Introduction: 3D Printed Dremel Spirograph
Please vote for me in the 3D Printing Contest!!!
Step 1: Model the Parts
I work with Autodesk Inventor at work and am allowed to use it at home with our licensing, so I use it at home as well. There are many free software options but because I'm familiar with Inventor that's what I stick with for my personal stuff, too. With several interfacing parts, the method I like to use for modeling assemblies is to create one part file with each individual part betting a new solid. Inventor does a very good job with this method and it seems to be the most reliable parametric method within Inventor. In my experience projecting geometry part to part within an assembly file is not (at all) reliable.
My plan was to model an outside track, a geared follower and a Dremel mount that would go inside the geared follower. The Dremel mount was necessary to let the Dremel rotate without having to make every turn the geared follower made. After getting started with the modeling I realized that in order to fit the parts on the print bed of the printer I had access to the outside track would have to be in multiple pieces. To simplify the files I made the track into four identical pieces that locked together, so the number of teeth had to be divisible by four so they would split up evenly.
Inventor does not actually model threads when you put a thread feature in the model, so for the purpose of 3D printing you have to create the actual geometry of the threads.
The single part file ended up having three unique solids- a quarter of the outside track, the geared follower and the Dremel mount. I exported the solids into an assembly file to get unique parts from the one part file. After putting the other three quarters of track in the assembly to check fit, I created my .stl files of the three components.
The printers I have access to are Makerbots, so I use their free desktop software Makerware to create .thing files to use for printing. It took two files to fit all six pieces required.
Step 2: Print the Pieces
Once your files are ready it's time to print the parts. My parts printed somewhat well-well enough to use but certainly not perfectly. Printing them with a raft may help the print stick to the bed and not warp (and sometimes not so much) but it usually creates some extra cleanup.
I modeled in .5mm clearance between the teeth locking the outside track together and they required very little work to get them to fit, just some very minimal filing.
I tested the follower within the track and it worked well. My first file for the Dremel mount was a bit too tall, so I updated my model and printed another that worked much better.
Step 3: Assemble and You're Done...For Now.
Once you put the track together and Dremel mount on it's time to try it out. I didn't model mounting holes into the track because I didn't want holes in the workpiece, so I always planned to clamp them down. You need to adjust the bit in your Dremel to protrude through the mount in the geared follower to the depth you want it.
I did my initial test in plywood, and it was working well, but my bit was dulling rather quickly. I recommend putting a mark on the follower that lines up with the track four where you start-if you have to stop and start over again, you need to start in the same place in order to make sure your cut spirograph pattern lines up with itself.
What makes this not the last step is that during my way around the track, attempting to complete all the revolutions to complete the entire pattern my bit dug into the wood oddly. It turns out that the cutting produced enough heat to soften the plastic, which then allowed the Dremel mount to push into the follower.
In order to move forward, my next step is going to be to make the Dremel mount and the geared follower out of aluminum. I will print new parts scaled up by 2% for casting and use them as investment casting blanks. There is an Instructable "How to Sand Cast 3D Printed Objects" which has information on the process.
Thankfully the design concept works, and so now it's simply a matter of finishing my furnace preparations for the next phase of the project to be complete.
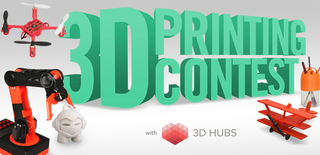
Participated in the
3D Printing Contest