Introduction: Dual Mode Windup Car
Dual Mode Windup Car is my first attempt at an enclosed windup vehicle. My previous designs have been "open chassis" to reduce weight, and of course so that I could watch the gears in motion (I truly like watching gears in motion, but it's just a hobby, I hope). This enclosed windup vehicle is a significant weight increase over the open chassis designs, and to compensate I did increase the final drive gear ratio from 1/25 to 1/16 to increase the torque. As such, I also strengthen the axles and gears to handle the increased torque. After testing, this vehicle easily traveled around 40 feet over the rough epoxy surface in my workshop. I'm still learning Autodesk Fusion 360, but it was instrumental in the design and appearance of this vehicle.
Dual mode refers to this vehicles two modes of operation, power and coast. Once the spring is wound using the key, releasing the vehicle propels it forward until the spring is depleted of its stored energy. This is the power mode. When the spring energy is depleted, the rear axle is disconnected from the spring motor via a floating pinion gear allowing the vehicle to truly coast. This is the coast mode.
The wheels and body top as shown in the photographs and video are designed for a dual extrusion printer, however I have included single extrusion versions of all the necessary parts.
You will need to purchase 16 "AS 568" size 222 (1 3/4 O.D., 1 1/2 I.D., 1/8" diameter) o-rings for the tires.
I probably forgot a file or two or something, so if you have any questions, please feel free to ask.
Designed using Autodesk Fusion 360, sliced with Cura 2.3.1, and printed on an Ultimaker 2+ Extended and an Ultimaker 3 Extended in PLA.
Attachments
Assembly.stl
Axle Front.stl
Axle Gear Idler Large.stl
Axle Gear Pinion Floating.stl
Axle Rear.stl
Axle Spring.stl
Body Left.stl
Body Right.stl
Body Top Flame And Robot.stl
Body Top Flame.stl
Body Top For Flame And Robot.stl
Body Top For Flame.stl
Body Top.stl
Cross Member.stl
Gear Axle Rear (12 Teeth).stl
Gear Idler Large.stl
Gear Pawl.stl
Gear Pinion Floating Guide Right.stl
Gear Pinion Floating (12, 8 Teeth).stl
Gear Pinion Floating Guide Left.stl
Key.stl
Pawl.stl
Spacer Axle Gear Idler Large.stl
Spacer Axle Spring.stl
Spring.stl
Wheel Hub, Left.stl
Wheel Hub, Right.stl
Wheel Left.stl
Wheel Right.stl
Wheel Rim.stl
Step 1: Print and Prepare the Parts.
I printed my parts on an Ultimaker 2+ Extended and an Ultimaker 3 Extended using .1mm vertical resolution and 100% infill for "Axle Spring.stl", "Key.stl", "Pawl.stl", and "Spring.stl", the remaining parts at 50% infill.
Print two "Cross Member.stl", two left and two right wheels of your choice (dual or single extrusion), and one each of the remaining parts.
Prior to assembly, test fit and trim, file, sand, etc. all parts as necessary for smooth movement of moving surfaces, and tight fit for non moving surfaces. Depending on the colors you chose and your printer settings, more or less trimming, filing and/or sanding may be required. Carefully file all edges that contacted the build plate to make absolutely sure that all build plate "ooze" is removed and that all edges are smooth. I used a flat jewelers file and plenty of patience to perform this step.
Study "Assembly.stl", carefully noting the locations and positions of the various components as assembly proceeds.
Finally some terminology. When "press" is used, this means the parts must fit tight and as such must be pressed together using a vice, C clamp, slip joint pliers or equivalent. When "place" or "slide" is used, this means the parts fit loose and should slide / rotate freely. The body side references of "right" and "left" are in relation to the vehicle itself as if you were sitting inside.
Step 2: Assemble the Axles.
Start by pressing "Axle Gear Pinion Floating.stl" into "Gear Pinion Floating (12, 8 Teeth).stl". Leave 4mm of the axle exposed on each side of the gear.
Next press "Axle Rear.stl" into "Gear Axle Rear (12 Teeth).stl". The gear must be centered on the spline of the axle.
Finally the spring axle is assembled in place on "Body Right.stl". Press "Axle Gear Idler Large.stl" into "Body Right.stl" (this axle also functions as the spring end mounting point). Slide "Axle Spring.stl" into "Body Right.stl" from the outside of the body. Next press "Spring.stl" onto "Axle Spring.stl" carefully noting the orientation of the spring on both "Axle Spring.stl" and "Axle Gear Idler Large.stl" (again, the spring end mounting point) and making sure the spring is firmly seated (there should be very little, about .5mm, endplay of the axle on "Body Right.stl" but it should rotate freely). Press "Pawl.stl" onto "Axle Spring.stl" again carefully noting the orientation of the pawl on the axle.
Step 3: Assemble the Body Right Side.
Press one of each of "Cross Member.stl" into "Body Right.stl".
Press "Gear Pinion Floating Guide Right.stl" into "Body Right.stl".
Place the idler gear assembly into position in "Gear Pinion Floating Guide Right.stl" noting the orientation.
Place "Gear Axle Spring.stl" onto "Pawl.stl".
Place "Spacer Axle Spring.stl" onto "Axle Spring.stl".
Place "Gear Idler Large.stl" onto "Axle Gear Idler Large.stl".
Place "Spacer Axle Gear Idler Large.stl" onto "Axle Gear Idler Large.stl".
Place the rear axle assembly into "Body Right.stl".
Step 4: Assemble and Attach the Body Left Side.
Press "Gear Pinion Floating Guide Left.stl" into "Body Left.stl.
Press the body left assembly onto the body right assembly. This step requires that all axles and cross members be aligned to fit into their proper holes.
Once completed, all gears should rotate freely and the floating pinion should easily slide throughout the guide slot.
Step 5: Assemble and Attach the Wheels.
Install the o-rings on the wheels.
Press two wheels onto "Axle Rear.stl", one right and one left, noting the alignment of the wheel spokes. Once installed, the rear axle should rotate freely. If not, make sure the body sides are pressed fully into position.
Press a right wheel onto "Axle Front.stl", slide the assembly into the body assembly starting on the right side of the body, then press the remaining left wheel onto the remaining end of "Axle Front.stl" again noting the alignment of the wheel spokes. Once installed, the front axle should rotate freely. If not, make sure the body sides are pressed fully into position.
Step 6: Attach the Top.
The top snaps onto the front and rear cross members. Noting the orientation, slightly spread the top, then position it around the cross members and snap into place.
Congratulations, you're done!
Hope you like it!
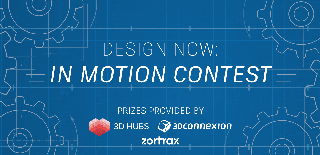
First Prize in the
Design Now: In Motion Contest