Introduction: Dynamic Layered Cube Light (Cubillumine)
The concept of this lamp is coexistence between warmth from wood and acrylic plates that changes the direction of light. This was a project for one of my core classes in Industrial Design, and it was a lot of fun!
Material list
- 1/8" plywood - 250cm² (around 39inch²)
- 1/8" acrylic board - 150cm² (around 24inch²)
- 1/4" diameter dowel - 3 × 2.5cm (around 1")
- 4 mm diameter steel threaded rod - 11.5cm(4.5")
- Two nuts that fit the diameter of the rod
- Locknut that fits the rod
- LED strip - 10~12cm (around 4")
- Switch (optional)
Tool list
- Laser cutting machine
- Orbital sander
- Sandpaper (800 grit)
- Clearcoat
- Brush (to apply the coating)
- Spray glue (optional)
Although it looks complicated, there are only three steps.
- Laser-cut both plywood and acrylic boards.
- Assemble the base to set up the LED (simply paste the laser cut plywood together with wood glue).
- Line up all parts with nuts through one shaft.
Let me explain the detail.
Step 1: Quick Sketch
These are the quick sketch to show how this design came up.
I wanted to design a lamp that can change its shape and adjust the amount of the light depending on how you feel on the day.
Step 2: 3D Modeling for Simulation
To simulate the final image with an accurate measurement, I used SolidWorks and made a 3D model. The thickness of the base to set up LED light and cord, and the number of layers were refined on this stage.
Step 3: Experiments
Here are my experiments with the shape of the cutout. I chose the fractal cutout because I preferred how it looked.
*The reason it looks white is I kept the masking tape on the acrylic board after laser cutting.
Step 4: Laser Cutting Template
Here is the template for the laser-cutting. You can download the PDF/ai template from the link.
*For those who haven't used a laser cutting machine before, I will share the note to prepare the data. If you have used it before, skip reading the note below.
How to prepare data for laser cutting
- Use Adobe Illustrator to prepare the data for laser cutting. Most of the laser cutting services accept the data made by Illustrator (=ai file).
- Check the maximum size which is accepted by the laser cutting machine you will use, and set up the size of the Artboard in Illustrator based on the maximum size. This Artboard's size will be the size of the materials (1/8" plywood and acrylic board) for cutting.
- Place the data of the cutting path on your Artboard from the template.
- Check color mode and set the "RGB" mode. (Not CMYK)
- Make sure the line weight is 0.001 pt. You probably won't be able to see the lines, but that's ok.
- Set up the colors of the lines based on how the machine is set up (for the machine I used, green lines defined the outside cuts and blue lines defined the inside cuts). *I shared the list of setting from my lab. Most of the settings should be similar to other laser cutting places, but ask the technician of your lab about the setting in detail.
Step 5: Laser Cutting Preparation
There are tips to succeed in beautiful laser cutting. They would make a huge difference if you didn't prepare it in a proper way. Don't let the technicians do all of the processes!
Apply masking tape on materials
Before laser cut the materials, apply masking tape to cover the surface. It will protect materials from burning. If you didn't put the masking tape on it, when the materials catch on fire from the laser (which often happens), the surface would get damage.
- Acrylic board: put masking tape on one side, set up the masking tape side on top for cutting
- Plywood: put masking tape on both sides
Control the machine manually
If you are in the position of controlling the pause/start button of the machine, be aware of the sign of burning and prevent catching fire by pausing the operation. Most of the time, you will see lots of smoke before it catches fire. Pause the operation when you see a lot of smoke until it's gone.
Step 6: Sanding Acrylic Plates
By sanding the acrylic plates, they diffuse light more and make it softer.
I would not recommend you sanding them by your hand as it takes so long to finish sanding all of them. Also, hand sanding could make an uneven surface and it could make scratches a lot on the surface. Instead, use an orbital sander.
*Wear an N95 mask and safety goggles during sanding. The acrylic powder can damage your lungs.
Step 7: Finishing the Wood Plates
Sand the wood plates with sandpaper (800 grit) to make the surface smooth and apply the clear coat.
I would recommend applying the coats two layers and sand the surface after dry each layer.
Step 8: Cutting the Rod and Sanding Its Edge
Cut an 11.5cm (4.5") piece off the rod and sand the edge so the nut turns smoothly.
*After you sand it, don't touch the sanded part soon. You would get burnt by the frictional heat.
Step 9: Making the Base Part 1
This part will be the bottom of the base.
Cut the 1/4" diameter dowels into 4x 2.5cm (1") pieces. You only need 3, but it never hurts to have an extra in case some of them are not straight.
Make sure that the dowels fit into the laser-cut holes. If they don't, use a drill to enlarge the holes.
By using wood glue (white glue), attach the 5 layers of the base part 1 shown in the laser cutting drawing; make sure the layer with no holes is on the bottom. You can also glue the dowels in place at this time. Clamp them together and wait for the glue to dry.
Step 10: Making the Base Part 2 and Setting Up the LED Strip
Glue the 5 layers of the base part 2 shown in the drawings together, and clamp them until dry. The small channel is the path for the cord.
Cut 10cm (around 4") off of the LED strip. If lead wires are not already attached, solder them to the +/- terminals.
Paste the strip on the walls inside of the base. LED strips usually have double-sided tape behind lights, so you can easily paste it on the walls without making any special efforts.
Optional
Set up the switch in the cord if you want. To do so, split either the positive or negative wire in the power cord, and solder the switch in place. It works fine without a switch; you just have to unplug the lamp if you want to turn it off.
Step 11: Assembly
Arrange all parts like the picture.
Run the threaded rod through the holes in each frame (from the fractal frames to base part 2) and use nuts to hold them in place.
Attach everything to the base part 1 by lining up the 3 dowels with the holes in the base part 2.
Step 12: Turn on the Light! (Fin)
Have fun with changing the shape of the lamp as you want!
Step 13: Experiments for the Screen (Optional)
Besides the simple sanded acrylic plates, I tried applying papers as well. As this lamp is easy to reassemble, you could use those screens when you are in the mood. In the example, I used Washi (和紙) paper (Japanese traditional paper), but you could use any kind of thin paper.
I used "3M 77 Super Multipurpose Adhesive Aerosol, Clear 16.75 Oz. Aerosol Can" to paste the paper on the acrylic plates.
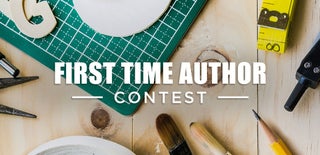
Second Prize in the
First Time Author Contest