Introduction: Different Take on Quick, Inexpensive Plywood and 2x4 Shelves
I have a lot of stuff and therefore need a lot of shelves to store all if it. I have built them in many many different ways. This instructable is for bulk storage where simplicity, quick build, and low cost are the desired factors, appearance matters not so much. These instructions will focus on the shelves I am building now, they are relatively light weight, but can be adjusted for much heavier duty use.
Step 1: Tools and Materials
- Hand Circular saw and straight edge guide
- Table saw
- Lots of clamps
- Drill and Driver ( including counter sink )
- 4x8 sheet of plywood
- Deck screws
- 2x4's 8 feet long
Step 2: The Goal
In this build I am making relatively light weight shelves. Each shelf will be 16 inches deep and 8 feet long. This is the size ( less the kerf of your saw ) you get when you rip a 4 x 8 sheet of plywood into thirds. Sometimes I go really light weight an make shelves only 12 inches deep, just rip the plywood into fourths. In this shelf setup I will have 4 shelves with a fifth which is just the floor under the unit.
Note: In ripping the plywood I have found it easiest to put the plywood on sawhorses, clamp down a straight edge and use a hand held circular saw up against the straight edge. You can make a fancy straight edge as described in: Circular Saw Rip Guide--My Versionhttps://www.instructables.com/id/Circular-Saw-Rip-... or Make Straight Cuts Every Time With A Door Board - https://www.instructables.com/id/Make-Straight-Cuts...
Step 3: The Shelves
The problem with plywood is that it tends to sag under load. This is fixed by putting a rim from the 2x4 all around under the edge of the plywood. In the early days when I did this I might use a full sized 2x4 to do this. The result was a seriously over built shelf with a lot of space and expense lost to the 2 x 4. Switching to 2x3 was a bit better but still too much. I then hit on the idea of ripping the 2x4s length wise. If you rip it in half that cuts the space and cost in half. Using a table saw this is not too bad a task. For light weight shelves this is still over build in many cases and then I rip the 2x4s in thirds. This is what I will do for this set of shelves. With the plywood and 2x4 cut I lay the shelf out on sawhorses and clamp the ripped 2x4 to the bottom of the shelf. I carefully line up the 2x4 section and clamp into place. Often it is not straight so I may use a persuader ( like a hammer ) to nudge it into place. When a couple of feet are set up I use deck screws to fasten the clamped edge, then work down the shelf to the end. I generally use 5 screws for each side, perhaps few more if I had to fight the edging into place.
Step 4: The Shelf Supports
Like the shelf edging I used to use fairly heavy lumber like 2x4's for the supports. But now for this unit I will again use 2x4 ripped into thirds. The real trick here is getting the unit to stand up while the build is still incomplete. This is even harder while working alone. I have a couple of tricks for this all of which involve a substantial number of clamps. The pictures tell much of the story.
Unless you stop them the uprights will fall over, taking the shelf system with it. My big trick is to make a 3 sided box on the floor and clamp the uprights to them. Additional struts may be clamped in place to provide more stability. Check from time to time with a square and or a level. To raise the shelves clamp a block on each support under a shelf. Lift the shelf a bit and re clamp higher up. Work around the 4 uprights until the shelf reaches your per-marked height. Then screw it in place with a long deck screw ( I use a 3 in screw ) The blocks are no longer needed, put them back at the bottom ready to raise another shelf.
As you raise the shelves you need to take the box at the bottom apart so, as it provides less support add some more diagonals, using a shelf a one side of a triangle. Done with a bit of care you should be able to raise any number of shelves to whatever plan you have. While the shelves are being raised, or when done install some diagonals permanently. You can use ripped 2x4's or even lighter weight material ( I use what ever comes to hand including scraps and left overs )
The stiffness comes more from the geometry than the material. Triangles with roughly equal sides seem to give the most strength and stiffness. When all the shelves are up I add 2 more vertical elements so the shelves only span 4 feet between supports not 8 feet. This seems stiff enough for me.
Step 5: Variations
There is nothing magic about plywood, you could uses osb or mdf, but the savings is small enough that I would normally stick to plywood. For light weight shelves ½ inch thickness should do, ¾ should be enough for all reasonable shelves. As the load gets higher you might move from 1/3 of a 2x4 for the edging to ½ of a 2x4. Similarly for the uprights, sometimes even using a full dimension 2x4. If you can fasten into a wall even in just a couple of places you can make the shelves really rigid.
The following are links to similar projects, but without ripping the 2x4's and using the temporary box.
- Cheap Storage Shelveshttps://www.instructables.com/id/Cheap-Storage-Shel...
- Build Easy Free Standing Shelving Unit For Basement or Garage https://www.instructables.com/id/Build-Easy-Free-S...
- Storage Shelvinghttps://www.instructables.com/id/Storage-Shelving/
And here is an instructable which uses ripped 2x4's: DIY FRAME from a 2x4 Fresnel Lens Frame Artworkhttps://www.instructables.com/id/DIY-FRAME-from-a-2...
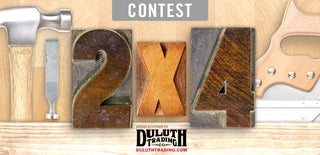
Participated in the
2x4 Contest