Introduction: Engineering a Way to Enjoy Nature Using Generative Design, Load Simulations, Arduino and More!
Hello, my name is Nicholas Nguyen and I am currently 17, entering Grade 12 at Bayview Secondary School situated in Ontario, Canada. I am interested in engineering, and among many other activities, I enjoy using CAD software to design various items for fun or to 3D print, and have been using Fusion360 along with other CAD software for about 2 years. When I heard about this competition, I figured that it would be a interesting way to put my skills to use. My submission includes a bridge that was modelled through the utilization of structural load testing simulations and the help of generative design. In addition, I modelled the surrounding environment hoping to represent the connectivity with nature that the bridge can provide to the surrounding community. The bridge connects a suburban area with a trail that has long been under-utilized due to the pre-existing bridge structure breaking down. The bridge is also equipped with sensors to track usage rates, a scale representation of how it would work was brought to life through the use of Arduino.
I wrote this instructable to not only detail my process of creating this design, but to hopefully teach viewers (you guys) the various tools and functionalities that CAD software can provide. In this instructable, I show how to utilize structural load simulations, generative design, rendering, and modelling to bring designs to a new level, with detailed videos showing the process of how I carried out these tasks.
Lastly, I hope you can all learn a thing or two from this instructable, and even if you don't, I hope it was enjoyable to see the entirety of my design process. Enjoy!
Supplies
For this project, you will need the following:
Device with Fusion360 software installed
(The following are optional, and are only needed to recreate the bridges sensor)
Arduino UNO and breadboard
Arduino compatible Push-buttons
Arduino compatible LED's
Jumper wires
Hot glue gun + glue sticks
Cardboard
Step 1: Selecting a Site
The planned site for my pedestrian bridge will be in North Algona Wilberforce located in Ontario, and will be crossing the Bonnechere River. The purpose of this bridge will be to connect the community (on the right of the river) to the forested area (left side of the river). This will allow for easier access to the forested area, as the only other bridge crossing is about 2.8 km away, with it mainly being built for vehicular access. I also believe that the pedestrian bridge should fit in quite nicely with the surrounding scenery as well.
Step 2: Making Necessary Measurements for the Bridge Walkway
In order to make my bridge as accurate as possible, I made measurements of an existing walkway in order to ensure that the bridge will be able to be seamlessly integrated into the existing path. The existing walkway was measured to be approximately 2.68 m in width.
The concrete walkway of the bridge itself will also have expansion points to allow the concrete to freely expand or shrink based on different temperatures. The variance of temperatures during the Summer and Winter months in Canada will cause the concrete to undergo thermal expansion or contraction, and without the expansion points, the concrete will easily crack resulting in a loss of structural integrity. This will end up producing higher maintenance costs and a lower lifetime of the bridge itself.
Step 3: Testing Different Beam Dimensions for the Bridge
This step gives insight into the possible simulation and testing process that civil engineers might undergo during the design process of their constructions, and a detailed video outlines the process to do so. I used Fusion360's simulation option to simulate the deflections of the beam based on specific loads and dimensions to determine a good supporting structure for the bridge's walkway. In the civil engineering world, measuring the deflection of a beam to see if it lies within an acceptable range is an easy way to determine the structural strength of a design, determining if it is sufficient and safe to be put into use.
Screenshots 1 and 2 show the beam deflection of a 200mm x 300mm x 20000mm beam when subject to a downward applied load of 6000 lbs (~ 26700 N). The resulting beam deflection was minimal at only 15.7 mm, which was well within the acceptable range based on the beams total length. However, the dimensions of the beam are quite large, and will use much more material than necessary for the required purpose of a pedestrian bridge, with fusion360 also declaring it overbuilt for its intended load bearing purpose.
Thus, a beam of dimensions 100mm x 100m x 20000mm, which is smaller than the previous beam, was tested with the same load (screenshot 3 and 4). In this case, the maximum beam deflection was 299.8 mm (at the midpoint). This amount of deflection was greater than the generally acceptable value for beam deflections, which is around 1/180 of the length of the beam. Therefore, there is the issue of having a beam that will sufficiently support the bridges and people's weight, but also not use an excessive amount of materials in doing so, as it is seen that a significantly larger beam will have to be used in order to ensure structural stability if the support was simply a straight beam.
In order to solve this problem, a truss pattern will be constructed using multiple smaller beams in contrast to single straight beams to increase its resistance to bending under load, as well as not requiring a significant amount of resources to construct. As a simple example, screenshot 5 shows a simple truss structure is applied to the smaller beam and is subject to the same load, and it can be seen that the deflection amount is about 31mm less than when it was just the beam by itself since the truss works to distribute the load more evenly. A more complex truss design will be able to reduce the maximum deflection even more.
The same force will be applied to the final truss design to test its deflection under the same or greater load.
Step 4: Creating the Bridge Walkway + Truss Design Testing
By combining measurements and data from steps 3 and 4, the final walkway and supporting for the bridge was designed and modelled.
The design consisted of truss supporting structures along the edges of a rectangular prism formed by multiple beams. A portion of the final truss assembly that will be used for the bridge was tested under the same load that was applied to the beams in step 4. The truss assembly achieved a better deflection to length ratio than the 200mm x 300mm x 20000mm beam while using much less material in the process. This is due to the fact that the truss' allow the concentrated forces from the load to be more evenly distributed throughout the entirety of the structure.
The fact that this truss system takes much less material to construct while providing a great amount of strength will allow the cost of the bridge to be lowered without compromising its structural integrity. Screenshots 3, 4, and 5 include pictures of the walkway, its cross-section with the integrated truss design, and a schematic with some measurements to aid in the recreation of the walkway. The walkway also has arcs on its base to improve its load bearing capacity, as well as reducing the amount of material needed to construct it.
A video is included to help guide you through the load testing process.
Step 5: Modelling the Supports of the Bridge (And Rendering!)
For this bridge, I decided to use a combination of pile and cable supports. The main purpose of the piles at the base of the bridge is to effectively distribute applied loads from the bridge surface towards the ground. The use of wire supports reduces the need for an excessive amount of piles, which increases the aesthetic appeal, as well as reducing the disruption to the surrounding environment and substrate of the pond it is constructed in.
A video was provided for the modelling process of my supports. I decided to use a simple "2-pile" support with a truss like structure in between the 2 beams for added stability.
The cable supports will be attached from an arch directly to the bridge's walkway. However, instead of having the arch fully above the bridge, it will also be mainly extended below the bridge in order to reduce its obstruction to the view of the surrounding nature area. The cable and arch design I am implementing will more apparent in the later stages when I put all the components of the bridge together.
A video was also provided to show how I produced the rendered images of my support designs. Note that the video only shows the steps for in-canvas renderings, which is a good way to get an insight of how your final product will look like rendered, a video detailing how to produce final renderings is included in the last step.
Step 6: Generative Design
I used generative design in order to design the benches/seating area's present on the bridge. Seating is important since it allows for space where people can socialize and enjoy nature simultaneously. I am utilizing generative design in order to minimize the materials used, as well as potentially maximizing the aesthetic appeal of the benches. Common uses for generative design include the automotive and aerospace sectors with the aim of cutting down the number of different parts requires to construct parts.
A general overview of how generative design works is as follows:
- A designer or engineer creates a simple representation of the part while defining guidelines such as material, size, weight, force, cost, etc.
- The computer program considers the aforementioned "rules" and generates many potential design solutions in a relatively short amount of time (much more than we can ever imagine!)
- It is important to note that the more limitations/restrictions that you put on the generated designs, the more predictable they will be
- A design is then chosen that best suits the intended purpose and meets the architect's or engineer's expectations
A video was provided giving a more detailed step-by-step guide to utilizing generative design in Fusion360 for creating the bench. The file for the bench is also provided below.
Generative Design Bench 1
Step 7: Data Collection + Arduino Push-Button Sensor
This bridge will be equipped with a push-button/touch sensor beneath a certain panel of its surface to track the number of people that cross the bridge. Initially, I had considered using a motion sensor, but that has the potential to get obstructed with debris that can accumulate over-time. Collecting data on the amount of users accessing the bridge can give valuable insights into the induced demand for the bridge, which in this case essentially represents the number of people who want to access the trail on the other end as mentioned in Step 1. The importance of counting the number of users is mainly to acquire future funding, as this data is generally used when applying for grant programs. If the data shows that a relatively high amount of people are accessing the bridge, there could be more resources or capital put into maintaining and further developing the area with infrastructure that can improve people's access to nature.
User data can also give insights into what purpose the bridge is used for. For example, if the collected data shows that there are more users during the weekend than the weekdays, it could indicate that the bridge is mainly used for leisure or enjoyment. However, if the usage is high throughout the entire week, it could possibly indicate that it is a common route to commute to and from work or other necessary locations. This can also be extended to collect data for an hourly basis, showing at what times does the bridge become the most popular.
In terms of how my user-count sensor would work, there would be a plate located on the bridge with a pressure/push sensor that would be activated every time someone steps on it. There would inevitably be double-counts as people would generally commute both ways over the bridge, but for the purpose of the aforementioned uses it is sufficient. My scale replica of the sensor consists of an Arduino push-button and LED, with a panel hot-glued to a push-button as the replica "floor-panel" of the bridge. The Arduino code is attached below, with a video demonstration and pictures included as well.
Attachments
Step 8: The Completed Bridge Model: Putting It All Together + Form Modelling
In addition to the support systems, I had also designed, modelled and implemented railing to ensure safety of pedestrians, bridge outlooks for pedestrians to relax and enjoy the surrounding nature, and covers above the outlooks so that people can still enjoy the scenery during inclement weather conditions such as rain and snow.
A video is included of my design process for the entirety of the bridge, aspects of my design that ended up not being used or being changed/modified were also included in the video to emphasize the complexity of the design and modelling phase of any project, in the real-world or on Fusion360, and how my vision of my final project evolved as I; went deeper through my modelling process. Further videos are also included to show more detailed steps of more complex aspects of my bridge design, such as form modelling.
Step 9: Modelling the Surrounding Area
In order to give a better representation about how the bridge will be able to be incorporated into a community, I decided to challenge myself and design the surround landscape, buildings, and scenery (and you can too!).
I first started with the design and creation of a few bungalows to represent the community of focus situated in North Algona Wilberforce. I then added the forested area on the opposing side consisting of evergreen trees, as those are the most dominant tree type making up the abundance of Canada's forests. Hills were also created through the use of form modelling within the forested area. A river was then added below the bridge as well. The final Fusion360 file is attached below, which includes the completed bridge and the surrounding modelled scenery/landscape. A short video that shows the process of creating a final rendering is included along with the final rendering
This marks the end of this instructable, thank you all for taking the time to view my design process.
Nicholas N.
Fusion360 Bridge Across Pond
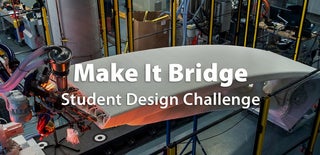
Second Prize in the
Make It Bridge