Introduction: Design and Assemble a Wheelchair Lever Arm
Team Name: SHIPRO
Members: Isabelle Pearson, Hunter Vinsonhaler, Peter Tran, Omar Haroon, Sepidehsadat Sadreddini, Hung Fu Su
In this Instructable, we plan on showcasing our final project for BME 60C (Solidworks and CAD Design) at UC Irvine. The goal of this list is to layout exactly how to design, produce, and assemble the part that we presented, as well as give tips and tricks for future creators. Good luck!
Isabelle Pearson, Team Leader
Step 1: Do Your Research
The first step in any prototyping process is to research existing patents and designs. After some searching, our research lead determined that the main needs for this project were to produce a lightweight design, that was custom fit to the wheelchairs given to us by the Free Wheelchair Mission. The part would also need to be easily attached and detached to the wheel to allow for assembly by people of all skill levels. Our goal was to use the facilities and training available to us to create a basic prototype, including the us of FlashForge 3D printers, basic woodworking tools, and power tools.
A Note from Our Research Lead
The manual wheelchairs are the most important piece of permanent or temporary equipment for chronically disabled people. As a matter of a fact, the Wheelchair Foundation estimated that the number of people who need wheelchairs will increase by 22 percent over the next 10 years, with the greatest need existing in developing countries. According to USAID, it is estimated that 20 million people in the developing world need a wheelchair. However, the manual wheelchairs have their drawbacks and are not very ideal for every client. Despite of being too expensive and reduced transportability, studies have shown that constant use of hand rims leads to Repetitive Strain Injuries (RSI) of the shoulders, elbows, and wrists. Therefore, multiple alternative designs have been developed in the market including those that utilize lever arms to drive wheels. Lever-drive wheelchairs are mostly designed with two manually operated lever arms that transfer force to the wheels through a simple mechanical system. They are easier to push and can travel longer distances over rough terrains. Additionally, they are great exercise tool for the arms of patients that can help them prevent from sedentary life style. In short, they allow patients to apply force in a more ergonomic and mechanical efficient direction in comparison to manual wheelchairs. There has been lever drive wheelchairs for decades, but the price range is between 2000$ to 10,000$. Through research our team aims to design an innovative lever propulsion attachment for wheelchair that can be inexpensively manufactured and is marketable to people who live in developed or developing countries.
- Sepidehsadat Sadreddini
Free Body Diagrams
Above we have also included the Free Body Diagrams associated with the design used to assess the viability of the design. We used a gear ratio of 0.71:1 using the equation 1/(1+S/R), where is the stationary sun gear and R is the output ring. Above we have attached another equation used to calculate the torque applied to the wheel, where N_r is the ring teeth, N_s is the sun gear teeth, and T_c is the torque about the carrier (torque from the lever arm in our case).
For our prototype, we chose to almost exclusively create our part from 3D printed parts. Although this proved to not be the most durable material, the goal was just to demonstrate the effectiveness of the planetary gear system. In the conclusion we expand on the ideal materials that would have been used if possible.
Step 2: Design Your Parts in Solidworks
Find the full instructions for each part by following the links to their own instructable pages:
2.1 Sungear
https://www.instructables.com/id/Design-and-Assemb...
2.2 Top Stacked Gear
https://www.instructables.com/id/Design-and-Assemb...
2.3 Bottom Stacked Gear
https://www.instructables.com/id/Design-and-Assemb...
2.4 Planetary Gear
https://www.instructables.com/id/Design-and-Assemb...
2.5 Annular Gear
https://www.instructables.com/id/Design-and-Assemb...
2.6 Double Ratchet
https://www.instructables.com/id/Design-and-Assemb...
We've also attached all of our Solidworks designs below if you want to go straight to printing
Step 3: Print Your Parts
For this project we used FlashForge 3D printers that were loaded with an ABS Plastic. Our process was as follows:
1. Save all of your Solidworks files as .STL files onto a flashdrive
2. Input all of the designs into MakerBot MakerWare, convert your STL file into a printable file and load onto an SD card. The majority of our parts were printed at 20% infill, 2 shell, with the extruders set to 240 degrees celsius, and 60/90 extruding speed.
3. Insert that SD card into your chosen printer, making sure that the extruders have the appropriate amount of filament for the size part you're printing and the base plate/extruders are fully heated.
4. Begin printing! Periodically check on the print to confirm that everything is still working correctly and the part looks how it should.
Step 4: Assemble the Prototype
List of 3D Printed Materials:
(2) Sun Gears
(2) Annular Gears
(2) Double Ratchets
(2) Top Stacked Gears
(2) Bottom Stacked Gears
(6) Planetary Gears
List of Purchased Materials:
(4) 11"x7" Plywood Boards
(2) 17" long cuts of 1/2" diameter PVC pipe
(4) 1/2" PVC 90 Degree Elbow Fittings
(4) 1/2" PVC Tee Fittings
(2) 1/2"x3/4"x1/2" PVC Tee Fittings
(2) 6" Long Cuts of 1/2" Diameter Wooden Dowels
(2) Bike Brakes (available at most bike shops or on amazon)
(2) Single Loop Closed Extension Spring with .047" Diameter, 7/16" x 3-1/2"
(12) Flat Head Phillips Machine Screws #6-32 x 2"
(4) Machine Screw Nuts #6-32
(6) Round Slotted Wood Screws #2 x 1/2"
(2) #19 x 1/2 in. Zinc Wire Nails
(2) 3/4" Tube Straps
Find the Full Assembly Instructions Here:
Step 5: Iterative Testing
The most important step in prototyping is testing your part and making improvements. Along the way we discovered and improved upon a few of the issues with the design, however some issues were due purely to material choice and would be fixed in manufacturing.
1. Long Print Times
Because the parts were so large, many of the prints lasted 12+ hours and were not a viable option given our facilities. To counterbalance this, we chose to separate the stacked gear into 2 separate parts that fit together rather than one large part. This allowed us to run more short prints instead of less long ones, which was more ideal.
2. Consistently Applying Inward Force
After building our initial prototype. we discovered that although all of the parts worked perfectly, the assembly had three independently moving parts there was not enough inward force for these parts to stay together. The result of this was that people would need to be pushing in at all times to keep the assembly from falling off, which is obviously unrealistic. To relieve this, we designed the crossbar made of PVC to hold all of the pieces together. The part did do this, however the results were not quite what we needed and did not allow for independent motion as we had hoped. With more time we would have continued to test and perfect this inward force until the parts could have moved freely without falling off.
3. 3D Printing Issues
Because our part was entirely 3D printed, the prototype was much more costly to produce than expected. On top of this, the machines used to print were very unreliable and were only successful in printing our part mabe 80% of the time and even when they did work the parts printed were not strong enough for consistent testing. Our team also discovered that our tolerances needed to be much larger than initially anticipated to accommodate for any imperfections in printing. We chose to 3D print this prototype because that was the subject of this course and we had not received training in any other manufacturing methods. However, in a future iteration we would have recreated the design using metal machining to create a more durable and consistent part.
Step 6: Cost Analysis
3D Printing: 45 hours of printing @ $4/hour = $180
Purchased Parts: $36
Total: $216
Considering the quality of the prototype produced, the cost involved was very high due to the high use of 3D printing. For our manufacturing plan, we would ideally use a steel aluminum alloy similar to the material used to make bikes. This would produce a lightweight yet durable part that would still be easily assembled and attached to the wheelchair using mass produced fasteners. We would have also liked to 3D print the base plate and bar holder for the project, however the budget did not allow for it. Attached is the files we would have used if possible.
In conclusion, we are very satisfied with the design of our project, and we believe it has the potential to be a successful addition to the Free Wheelchair Mission assembly. However there are still some major materials questions that we would like to address in the future.
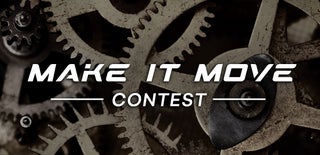
Participated in the
Make it Move Contest