Introduction: Designing a 3D Printable R/C Aircraft (Thin Walled, Lightweight Printing)
About two years or so ago, videos about 3D printed R/C aircrafts popped up on my suggested YouTube feed and since then I've wanted to build one of my own. I managed to find plans online and was intrigued by the immense amount of detail given to the internal structure, unfortunately, I did not have access to a paid slicer software capable of slicing such complex internal structures and the free slicer I was using was capable of slicing only the external skin/structure.
I figured that I might as well print the aircraft files I found online with conventional infills (hex, triangle, line, 3D gyroids etc.), a feature available with almost any slicer software out there. My printed aircraft turned out to be twice the anticipated weight and had a terribly high wing loading which made it fast as rocket.
For this reason I decided to do my research and figure out why my slicer was not able to print the parts and find a way to design an aircraft which is lightweight, strong and can be sliced with any slicer out in the market.
This instructable will take you through the process I went through, problems I faced and solutions I tried out to overcome those problems so that when you wish to design your own 3D printed aircraft, you don't have to go through multiple failed prints and have to constantly tweak settings to get the right print and can focus more on the design, aerodynamics and aesthetics of your aircraft.
3D printing makes manufacturing complex geometries significantly easier provided that you know the limitations of your machine and slicer. If you have some experience with 3D modelling, you could even take scale renders of warbirds and iconic looking aircrafts and build them. Some scale projects which would take you 400-500 of hours to painstakingly design and build with balsa and fiberglass would take just 100 hours to design and a couple of hours to assemble if 3D printed.
Supplies
Servos (typically 9g for the size of aircraft in this instructable)
BLDC Motor (2212 980kv Motor in this project)
ESC (18A w/ BEC in this project)
Propeller (1047 in this project)
LiPo Battery (11.1v 2200mAh in this project)
Rx/Tx (Flysky TH9x in this project)
Pushrods (cycle spokes will also do)
Misc Hardware
A 3D Printer (Flashforge Guider IIs in this project)
A Slicer software (Flashprint in this project)
PLA filament (easiest to print with)
Step 1: Understanding the FDM 3D Printing Process
Fused Deposition Modelling (FDM) or Fused Filament Fabrication (FFF) is a type of additive manufacturing technology used by most desktop 3D printers you see out in the market. In the FDM process a thermoplastic filament (which can be heated and deformed) is heated to its melting point and deposited layer by layer to form a solid 3D body.
While depositing each layer of typically ~0.2mm height (adjustable on the slicer - can be made lower for higher resolution and higher for faster print time) the printer over-extrudes material so that each layer is able to adhere to the next as well over-extrudes the layer width of typically ~0.4mm (adjustable on the slicer however, constrained by the nozzle diameter) form a closed loop perimeter for each layer.
Due to the nature of the layer by layer deposition process of FDM printing, discrete layers can be seen on the printed solid resulting in an anisotropic load bearing capacity. The strength in the X-Y direction of the print wherein the profile comprises of a continuous filament is about 3-4 magnitudes higher than in the Z direction where layers are discretised.
In order to increase the overall strength of a printed object the number of perimeters can be increased thereby printing multiple walls instead of a single wall. Strength can also be increased by adding infill structures with the desired density. Conventional slicers in the market can be easily configured to change these parameters however, these solutions for adding strength to conventional 3D printed objects are too heavy to be effective for use in applications such as R/C airplanes and UAV's.
PS - Pictures below in this step have been taken from google for ease of explanation.
Step 2: Complications While 3D Modelling a Thin Walled Structure
In this section of the instructable I used Fusion 360 to model a section of a wing with a variety of infill structures in order to optimise for best strength to weight ratio.
Printer Settings:
Material - PLA
Layer Width - 0.4mm
Layer Height - 0.3mm
Number of Perimeters - 1 (use random start locations)
Infill - 0%
Top and Bottom Layers - 0
Retraction Length - 0.5mm
Extrusion Width - 109%
As a baseline I printed just the wing perimeter with a single wall and that turned out horrible. While the print was lightweight, it had no rigidity and warped very badly after cooling down.
For my first test print, I tried to do a conventional full truss rib sketch extruded 200mm modelled as a single solid body. Lightening holes were incorporated into the section and the wall thickness throughout the structure was 0.4mm. The 0.4mm wall thickness was chosen because that was the diameter of my nozzle (and the layer width as well) and the slicer would slice the entire structure as a single wall. The sliced model showed some lines running the span of the wing where the truss would join the skin, however, I did not think much of it and proceeded to print the file.
Upon printing a few layers, I realised that slicer was not able to generate a continuous tool path and there were big gaps at the same locations where I saw lines running through the span of the section on the slicer. I thought this could be due to the retraction length settings (reducing the filament retraction length in the nozzle would have the effect of more filament oozing out while the extruder moved from one shape to another in its tool path, potentially joining the gaps) , however, playing around with it did not help. I also tried to add fillets where the truss structure intersected the skin, but that did not solve the problem either.
The results for three significant cases above have been included below -
Case 1 - 0.4mm Skin Only
Ribs - No
Fillet - No
Retraction Length - 1.3mm
Weight of Print - 24g (estimated on slicer)
Strength - Very bad
Warpage - Very bad
Case 2 - 0.4mm Skin With Ribs
Ribs - Yes
Fillet - No
Retraction Length - 1.3mm
Weight of Print - 59g (estimated on slicer)
Strength - Did not test
Warpage - Did not test
Case 3 - 0.4mm Skin With Ribs
Ribs - Yes
Fillet - Yes
Retraction Length - 0.5mm
Weight of Print - 63g (estimated on slicer)
Strength - Did not test
Warpage - Did not test
Step 3: Eureka Moment: Successfully Designing a 3D Printable Thin Walled Structure
After trying to troubleshoot my initial design a few times, I realised that there was something fundamentally wrong with designing a single solid thin walled body with a complex internal geometry and did a lot of research and reached out to a lot of people on RC forums and found that everyone that successfully printed an aircraft did not combine the internal structure and skin into a single body, instead they designed the internal structure and skin as separate bodies, however, I did not know how to do so or what the constraints would be while doing so. It was time to find out on my own.
I began experimenting and changed my approach from extruding a sketch into a solid body to lofting a surface between two sketches (which allowed me to taper and twist the wing if I wished!). After lofting a 100mm tall surface, I created another surface offset to it on the outside by 0.2mm. This outer surface would then become the skin of my wing section by giving it a 0.4mm thickness. Using the top view of the inner surface as an outline I created a sketch with a matrix of cross members perpendicular to each other with a thickness of 0.8mm and extruded the sketch such that it would extend above and below the wing surface.
After extruding the matrix, I used the inner wing surface as the tool body to slice the matrix structure such that I would get the internal support/infill structure for my outer wing skin with a separation of 0.2mm (reason behind this gap was that over-extrusion of the filament would allow the skin and internal structure to adhere well). I then added a small feature to the internal support structure joining it to the outer wing skin section. Doing so allowed me to export the body as a single STL file.
Printer Settings:
Material - PLA
Layer Width - 0.4mm
Layer Height - 0.3mm
Number of Perimeters - 1 (use random start locations)
Infill - 0%
Top and Bottom Layers - 0
Retraction Length - 0.5mm
Extrusion Width - 120%
Print Speed - 100mm/s
Nozzle Temp - 240 deg C
Bed Temp - 55 deg C
Cooling Fan - Always
Upon printing this I found that the strength was quite good however the internal structure did not adhere very well the outer skin and could be pried off with gentle pressure. I also felt it could be lighter however, I wanted to experiment further with the separation distance between the skin and internal structure to see if that helped with adhesion.
I reduced the gap to 0.1mm (instead of 0.2mm) and the adhesion improved a lot between the skin and the internal structure. I then tried to print with supporting structure/infill matrix cross members thickness reduced to 0.4mm as opposed to 0.8mm and this helped significantly with weight reduction. In the last case I added lightening holes to the internal infill structure and that further reduced the weight while maintaining a similar standard of strength and rigidity. The strength and rigidity were tested for feel by applying force using hands.
The video linked to with this step shows you how I went about designing the final version with lightening holes.
The list below summarizes the results of this experiment for some of the interesting wing section prints:
Case 4
Chord Length - 100mm
Wall Thickness - 0.4mm
Supporting Structure Thickness - 0.8mm
Wing/Infill Structure Gap - 0.2mm
Weight Reduction Holes - No
Print Weight - 34.2g
Print Time - 3h 20m
Warpage - None
Compressing Strength - Excellent
Bending Strength - Good
Wall/Infill Adhesion - Bad
Case 5
Chord Length - 100mm
Wall Thickness - 0.4mm
Supporting Structure Thickness - 0.8mm
Wing/Infill Structure Gap - 0.1mm
Weight Reduction Holes - No
Print Weight - 34.0g
Print Time - 3h 20m
Warpage - None
Compressing Strength - Excellent
Bending Strength - Excellent
Wall/Infill Adhesion - Excellent
Case 6
Chord Length - 100mm
Wall Thickness - 0.4mm
Supporting Structure Thickness - 0.4mm
Wing/Infill Structure Gap - 0.1mm
Weight Reduction Holes - No
Print Weight - 30.3g
Print Time - 3h 19m
Warpage - None
Compressing Strength - Excellent
Bending Strength - Excellent
Wall/Infill Adhesion - Good
Case 7 - Best Strength:Weight
Chord Length - 100mm
Wall Thickness - 0.4mm
Supporting Structure Thickness - 0.4mm
Wing/Infill Structure Gap - 0.1mm
Weight Reduction Holes - No
Print Weight - 30.3g
Print Time - 3h 23m
Warpage - None
Compressing Strength - Good
Bending Strength - Excellent
Wall/Infill Adhesion - Good
Step 4: Designing an Airplane and Preparing It for 3D Printing
With help from tailwindgliders, I was able input the parameters for my design and ensure the aircraft I was designing would be airworthy. The link has been pasted below.
http://www.tailwindgliders.com/Files.html
I decided to use a T-tail design in this aircraft as I had never designed one and thought it would be a fun challenge to incorporate while 3D printing.
The excel sheet linked below shows all the parameters/dimensions I used while designing my aircraft. The stability analysis has also been included in this excel sheet.
https://drive.google.com/file/d/1ernyoVFZHIikcpt0f...
In efforts to reduce weight I incorporated the technique seen in the previous step while designing the wing and tail empennage. However, I used conventional gyroid infill at 5% for the fuselage sections in an effort to save time and because the fuselage itself wasn't that big to contribute to weight savings significantly.
For printer settings I used the following (Wing and Empennage):
Material - PLA
Layer Width - 0.4mm
Layer Height - 0.3mm
Number of Perimeters - 1 (use random start locations)
Infill - 0%
Top and Bottom Layers - 0
Retraction Length - 0.5mm
Print Speed - 100mm/s
Nozzle Temp - 240 deg C
Bed Temp - 55 deg C
Cooling Fan - Always On
For the fuselage sections I used the same settings but changed the following:
Infill - 5% (3D Gyroid Infill)
Top and Bottom Layers - 3
P.S. - The left side of the wing and elevator STL's have been included. Mirror them for the right side if you would like to print.
Attachments
InstructablesPlaneAilSecRoot.stl
InstructablesPlaneAilSecTip.stl
InstructablesPlaneElevExt.stl
InstructablesPlaneElevL.stl
InstructablesPlaneElevR.stl
InstructablesPlaneFuseFront.stl
InstructablesPlaneFuseMid.stl
InstructablesPlaneFuseRear.stl
InstructablesPlaneRudder.stl
InstructablesPlaneRudderExt.stl
InstructablesPlaneWingSecIn.stl
InstructablesPlaneWingSecMid.stl
InstructablesPlaneWingSecTip.stl
InstructablesPlaneWingSecOut.stl
Step 5: Printing the Aircraft
While printing, it is necessary to understand the limitations of FDM 3D printing. The following considerations have to be made:
- Designing with a strong base. It is necessary to ensure that there is enough contact area between the first layer and the printer bed so that the print adheres to the bed well. If the print is not stuck to the bed well, the print will fail. Using a small brim (2-3mm is always a good idea as it helps with bed adhesion and stops the base from warping.
- Overhangs and holes will require supports. All slicers in the market have auto support generation options as well as customised supports generation. While the printer I am using (FlashForge Guider IIs) has very good bridging capabilities, some printers may not and it is important to use supports where they are needed.
- Tolerances of your machine have to be taken into consideration while designing parts that fit into others or have parts that fit into them. Ways of getting around this would be by calibrating your printer and adding compensations in the slicer software or designing your part taking into consideration the tolerances of your machine.
- Orientation of the print will determine the directional strength of the printed object and also the printers capability of printing the geometry without supports.
The entire print took about 35-40hrs of printing time and weighed in at about 0.7kg.
Step 6: Assembling the Wing
Once the wing sections had printed and removed from the printer bed, I had to separate them from each other and trim the excess brim off.
Once the parts had been cleaned, I inserted an 8mm aluminum tube coated with a thin layer of two part epoxy (you could also use a CF rod and Medium CA glue to save weight) through the spar holes (highlighted in blue) of each section leaving about 5mm of excess tube on both wing tips. The slow curing time of epoxy allowed me to make adjustments incase my alignment was off.
After the epoxy had cured, I glued the wing tips on the end of wings. The 5mm of excess aluminum rod allowed for more contact area to the wing tips for the epoxy to glue onto.
I then proceeded to glue the two halves of the ailerons together for each side of wing and then used fibre-reinforced tape to mount them onto the wing. The flexibility of the tape allowed the joint to act as a hinge. While taping the ailerons to the wing, make sure to leave a slight gap between the trailing edge of the wing and leading edge of the aileron so that the aileron is allowed to rotate and does not bind in its movement.
Once the control surfaces (ailerons) were mounted, I spray painted the wing to mask the tape, making it look better. After the paint had dried, I mounted a 9g servo in the slot that was designed for it and hot glued it in place. I used plastic scraps for control horns and CA'd them in place. I then used cycle spokes as pushrods and 2mm linkage stoppers on the servo end as well as the control horn end for easy adjustments.
Step 7: Assembling the Fuselage
Once the parts had been printed and removed from the printer, I trimmed off the excess brim and removed the custom supports I had generated while printing.
First I mounted the motor to the nose section of the fuselage. This was a little tricky as the section was deep and required a steady hand and a tool extension to reach the nuts that held motor in place. I then used an old soldering iron to cut a hole on top of the fuselage so that I was able to plug in the wires from the motor to the ESC.
After mounting the motor, I used two part epoxy to glue the three fuselage sections together. Once the glue had cured, I inserted the 8mm diameter 600mm length aluminum tube covered in a thin layer of epoxy on one end into the tail boom mounting hole. Once the glue had dried, I melted a small hole in the back on the fuselage with a soldering iron to allow the wires from the tail servo to enter the fuselage.
On fitting the wing into the slot that had been designed for it, I realised it was very tight and sanded it a bit to give me the right fit. After the fit was right, I used a soldering iron to make holes in the side of the fuselage to run aluminum tubes through at the leading edge and trailing edge positions of the wing so I could use them as anchors to hold the wing in place using rubber bands.
Step 8: Assembling the Tail Section
Just like the previous steps, the excess brim was trimmed and supports removed.
The T-tail was designed such that it would have an all moving tailplane. In order to allow this movement, I designed it such that a small 8mm aluminum tube would be inserted through the vertical stabiliser connecting the two elevator halves while allowing it to rotate.
For one elevator section I glued the 8mm aluminum tube using epoxy and after pushing it through the vertical stabiliser and through the other section of the elevator, I drilled a hole through the elevator and aluminum tube and fastened it with a 2mm bolt. After this I spray painted the tail empennage.
I then hot-glued a servo in the slot and used a cycle spoke cut down to length with an L bend on the servo end and a linkage stopper on the elevator end to enable control. I then proceeded to align and glue the tail empennage onto the tail boom.
After the glue had dried, I soldered extensions to the servo lead so that it could run to the fuselage and pushed it through the hole I made in the previous step.
I then did a glide test after adjusting the CG of the aircraft and thought the tail area needed to be increased so I printed extensions and glues them on using epoxy.
Step 9: Setting Up the Electronics and Test Flying
After connecting the servo leads to the respective channels on the receiver, I powered up the aircraft. Once the servos had centered, I adjusted the servo arms and linkages and tightened them.
I then checked for the motor direction and that seemed to fine as well. Incase the motor was spinning the wrong direction, I would simply have to swap two of the three wires going from the ESC to the motor. After this I added control throw end points and exponential to each channel and ensured that I was getting enough control on each channel and with the responsiveness I wanted. I usually add 30% expo on the elevator and aileron. It was a bit tricky adjusting the end points for this aircraft as I wasn't sure where to start for an all moving tailplane, however, after doing some research and calculations, I found 20mm of travel for the elevator was good and about 10mm of travel for ailerons was sufficient too.
After adjusting the controls, I checked the CG and found that I was very tail heavy and ended up having to add some weight to the nose such that my CG was just slightly ahead of the 1/3 chord mark from the leading edge of the wing.
Video of the first test flight is included with this step
Step 10: Summing Up the Learnings and Improvements
Learnings:
- Extrusion width is a very important parameter while designing thin walled skin structures with custom infills which do not touch the skin surface. It is a good idea to over extrude. In my case an extrusion width of 120% seemed to work well. This would increase the weight of the print slightly however, it would ensure good skin/infill adhesion. The print quality also doesn't suffer much.
- Reducing the retraction length also helps with adhesion when the extruder switches from printing the perimeter to the infill structure. It does however increase the stringiness in the print.
- Higher printing temperatures will allow you to print faster ~ 100-120mm/s without any issues.
- In order to export the infill and skin as a single STL, you need to join the two parts at any place.
- While slicing the parts, you need to ensure that the entire base of the part is in contact with the printer bed. On flashprint, the base that is in contact with the bed is highlighted as blue.
- When slicing the parts, ensure that you are giving sufficient support to overhanging geometries. You can save on filament and the hassle of cleaning excess support material if you decide to go with custom supports instead of auto generated supports.
- The printed part is the stiffest where the infill structure criss crosses and that is what gives it its compressive strength. For that reason the lightening holes have to added such that they do not cut any material from the intersections.
- The skin/infill adhesion determines the bending strength. When bending occurs, there is compressive and tensile tractions generated which is highest on the skin/surface. If the skin/infill adhesion is not great, both the structures will bend very easily as can be seen in the picture below.
- Line width can be increased slightly from 0.40mm to 0.42mm to increase the adhesion in the XY direction of the print i.e. between the skin and infill. Alternatively you could reduce the gap between the infill structure and skin further.
- Layer height can be reduced from 0.3mm to 0.25mm to increase the adhesion in the Z direction of the print (spanwise for the aircraft) to improve layer adhesion and give a smoother print surface finish.
Improvements:
- The tolerances for holes were incorrect and needed filing/sanding. These compensations should have been accounted for in the design.
- The same printing technique used with ABS results in base warping. Usage of ABS would result in a lighter print. I need to figure out how I can print on ABS without this problem occurring.
- The fuselage could have been made lighter if I did not try to save time and used the same infill design I used for the wing and tail instead of the slicers gyroid infill.
- The tail empennage could have been designed with alignment features which would make the assembly process a lot easier.
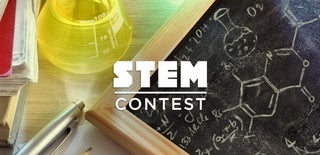
Participated in the
STEM Contest