Introduction: Electric Recumbent? Is That Really Possible?
I love cycling, but the hills around my town are punitive. Electric bikes are getting more popular and I became motivated to add some electrical power to my recumbent bike.
Researching the possibilities, I mostly found kits for regular bikes. Not much out there for recumbents. But I settled on a motor and controller kit that, although designed for regular bikes, seemed well reviewed and could be flexible enough to be mounted on my frame.
This Instructable is not a step by step instruction, but rather details some of the challenges I faced. I hope it may provide a useful reference for anyone trying a similar conversion. At the end of this Instructable is a list of links to the parts I bought.
Step 1: ORIGINAL BIKE
My recumbent was manufactured by BikeE, a company which built a lot of these bikes, then failed in the early 2000’s. The drive train is unusual. It has a single drive sprocket at the crank, with an 8 sprocket rear cluster, and a three speed internal hub in the rear axle. This gives it 24 speeds. The bike is very comfortable to ride, like sitting in a lawn chair. But even with 24 speeds, climbing hills is hard, as you can not stand up and put your weight into the pedals.
The frame is a rectangular aluminum tube. It's reasonably rigid for riding, but if you try to clamp onto it tightly it compresses and threatens to collapse. This presented a more of a challenge than expected.
Step 2: THE KIT
The ebike conversion kit I bought is designed to be mounted at the rear axle of a single speed bike, next to the chain sprocket. This requires an overrunning clutch (sometimes called a freeewheel) to allow both the peddler and the motor to drive the rear wheel without interfering with each other.
Definition: An overrunning clutch transmits torque in one direction only and permits the driven shaft of a machine to freewheel, or keep on rotating when the driver is stopped. On bicycles, such clutches permit the rider to coast without moving the pedals.
The first problem I discovered when the kit arrived was that the chain and clutch/sprocket provided were something other than standard 3/32” bicycle chain. This sent me to the web to buy the correct parts. I needed an overrunning clutch with sprocket for 3/32" chain, and a length of that chain.
Step 3: MOUNTING THE MOTOR
Here I try to explain how I managed to mount the motor onto the aluminum frame without squashing it. The main rail looks sturdy, but it is actually thin folded aluminum. The first picture shows my plan for clamping tightly on the frame.
I started with two steel fence “L” brackets from Home Depot. I drilled some holes to attach the motor to one and cut off the “L” on the other. Then using 4 ¼-20 bolts in new holes, I clamped the main bike rail between the plates. To prevent collapsing the rail, I inserted spacers onto the bolts through oversize holes on the left side of the rail, then clamped the left plate against those spacers. The spacers were cut so they are just under sized for the width of the rail. When it is all assembled, the mounting plates are tight against the spacers on both sides, and the main rail is only slightly compressed. Since the holes in the right side of the rail are still ¼”, the spacers and bracket on the right side also clamps the right side of the rail between them.
Here are the steps I took to ensure all the holes in the brackets and in the rails were aligned correctly:
- Clamped the two brackets together off the bike and drilled four ¼ inch holes through both plates.
- Temporarily clamped the plate with the motor onto the bike rail and adjusted its position so the chain was not too tight or loose. Then marked that position on the rail.
- Without motor, clamped both plates to the rail, adjusting them by eye to be aligned.
- Drilled the 4 holes in each plate using the ¼ inch holes as guides.
- Removed the plates, and enlarged the holes only on the left side of the rail so the spacers could slide in.
- I bolted it all together using 1/4x20 bolts and Nyloc nuts so that they wouldn’t rattle loose over time.
Step 4: THE DRIVE SYSTEM
As shown in the images, the motor is mounted near the front sprocket, forming a mid-drive solution. This has the significant advantage that by driving the crank arm, the motor and the rider both have use of all 24 gears. This mounting solution requires yet another overrunning clutch to allow the motor to drive the crank sprocket without the pedals turning. It turns out somebody makes exactly this. They are called Sickbikeparts.com. Very fitting.
I bought some very non-bicycle bolts, washers and nuts, and built an assembly:
- New chain-ring with overrunning clutch and crank attached to crank axle
- Original freewheel on one side of that
- Chain-guard on other side.
The chain-rings are spaced out by washers so the chains don’t interfere.
The motor drives the new chain-wheel, and through the assembly drives the main chain and the rear wheel. When I pedal without the motor, the overrunning clutch on the motor itself spins. This allows me to pedal without having to turn the motor. When the motor is working to move the bike, I can pedal to help, or not. And it only takes three overrunning clutches: one on the rear chain cluster (standard on bikes), one on the motor, and one for the cranks.
Step 5: BATTERY TYPE
The kit I bought has a charging jack and is really intended for Lead Acid batteries. After some research, I decided to use Lithium Iron Phosphate batteries (LiFePO4) which charge like Lead Acid batteries. The LiFePO4 batteries are much higher capacity for a given weight than Lead Acid though they are more expensive. The ones I bought weigh about 2.9 lbs each.
Why not use Lithium Polymer (LiPO) batteries? LiPO batteries require charge balancing between cells, which requires multiple connections to the charger, and in this application would require disconnecting the battery from the kit electronics in order to connect it to a charger.
LiFePO4 batteries are rated for more discharge cycles, and high current ratings. The LiFePO4 batteries can be charged from a charger up to 14.6V (6A) and I have two in series. So I located a 28V 3A charger on Ebay, and used that. (no link provided for this.)
Step 6: MOUNTING THE BATTERIES
My battery box is a repurposed camera case. It puts the weight of the batteries onto the main bike rail, provides some padding, and has space for the electronics.
I put a piece of plywood in the bottom of the case, then drilled two holes through the plywood and the bottom of the case to bolt it to the bike frame. A single tie wrap under the plywood and over the batteries keeps them from moving around.
Since I just installed this “solution” I have yet to verify its survivability.
(My first attempt at mounting the batteries was folded out of expanded metal and pop riveted together. That lasted a while, but one day when I hit a good sized bump, the metal just tore from the weight of the batteries. Now, with the weight of the batteries sitting on the bike frame, things should work better.)
Step 7: THE CONTROLS
The kit came with a right-hand throttle with integral handgrip, and a left handgrip to match. (Blue arrows in photo.) Mounting those was straightforward, though I did have to extend the wire length on the throttle control, due to the length of the BikeE frame.
The electronics also has a connector for an on/off switch, and one for a battery voltage indicator. (The on/off switch connector had to be jumpered for the electronics to run.)
I wanted both the on/off and the battery voltage indication on the handlebar. So I dug into the junk box, and found an old low brightness headlamp with mounting bracket. With a little carving, I mounted an inexpensive voltmeter and below it an on/off switch. (small red lever is visible below display in the photo at red arrow.)
Step 8: WIRING
Wiring the system was fairly straightforward. Each connector on the electronics package was labelled in English and Chinese.
The wiring diagram here was screen captured from one of the assembly videos. It shows all the connections, including those for headlight, brake light, brake levers, key, etc. which I did not buy with my kit.
The electronics package had some connectors into which I could push ¼” flat connectors, but most of the connectors were too small for any flat connectors I could find. My solution was to cut off one leg of a spade lug, and push that into the mating connector. Lots of blue tape holds the connections in place.
Step 9: IF I WERE TO DO IT AGAIN
The bike now has about 10 mile range in throttle only, further if I am peddling too.
I would strongly consider one of the other kits (links under Alternate Kits). Maybe one with a 36V motor, and perhaps 350W rather than the 250W I have. While that would require a third battery, the range would go up proportionally.
The motor is noisy, so a better quality solution should be considered.
Perhaps another look at LiPO batteries is warranted.
Overall, though, I am very happy with the solution as outlined here.
Step 10: WEB LINKS FOR PARTS USED
DRIVE KIT
ALTERNATIVE KITS
CLUTCH/SPROCKET AND CHAIN
https://www.amazon.com/ KMC-Bicycle-Chain-Silver-Gray/dp/B003AFOV84?th=1
LARGE SPROCKET WITH OVERRUNNING CLUTCH
http://sickbikeparts.com/chainring-freewheel-40-tooth/
http://sickbikeparts.com/front-freewheel/
http://sickbikeparts.com/cranks-170mm-freewheel-crank-set/
http://sickbikeparts.com/chainring-hardware/
http://sickbikeparts.com/crank-removal-tool/
BATTERY
https://www.amazon.com/TalentCell-LF120A1-Rechargeable-153-6Wh-Phosphate/dp/B07JF56C7L
VOLTMETER
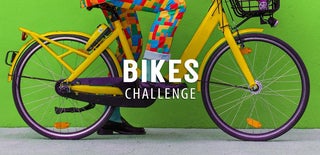
Second Prize in the
Bikes Challenge