Introduction: DIY Workshop Build | Metal Structure
At the end of a long process of planning and thinking
My Workshop construction project begins!!!
it's time to build my storage/parking/home studio.
As part of the preparations for constructing our house, I asked our architect to include a plan for a storage area with covered parking for two vehicles. The architectural design of the storage/parking area is based on the regulations and laws of the municipality and adheres to the requirements of the various committees.
I entrusted the foundation and concrete pouring to a professional contractor who has all the engineering tools and expertise. They were accompanied by a construction supervisor who is also a building engineer.
In the initial stage, the contractor removed the topsoil and then spread and compacted the sub-layers.
They completed the slab according to the 0 level of the architectural plan.
I prepared iron plates with protruding "studs" at the bottom, to which the columns of the structure will later be connected.
Just before the pouring, I also laid down a conduit for future electrical wiring.
Months before the project started, I kept my eyes open and looked for opportunities to acquire construction materials that would be useful in building the Workshop.
Fortunately, I found excellent materials that were simply discarded, and with relatively simple adjustments, I found a way to reuse them.
I also modeled the structure in a 3D software long before the construction began. The 3D model helped me visualize the structure and also calculate the required quantities of materials.
This guide contains ten videos documenting most of the work process, which I filmed along the way.
To remove any doubt, I have practical experience in welding. In the past, I worked for several years in different metalworking shops. I recommend that anyone interested in doing this type of work themselves first study the basics and theory and try their hand at professional work under the guidance of experienced professionals. And don't forget, safety above all!
I hope you enjoy it :)
Omer
Supplies
Tools:
Welding machine
Welding mask
Welding gloves
Angle Grinder
Work gloves
Safety goggles
Respirator
Masking tape
Ladder
Hammer
Screwdriver Drill
Work boots
Paintbrush
Chalk Marking
Metal bend saw
Roller stand
C-clamps
Materials:
Welding Electrodes
Bolts with iron drilling head
Iron sheets
Iron profiles 100X100 mm 100X50 mm
Iron plates
Iron paint
Door track
Wheel rollers
Roller bracket
Concrete screws
Step 1:
Preparations
I'm really excited to introduce the first episode of a series of videos in which I will document the construction process.
In this video a contractor pours the concrete floor, and at the same time I begin to make preparations:
Before the pouring, I made an electrical infrastructure that would be buried in concrete.
I have prepared metal plates in advance as the basis for the poles and they will also be placed in the pouring stage.
Old deconstructed lampposts have found their way to me and I will use them as poles for the structure, I cut and prepare them to the desired dimensions.
Taking into account the state of heights given in the field (a laser leveler test was performed).
Step 2:
Poles installation
In this video my brother helps me to install and level all the poles of the structure.
Then I cut and prepare the materials for the next steps.
The iron profiles are so heavy that I just drag them on the floor :)
The roller stand I built really helps me with the cutting process.
Most importantly: measure twice – cut once!
Step 3:
Roof beams installation
In this video with the help of my neighbor and with the help of my brother we place most of the roof beams.
Unfortunately I didn't shoot all the steps from the beginning, but it's a repetitive process.
Clamps and vise grip is the main tools at this stage, before the beams are hoists I prepare a Temporary "step" to place the beam on.
Then check that everything is aligned, and tack weld.
Do not weld full welding so if there are mistakes it will be easy to disconnect.
Step 4:
Aluminum Windows
In this video I give new life to the windows I found lying in the dumpster, Aluminum frame windows in excellent condition with double glass layer.
Along with them, I also found their rail profiles and net, All I have to do is clean them well and rebuild the frame, the side profiles were missing and a few other small accessories that I bought from a local aluminum man.
This is my first time making a frame for an aluminum window - I learned how to do this mainly by looking at an existing similar window is installed in my home.
The aluminum man also gave me some tips and here was reborn great window!
After I completed the window, I took the external dimensions of the aluminum frame and made a metal rough opening in which I will later set the window.
You'll see the rest of the installation in the following episodes…
Step 5:
Install a window frame and continue construction
In this video, I install the window frame that I make in the previous video, and continue build the construction.
I also bring additional reclaimed materials to the construction site for later use, Metal sheet for the door and sliding door rail.
First I complete and connect all the remaining ceiling beams, and then I place the window frame
I add "legs" to the window and fix them to the floor using screws.
Later on I connect profiles to areas where there will be walls, one beam down 5 cm from the floor and a second beam in the middle of the height of the wall.
Step 6:
Install sliding door rail and door frame
In this video, I install the sliding door rail and the door frame.
I weld together two profiles of rails because I already owned a leftover rail.
I then make the door frame and attach the wheels to it, and put it into the tracks for the final location.
Step 7:
Sliding door cladding
In this video I make progress through different and vital tasks,
It seems that I am jumping from task to task, but in practice it is a work order that has logic and thinking behind it. 😊
I strengthen the sliding door rail to the structure by adding three flat irons that I made.
Later, I add more profiles to the door frame so that it fits the large, reclaimed metal surfaces, 2 of the surfaces are installed as they are and the rest I cut and fit.
To prevent the door from swinging, I fix guide roller to the floor.
Unfortunately, I didn't film the making of the roller bracket.
At the end of the roof structure, I add profiles to create an extension to the roof.
In preparation for the walls of the workshop, I ordered a bending metal according to the dimensions I defined, I weld the bent irons together in pairs because that's the maximum length they could provide me.
I will install them on the floor and their function is to prevent water and pests from entering the building.
Step 8:
Final preparations before roof and wall cladding
In this video, I make final preparations for the cladding of the building:
Completion of an extension in the roof above the window.
Installing the window I created in chapter 4 and sealing it.
Fixation and sealing of the bent metal (prevents the entry of water – and pests)
Add support triangles.
Step 9:
Roof & Wall installing
In this video my brother and I are installing the Warehouse walls and roof.
The original plan was to use an isolated panel…
Because the isolated panel is too expensive for me at the moment, I decided to install a simple sheet metal , Maybe in the future I will switch to insulated panels.
I cut the sheet metal with a circular saw with a special blade for metal.
Using chalk line I mark the positions of the screws, so that there are no Mistakes.
Step 10:
Almost finished
In this video I finish assembling the wall sheet metal.
I weld the lock housing, and assemble the door handle. (I also created the door handle myself but I didn't picture of the preparation, It is an iron pipe and 2 flat irons that are welded together.)
From Foamed polyethylene I make triangles to seal the "waves" of sheet metal.
And with strong glue, I seal and close the large slits.
The massive work is over, But there are still some tasks left to complete the workshop: Electricity, sealing the bottom of the door, arranging the interior space and more....
--------------------------------------------------------
You're invited to subscribe to my YouTube channel and follow all of my projects:
https://www.youtube.com/channel/UCkNrUodcQbCM8FDG...
social media:
https://www.instagram.com/kultakala_design_studio/
https://www.facebook.com/kultakaladesign/
https://www.pinterest.com/omerorbach/_created/
Your support is much appreciated!
New projects coming soon!
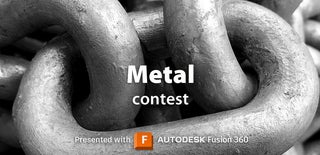
Second Prize in the
Metal Contest