Introduction: Designing and Machining a Custom Emblem
I am a second year welding student at Niagara College, Ontario. I often work with CNC routers at my work and I was recently commissioned to customize an "MVP" belt for my school's volleyball team (Previous one pictured above). I wanted to create a unique, custom piece that I could be proud of in the end, and that would advance my CAD/CAM skillset. I had some prior experience in Fusion 360 so I decided to give it a shot. Here's how my process went, and hopefully you can learn a thing or two from my successes and mistakes:
Supplies
Being a CNC based project, of course I needed access to a CNC machine. In this case I was lucky enough to be able to use the CNC router at my work which got that issue out of the way. Alternatively, you could outsource the production of the plaque to a machine shop or elsewhere at your own expense, however it would save the time and risk of generating toolpaths yourself.
Additionally, you will need the following:
- Material to machine (I used a piece of 6061 aluminum I had lying around)
- Roughing end mill (in my case a 1/4" endmill)
- Ball nose end mill for finishing pass. (mine was 1/8")
- A copy of Fusion 360, or another CAD/CAM software if you prefer
Optionally to make your piece stand out you can use a polish, and other materials to add some colour like I did.
Step 1: Initial Drawing
The first step is to come up with a design. I was aiming for a sleek, modern look with faceted triangles, while still maintaining the ouline shape to match the profile of the belt since that was staying the same. I used a photo of the original emblem to trace the outline, then added the logo in the centre and messed around with lines until I got a design I liked. The client wanted the logo in colour so I didn't end up machining the logo into it like I had originally planned.
Step 2: Make It 3D!
Next up was the fun, yet tedious task of bringing the sketch to life. I was limited to a thickness of 1/4" because of the stock I was using which made things a little difficult when trying to make the triangles 3D but it ended up working out.
To convert the sketch to 3D I used the extrude command, mixed with the taper function inside of it, to attempt to get nice-looking faceted triangles all over the emblem.
Step 3: Toolpath Time
Now that the piece is all modeled up it's time to generate some toolpaths! Mine consisted of 3 main operations. They are roughing, finishing and profile. I used a 1/4" endmill for both the roughing and profile operations, and a 1/8" tapered ball nose bit for the finishing pass. In this step it's important to dial in feeds and speeds, as well as optimal chip load and stepover for detail. I've still yet to learn a lot more about the CAM side of Fusion 360, and due to the deadline of the project I wasn't able to learn it in time so I used Vectric Aspire, which I have access to through my work along with a lot more experience. The key details I can provide you with for a baseline though are that I used an 80% stepover for my roughing pass at 20ipm and 7000rpm, and a 5% stepover for my finishing pass at 80ipm and 7000rpm.
Step 4: Workholding
I forgot to document this part of the process, but my method of holding the piece in place was to cut out the profile of the finished piece first, then to cut a zero tolerance pocket for the piece to sit in with a press fit to ensure no lateral movement during the cutting operation, and to remove the need for tabs on the final piece. You can see the piece set into the spoiboard in the next step.
Step 5: Rough Cuts
Now that you're ready to machine the piece, load up your roughing bit, zero it in and press start! Make sure to keep an eye on the piece while it's cutting to ensure the bit is getting adequate cooling if you're machining metal, and make sure the chips are adequately cleared out to prevent chip welding.
Step 6: Satisfying Finishing Pass
This is my favourite part of all: watching the whole thing take shape right before your eyes. This step is pretty much the same as the roughing pass, except this time load your finishing bit and finishing pass gcode and run the machine. Again watch the machine while it runs so you can stop it if anything goes wrong, and try to prevent breaking bits.
Step 7: Clean It Up, Make It Shine, and Be Proud
Now it's time to admire your work! Give that emblem that you worked so hard on some polish and put it all together. I cut the logo out of acrylic on a laser cutter and used some epoxy to fasten it on. The facets on my emblem are subtle, yet with the polish they reflect light from many different angles, giving it a real stand-out appearance.
I hope this instructable helped you learn something and make a beautiful creation of your own!
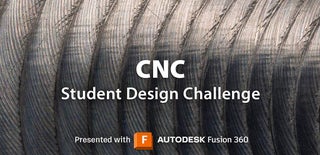
Runner Up in the
CNC Student Design Challenge