Introduction: Easy Bicycle Framebuilding Jig
HI Everyone,
If you have ever wanted to build a strange bike, or even a garden variety one. This is for you.
Here is a design for a highly flexible, accurate and low cost jigging system.
I designed this to build my cargo bike and amphibious kinetic sculpture racer
A similar strategy could be used for 3d printer ways.
To build a hand made bicycle, a frame jig is a requisite to get an accurate product.
Both to insure your tubes are all filleted and fitted accurately, and to hold it exactly where you want it when it gets welded together.
To build most bikes, you will need only part of what is pictured here.
I made this to hold 5' wheelbase bikes with other unique features for the kinetic sculpture racer, which most frame builders don't need to do, nor are almost any frames this large. On the other hand, if you have grander or stranger visions, such as more wheels or riders, this could be scaled to those geometries as well.
the basic idea is to turn garden variety welded square steel tubing on edge to a 45° angle, this forms the equivalent of a "v" ways on a lathe. and provides and accurate x y & z axis jig that is accurate and easy to change.
the width and height can change easily while maintaining all the components precisely along the third axis.
Common parts, easy to make
Garden variety thin wall box tubing, short lengths of angle iron, welded to uprights, this is a very simple and quick way to put together a jig to build frames. it is much more important that the joints are accurately welded than having close fitting joints or pretty welds, as seen here.
Just like building a welding cart for your first welding tanks, this is a natural first project for a beginning frame builder, though this system could be scaled for motorcycles or any other project requiring accurate location of parts in space.
Like a bike frame, the primary requirement is to make the initial tool exactly right, as all the rest of the components will reflect that accuracy.
I am going to put this up without discussing the ways I used to determine the accuracy of the jig as it was going together, that will have to wait for another issue as it is critical and complex. Basically it involves the same methods and skills needed for a measuring frame, so enjoy. Stay tuned.
Tom
Hitchcock.design
Step 1: Tools and Materials Needed
A way to cut and weld metal tubing and angle iron. I used a wire welder and a metal cutting chopsaw.
you could do it all by hand if desired with a hack saw.
in addition you will probably end up drilling some holes and filing some metal.
measuring will be very important. a cellphone makes a very good digital level.
straight edges, square.
The project is designed to use primarily common 2" (50mm)and other size welded box tubing, light gauge angle iron and various brackets cobbled from the hardware store and donor bikes.
I put mine on a small folding table, which folds. the main beam could be clamped in a vice with the right v blocks or maybe held in a bike stand base.
Step 2: The Angle Jig
This is the core of the project and must be made very accurately.
This jig will hold all the other parts to the proper angle with each other for welding.
This involves a piece of 2" angle iron and some flat stock. the length is about 6' but not critical.
The angle is cut as shown, the small plates are guides to use to position the angles on a square when first conjoining them.
It's wise to do a fairly strong tack on this and all subsequent joints, and test them for squareness before locking them down.
Step 3: Making the Connections
To connect the jig parts together, two components are used, worm clamps and shims.
The worm clamps are pretty obvious, just be sure to get all the same driver size, then with a cordless socket driver, changes are really quick.
The shims are to compensate for the interference of the vertex of the box tube with the web of the angle iron.
any flat material, either plastic or metal that is the right shape and not compressible will probably work.
Common steel that you will buy will have this, and it is easily compensated for with shims. these allow the angles to be clamped to the box tubing with great rigidity.
To connect the dropouts, I used an old axle in a little u shaped bracket I had. the BB shell is held with aluminum cones, I machined mine.
The video shows most of the components and base.
Good luck with your creations.
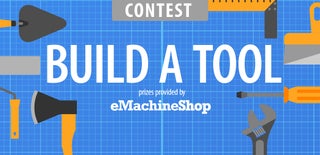
Participated in the
Build a Tool Contest 2017