupts the magnetic circuit on the Reed Switch assembly, once per revolution.
Whenever the winding process is stopped, the lead-wire gets anchored by the rubberized clip mounted on the tool post.
In preparation for winding our first layer, Tap Plastics Two-Ton Epoxy shall be mixed. The first few turns of wire are laid down without glue. (This holds down the underlying G-10 Fiberglass strip.) The winding process is stopped momentarily. Masking tape is removed from the G-10 fiberglass strip. We begin the winding process again, with the wire constantly pulled taught by hand. We begin covering the winding with Epoxy, using the other hand. With the first layer complete, the wire is anchored to the clip on the tool post. The retainer cap gets removed from the end of the mandrel, and replaced by a slightly larger one. Wet Epoxy is wiped off each retainer cap immediately after use, using alcohol.
A strip of sanded G-10 Fiberglass is laid down over the first layer. Fresh Epoxy is mixed. We begin to lay down our second layer.
This process repeats until all four layers are built, separated by sanded G-10 strips, with 35 turns indicated on the counter. The "finish" lead is secured by the rubberized clip mounted on the tool post. Epoxy is given time to cure. The winding is ejected. The center G-10 strip is peeled out.
Step 9: Mount the Applicator Coil
Fabricate an 1/8"-thick G-10 Fiberglass mounting plate as shown. 8-32 Riv-Nuts are inserted to attach the lead wires. (Harbor Freight sells cheap Riv-Nut kits.) Small holes are drilled into fiberglass edges that face the Applicator Coil (for good anchoring). Sand is mixed with Two-Ton Epoxy. (Epoxy doesn't make a good structural material without added ceramic fill.) Sandy Epoxy gets applied between the applicator Coil and the Coil Mounting Plate, also filling the small holes. After the Epoxy cures, Applicator Coil wires are cut to length, stripped, and soldered into #8 non-insulated ring lugs. These are screwed down to the Riv-Nuts.
Step 10: Construct Applicator Coil Assembly
A piece of 2" Inch PVC Pipe is cut to length. It gets slotted lengthwise to accommodate the Coil Mounting Plate. Slotted it with a hack saw first. Then I used three hacksaw blades, screwed together at each end, for a handheld cutter, which I used to widen the slot. Small angle brackets are used to attach the fan to the end of the pipe, and for attaching the mounting plate in four places.
(I used angle brackets that came with 6-32 threaded holes on one face. Each gets attached at the other face with a pop rivet. Anything similar should work just as well.)
Large custom angle brackets were fabricated for mounting the Applicator Coil Assembly to the baseplate. These clamp the Coil Mounting Plate from both sides. Both get screwed down to the Baseplate.
This fan draws 1.2 Amps at 12 Volts. I had one with superior airflow, which I liked better. It drew 1.4 Amps. Alas it failed occassionally, for no apparent reason. Replacements of the same brand did the same thing. This fan is subjected to high pulsed magnetic fields. You might not be able to find the fan I specify in my parts list. Anything similar might work. But hand selection may be necessary, if you have trouble finding one with a reliable motor. Fan-motor failure interrupts system operation, so a fan-failure shouldn't prove catastrophic.
Notice how the base-plate has slotted holes, to allow for coil retraction, away from a user's brain. This offers our only adjustment of field strength.
Black angle brackets shown here were cut from Server mounting rails. These came with 12-24 tapped holes, which I aligned with slotted holes in the baseplate. Mating screws seem to have an interference fit, which feels nice. Screw heads are accessible to end users on the top side of the baseplate.
Step 11: Cabinet Wiring
Wire the control panel first. Attach fan wiring to the case with cable clamps. Keep all wiring tied safely away from the main assembly. Pulsed high voltage, and high voltage AC, tend to break down insulation over time. The best way to avoid this is to provide air spacing between high voltage points and low voltage wiring. Use spiral wrap or Ty-Wraps to bundle the umbilical cable to the Main Assembly. Route the umbilical using cable clamps to avoid interference with Main Assembly components. Use Nyloc nuts to affix the front panel to the plastic case.
Step 12: Final Assembly and Wiring
Mount the 12 Volt fan power supply to the baseplate. (It sits underneath the capacitor bank.) Sheet metal mounting straps shall be cut and folded, sized to hold the 12 Volt power supply down. Rubber pads shall be inserted under the mounting straps, to grip the power supply firmly without crushing the plastic enclosure.
Mount terminal block (TB2), Triac (TR1), and Power Control Timer Board (A3). Lay in associated wiring. Use Ty-Wraps to secure the wiring.
Install a 6.3 volt incandescent lamp on the high voltage transformer. A hole in the transformer core can be tapped with 6-32 threads. Mount the bulb there using a cable clamp. Solder the 3 volt Magnatron heater winding leads to the base of the 6.3 volt bulb. The bulb will glow dimly whenever the transformer is energized.
Four wooden spacers are fabricated, sized to elevate the cap bank, making space for the 2 Amp 12 Volt Power Supply underneath.
Mount the Capacitor Bank above Power Supply PS1. Nyloc nuts are used to hold the cap bank down. Mount the Switch Deck (A2), Snubber Assembly (A5), HV Transformer (T1), Applicator Coil Assembly (A4), and the Pulse Driver Board (A1) / Inductor (L1) assembly. Attach the cabinet assembly harness. Mate all connectors.
Consult the System Harness drawing (1030-WD) for wire gauges and routing details. Keep high voltage wires short and direct. All high voltage lines shall be isolated with air spacing.
Print the System Harness drawing. Verify each wire was correctly placed. Tug-test all crimp lugs. Check each wire off on the wiring diagram with a check mark, as this process is done. Sometimes it is helpful to have a second person, who also verifies each lead was correctly placed, and that each lug was correctly crimped. Do not proceed until all crimp-lugs and wiring placement is confirmed.
Attachments
Step 13: System Turn on / Testing
Always practice good high voltage safety:
- Get CPR Certification for your whole team
- Install a shorting stick
- Install an overhead pull-cord, poised to disconnect primary power from all workstations, in the event of an emergency
- Keep a telephone (landline) active nearby
- Never work on energized circuitry alone
- Wear safety glasses
- Stand on an insulating surface, or wear dry rubber shoes
- Whenever testing energized circuitry, keep one hand in your pocket at all times
- Any arm-to-arm AC shock should be followed by a 24 hour observation period, spent in a Coronary Care Unit (at your local hospital)
- If someone gets shocked or appears injured, activate the Emergency Medical System immediately, by calling 911
- Whenever working around dangerous voltages: make yourself comfortable
Fabricate a shorting stick with an insulating handle, attached to the grounded baseplate by a heavy lead-wire. Apply Ty-Wraps, both at the handle and at the baseplate, to prevent wire ends from flexing. This shorting stick shall be used to discharge capacitors, and to short anything in the system before you touch it.
I've turned these systems on with a variety of wiring errors. Luckily, nothing bad ever happened. I was always able to deduce what I did wrong, from the symptoms I saw. At each step shown below, verify the system behaves as described. If not, diagnose and fix each subsystem before proceeding. Refer to System Schematic (1031-SD) as needed.
An advanced test lab is always desirable. If one is available, testing should be done using the Test Data Sheet. But for makers in the field, fancy test equipment won't be available. Given only primitive operating conditions, the following turn on sequence should prove sufficient:
Leave the unit unplugged. Set the power switch in the OFF position.
Pulse Driver Board Testing:
Disconnect one AC input lead from High Voltage Transformer (T1). Insulate this disconnected lead.
Disconnect the cabinet fan connector.
Plug in the power cord.
A green LED on the Pulse Driver Board (A1) illuminates.
Barely perceptible ticking will be heard from the Pulse Driver Board.
Select 10 Pulses Per Second (PPS), 12 PPS, and 15 PPS at the selector switch. Confirm the rate of ticking changes.
Unplug the power cord.
Reconnect the cabinet fan.
Plug in the power cord.
The cabinet fan energizes.
Unplug the power cord.
Power Control Timer Board Testing:
If an AC Amp Meter can be found, connect it to monitor Primary 120 VAC Line Current.
Reconnect the High Voltage Transformer (T1) primary.
Disconnect the High Voltage Transformer secondary lead from the Switch Deck Assembly (A2). Isolate this lead.
Apply a piece of Duct-Tape across the Applicator Coil Fan and rotor (F1), to prevent it from turning.
Plug in the power cord.
A green indicator is given on the Pulse Driver Board (A1).
The cabinet fan energizes.
Energize Power Switch (S1).
The applicator coil fan does not energize.
After about 25 seconds, a Red LED should illuminate on Power Control Timer Board (A3). It should stay lit for four seconds.
The Red LED should extinguish for 15 seconds. The cycle should repeat.
The Yellow LED on the Power Control Timer Board should not illuminate with the Applicator Coil Fan Rotor locked.
The incandescent lamp (I1), on High Voltage Transformer (T1), should not glow with the Applicator Coil Fan Rotor locked.
Turn the power switch OFF. Unplug the unit.
Remove the Duct Tape from the Applicator Coil Fan.
Reapply Power. Turn the Power Switch ON.
The Applicator Coil Fan will come up to speed.
Verify aggressive airflow blows past the Applicator Coil.
After about 25 seconds, both the Red and Yellow LEDs on the Power Control Timer Board should illuminate.
A humming sound will be heard from the High Voltage Transformer (T1), indicating it is being energized.
The High Voltage Transformer should draw >3 amps unloaded.
Incandescent Lamp (I1) will glow dimly, indicating High Voltage AC output is present.
Lit Red and Yellow LEDs, a humming transformer, and the lit incandescent lamp will remain active for four seconds.
Red, Yellow, and Incandescent indicators go dark. Humming ceases. High voltage deactivates.
There will be a 15 second OFF period.
The cycle repeats: 4 seconds High Voltage ON, and 15 seconds High Voltage OFF.
Turn OFF the Power Switch. Unplug the power cord. Touch the High Voltage Transformer Secondary with the shorting stick. Reconnect the High Voltage Transformer Secondary to the Switch Deck (A2) AC Input slip lug.
High Voltage Testing
Take a good long look at your workmanship. Look for tools, metallic objects, or scraps of wire laying around inside the assembly. Remove debris as necessary. Wear safety glasses. Have people watch the unit from various angles, the first time high voltage is applied.
Plug the unit in.
Energize the Power Switch.
After 25 seconds, a loud clicking sound will be heard. (This is the sound of the repetitive magnetic pulse.)
Pulsing will persist for 4 seconds, followed by a 15 second rest period.
While pulsing, two Neon bulbs will flicker on Capacitor Bleeder Board (A6).
While pulsing, one neon bulb will flicker on Switch Deck Diode/Divider Board (A1,A2).
While pulsing, Incandescent High Voltage Transformer Indicator (I1) will glow dimly.
All Neon bulbs, and the Incandescent indicator, will extinguish between pulse trains.
This cycle will repeat, 4 seconds pulsing, with 15 seconds of OFF time between pulse trains.
Check all three Pulse Repetition Frequency settings (10 PPS, 12 PPS, and 15 PPS)
Pulse repetition rate will change when different switch positions are selected. Pulsing will sound stable for all three frequency settings.
If possible, log the Primary Line Current for all three settings.
If you have an amp meter connected to monitor primary line current, correct high voltage transformer primary phasing can be verified. This is done by swapping the High Voltage Transformer primary leads. With correct transformer primary phasing, the system should draw less line current. (This test isn't necessary. The system will work either way.)
Turn the power switch off.
Confirm all neon indicators extinguish.
Unplug the unit.
Use the shorting stick to discharge the high voltage capacitors.
Initial Testing is complete.
Step 14: Final Assembly
Retract the Applicator Coil Assembly fully, by sliding it into the assembly along the slotted holes provided. Verify Applicator Coil and Applicator Coil Fan leads accommodate the full range of travel without causing high voltage wires to come into contact with other leads or grounded metallic parts. Secure the Applicator Coil mounting screws.
Flip the main assembly over, and place it into the cabinet. Verify the cabinet's connecting umbilical cable is secured away from all major components. Install all mounting screws, to secure the main assembly into the cabinet. Move the Applicator Coil into the fully extended position, butting it right up to the cabinet side wall. Place a circular piece of tape (or any other marking) on the outside of the cabinet, to indicate the center of the applicator coil.
Close the cabinet, lock all latches.
Step 15: Functional Testing
Plug the unit in to a 120 volt outlet. Energize the power switch. Wait 25 seconds. Place the palm of your hand on the outside of the case, directly over the center of the applicator coil. Clicking will be heard. You will feel a sharp shock with each click.
In preparation for human trials, retract the applicator coil fully, away from the cabinet side wall.
A full study of current best practices in this field should be undertaken before stimulation is attempted.
One addict I know applied stimulation to the center of his forehead. He liked that. Clinical therapy typically targets the dominant prefrontal lobe, roughly three inches in front of the ear, and slightly higher up. In most cases, that will be the left hemisphere, for a right handed person.
Caution: stimulating only the non-dominant hemisphere may increase depression.
10 PPS is the normal waking-state brainwave firing rate. The NIH applied 15 PPS to the left Dorsolateral Prefrontal Lobes of CocUD sufferers.
If you're unclear about which way to turn the frequency selector switch, 10 PPS pulsing sounds slower than 12 PPS or 15 PPS.
Initial experimentation should begin with the Applicator Coil fully retracted. Try a four second burst of pulses. Effects will be subtle. Harm avoidance is our primary concern. Advance the Applicator Coil gradually, and only after existing effects are fully understood. It may take days to notice changes made to one's own mind. Go slowly.
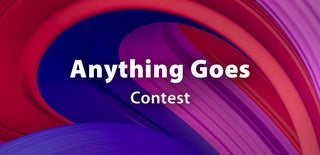
Participated in the
Anything Goes Contest