Introduction: Easy DIY Variable Power Supply
Easy to replicate, cheap DIY work bench power supply, linear regulated voltage 1.2V to 17V, short circuit and thermal protection, three levels of current limiter: 50mA, 250mA and 1500mA (LM317) or 3000mA (LM350), depending on the voltage regulator IC used. Instructions to make the electronic circuitry, the enclosure, and mount all this together.
For this power supply I am using 19V switching mode original adaptor for an old laptop. You can have one or get one from your friends, or buy cheaply from a repair shop. My laptop adaptor is fixed to the shelf above the bench with two zip-ties, so it does not take any usable space.
There are a lot of steps, but every step is well illustrated and really easy to follow. This project was built many times by different people, one was built by a complete beginner. Well, he was well educated - he has two academic educations, one is theology, and the other is psychology...
Enjoy and good luck!
Skills needed
There are a lot of instructions over the Internet and here, at Instructables, so I will not explain these processes.
To cut, bore, sand and file sheet materials (aluminum for the heatsink and 3 mm sheet material of your choice for the enclosure).
To solder.
To make PCB - it is really easy and fun! Preferable method is Toner Transfer.
To measure voltage and current.
Tools
There are no special tools needed. A short list include:
Soldering iron, digital multimeter, saw, drill and bits, files and sandpaper.
Materials
Enclosure:
2.5 to 3 mm thick hardboard, 3 sheets 200 x 300 mm. You can substitute hardboard for any stiff sheet material of your choice.
White glue (PVA) or other appropriate glue.
Cyano-acrilate supe-glue, preferably gel.
Black matt acrylic spray paint (or other of your choice).
Transparent matt varnish spray (to make front graphics durable).
130 -160 g/m2 cardboard size A4 for front panel graphics.
Optional: Self-adhesive decoration folio. 200 x 500mm, to decorate top cover.
PCB (Toner Transfer):
Single sided copper clad board (PCB blank), 86 x 46 mm, 5 mm allowance on both four sides.
Adhesive tape.
Toner transfer paper (or any substitute, like photo-paper, magazine page, etc.)
Acetone
Etching chemicals (see your preferred instruction for etching PCBs).
Solder wire.
Desoldering brand.
Electronic components:
Dual digital AV meter WR005 (or similar) 100V 10A - $2.33
IC LM350T for 3A (or LM317T for 1.5A) - $0.22
IC LM7812 - $0.10
NPN transistor BC546 or similar - $0.01
3mm LED of your choice - $0.01
1N4007 diodes - 2 - $0.02
6A05 diode (optional) - $0.18
100nF 50V metal film capacitor - $0.17
10uF/50V electrolytic capacitor - $0.08
1000uF/25V electrolytic capacitor - $0.16
2kOhm variable resistor, linear (type B) potentiometer - $1.28
200 Ohm variable resistor for fine tuning - you can not buy easily such thing, I am using an old 240 Ohm Russian one, salvaged from a broken military transiver. So, if you can not find one, you can make it from an 1kOhm variable resistor, soldering 240 Ohm 0.25W resistor to it pins numbers 1 and 2 - $1.28
Resistors 0.25W - 10 resistors, as per schematics. They are everywhere, total price of all - about $0.03
Electro-mechanical parts:
4-pole speaker terminal - $0.76
3-pole PCB terminal - 3 pcs, $0.50
2-pole PCB terminal - 2 pcs, $0.36
DPDT On-Off switch D6F2 or similar - $0.76
DPDT On-Off-On switch MTS-203 or similar - $0.78
Miniature slide switch for the fan - $0.04
Panel mount cylindrical fuse holder - $0.38
Fuse 4A - $0.08
DC Jack 2.1 x 5.5 mm, panel mount - $0.15
Computer fan DC12V, size 40mm, 50 to 100mA - $0.76
Aluminum heatsink 3x50 x 75mm - plate or machined heatsink, salvaged from old PC power supply.
Fasteners (buy them at the local hardware shop):
M3 x 16mm bolts - 13 pcs
M3 nuts - 21 pcs
M3 washers - 26 pcs
PDF files for downloading - schematics, PCB layout, PCB drawing for Toner Transfer, general layouts, enclosure templates, front pane graphics.
Attachments
01_UPG_Schematics.pdf
02_UPG_PCB_Layout.pdf
03_UPG_PCB_for_Toner_Transger_SizeA5_Cardboard.pdf
04_UPG_Layout_TopView.pdf
04t_UPG_w_Temp_Contr_Layout_TopView.pdf
05_UPG_FrontPanel_Layout.pdf
06_BAS=UPG_Sections_Heatsinks.pdf
07_BAS=UPG_Main_Frame_Parts.pdf
08_BAS=UPG_Back_and_Front_Panels.pdf
09_BAS=UPG_TopCover_Panels.pdf
10_UPG_FrontPanel_Graphics_on_Cardboard.pdf
Step 1:
Make the PCB.
Step 2:
Solder the resistors on the PCB.
Step 3:
Cut and solder the wire bridge on the PCB.
Step 4:
Solder the diodes.
Step 5:
Solder capacitors.
Step 6:
Solder LM7812 IC (it is a power supply for the fan and the fan indicator LED).
Step 7:
Solder the current limiting transistor.
Step 8:
Solder PCB terminals, cut out labels and glue them to the terminals with super-glue. It is important not to glue the labels upside down. On the labels with signs only "-" means middle, "^" means up and "v" means down, with regard to the poles of the current limiter. switch.
Step 9:
Bend the legs of the LM350 (or LM317) IC and solder it into place. The aft end of the IC should be inline with the aft end of the PCB, thus allowing proper positioning of the heatsink.
Step 10:
Make small heatsink stands from scrap aluminum plate and position the heatsink. If it is needed, bend the legs of the IC with pliers and not force them!
Step 11:
Now our PCB is finished. Let's make the enclosure.
Step 12:
Using the PDF drawings as templates (glue them to the material), cut and drill the parts of the enclosure.
Step 13:
You have to double some parts (glue two layers together).
Step 14:
Glue the sides of the enclosure to the bottom. Keep the right orientation!
Step 15:
Glue front and back panels.
Step 16:
Glue one side of the top cover.
Step 17:
Glue the other side of the top cover, but place an 1mm cardboard between the side of the base and the side of the cover. This will make 1 mm slack between them and the lower part of the cover's sides will not try to bend outside. Sand the excess material of the cover.
Glue the legs and the inside studs. The holes in the studs and legs are not for bolts, but only to center them in their place.
Step 18:
Paint it black and prepare small felt pads for the legs.
Step 19:
Cut carefully the front panel graphic and glue it to the enclosure with white glue. Apply glue only to the enclosure and allow it to become semi-dry, then press the printed cardboard. Using modeling knife cut the excess paper around the front side of the enclosure. When the glue sets, spray matt transparent varnish on the graphics for durability.
The secret of this technology is not to show any part of the paper, which is cut or holed - these cuts and holes are usually ugly. But as you can see, except the LED, all other components on the front panel have boards, nuts, etc., so they will cover the cuts. The top cover is slightly wider than the base of the enclosure, so it will cover the sides of the paper. You can buy even a LED socket (making a bigger bore for it), so the last exposed hole will be covered.
Step 20:
Installation of all parts.
First, mark your variable resistors, to prevent any further mistake. Two red points are for the 200 Ohm resistor, which virtually not exist, so buy an 1 kOhm VR and solder a 0.25W 240 Ohm resistor between it's right (on the picture above) and it's middle pin. Thus you will have a 200 Ohm variable resistor, the drawback is, that it is not linear (the resistance is not exactly proportional to the angle of turn).
Step 21:
Make short bridges between right (this time we can see the opposite side of the VRs) and middle pins.
Step 22:
Make a bridge between the two variable resistors (about 25mm length).
Step 23:
Install the variable resistors into the frame and lead green and black cables as shown. Green to the VAR, and black to the GND.
Step 24:
Mount DC socket on the back panel, ON/OFF switch and fuse holder to the front panel.
Connect laptop adapter to the DC socket, connect it to the grid and check the polarity of the DC socket legs. Mark minus and plus with small labels.
Solder and lead thick black cable from the DC socket on the black to the input of the PCD, marked as GND.
Step 25:
Connect the positive of the DC socket to the fuse holder.
Step 26:
Connect the other terminal of the fuse holder to the lower pins of the ON/OFF switch. Use both lower pins.
Step 27:
Connect the middle pins of the ON/OFF switch to the PCB IN terminal, marked as IN+.
Step 28:
Mount the ON-OFF-ON switch, which is a current limiter switch, and connect it to the PCB as shown. Use different colors for wires. Use thick wires.
This is a bunch of cables, but you can easily identify where to connect them. The cables from the left side of the switch are going to the left PCB terminal, and from the right side - to the right terminal. The cables from the lower poles of the switch are going to mark "v" of the terminals, the cables from the middle poles to the "-" sign, and the remaining upper cables - to "^".
Step 29:
There are two types of speaker terminals, as shown. You have to connect the terminals together: positive-positive (red) and negative-negative (black).
Step 30:
Mount the speaker terminal, using M3 bolts and nuts. Mount it upside-down, so to open the holes for wires you will pull the bars upside with your thumb, while pressing down the enclosure with the other fingers. It is more convenient for small and light devices.
Step 31:
Now you can add a protective diode, connecting PCB OUT+ to the red terminals of the speaker terminal. Before this you have to solder small "heatsinks" on both side of the diode.
This will prevent the electronics from taking opposite voltage from a big car battery, for example, when the mains brake down. However, this will not prevent the AV-meter. My AV meter had some reverse voltages without any damage, but it is not guaranteed.
At the same time it will make the voltage regulation less stable, as the IC measures and regulates the voltage BEFORE the diode. And the diode has a voltage drop of 0.6 to 1V or more, depending on the current.
It is more better to be careful.
Step 32:
Mount the AV-meter. Fix it with 2-3 small drops of super-glue.
Connect the thick blue wire to the negative leg (black) of the speaker terminal.
Step 33:
Connect the thick black wire of the AV-meter to the GND output of the PCB, as shown.
Step 34:
Connect the thick red ire of the AV-meter to the positive leg (red) of the speaker terminal.
Step 35:
Connect the thin red wire of the AV-meter to the Vcc output (12V) of the PCB. This is the SV-meter's power supply.
Step 36:
Glue the slide switch into the hole of the back panel, using super-glue.
Connect the PCB terminal Vcc output to the middle pin of the switch.
Step 37:
Install the computer fan on the bottom of the enclosure, using M3 bolts and nuts. Note, that the air direction should be upwards!
Connect the fan's red wire to the upper pin of the slide switch.
Connect the fan's black wire to the GND pole of the PCB terminal.
Step 38:
Solder an 1 kOhm resistor to the anode of the LED. Solder thin red wire to the other end or the resistor.
Solder black wire to the cathode of the LED. Insulate the legs from each other (not shown).
NOTE: LEDS has anode (positive pin) and cathode (to ground). Negative pin is marked by a cutout of the glass at its side, and also the anode led is longer.
Step 39:
Glue the LED with super glue into its hole on the front panel.
Connect the red wire of the LED with the upper pin of the fan's slide switch.
Step 40:
Connect the black LED wire to the GND pole of the PCB OUT terminal.
Step 41:
Now the assembly is finished, only the heatsink is missed.
Step 42:
Mount the heatsink. You will have to release the PCB from the base and tilt it. If you are working with single-wire cables, this will be impossible. In this case you can turn the heatsink's bolts, so the bolts' heads will be on the back side, the nuts and washers - in the front side. Against the bolts you have to drill holes in the back plate of the enclosure for a small screwdriver.
Step 43:
Glue a label to the backside for the appropriate power supply.
Predrill 4 holes through the cover to the sides of the base and fix the cover with small black screws.
Thus the Test Bench Power Supply is finished.
Step 44:
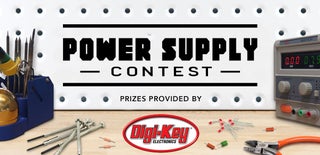
Participated in the
Power Supply Contest