Introduction: 'Enterprising' Magnifying Lamp Upgrade
One of the most useful tools I have in my workshop is a Clarke SAM170 Desk Mounted Magnifying LED Lamp.
I use it as a desk lamp above my 3D printer and also as a magnifying glass when carrying out fiddly operations such as soldering small components. It is also a great light source when taking photographs for Instructables!
For many years I have thought that the lamp resembles the starship U.S.S. Enterprise from the original series of Star Trek. I decided to 3D print components to add to the lamp to make the resemblance more accurate.
This Instructable describes the transformation from lamp to starship and was my entry in the Space Contest 2021. It won a Runner Up prize so many thanks to everyone that took an interest in this project.
Supplies
Clarke SAM170 Magnifying LED lamp: Clarke Tooling
White PLA: Geeetech White PLA
Black PLA: Geeetech Black PLA
Copper PLA: Noulei Shiny Copper PLA
4 x M3*18 flat head self tapping screws: From this multi pack
Step 1: Before and After...
The two photographs show the magnifying lamp before and after the transformation ('cloaked' and 'uncloaked' if you prefer...).
One of the considerations in this project was that it should be easy to fit and remove the model so the lamp and magnifier could still be fully used. In fact, I have found that the unit is still usable in most situations. The model only has to be removed if the unit is to be positioned at extreme angles. In this case the nacelles would impede the adjustment of the arms and lamp enclosure.
A bracket was designed that allows the secondary hull and nacelles to be moved forwards and removed. This should be carried out carefully as the Enterprise can receive Klingon scale damage by colliding with the metalwork.
The primary hull transformation only entailed replacement of the removable dust cover.
Step 2: Producing the 3D Model Files
I use the application '3D Builder' published by Microsoft to create the required 3D models. The resulting 3mf files are then processed using the excellent Prusa slicer application to create the g-code files needed for my Prusa i3 MK2 printer.
Both programs are free and are available here:
3D Builder: Get 3D Builder - Microsoft Store en-GB
Prusa Slicer: PrusaSlicer
You will need 3D builder (or another suitable 3D design application) to view and manipulate the 3mf files included in this Instructable.
As I did not want to build the Enterprise from scratch I downloaded this excellent model from the Thingiverse website as a starting point: Starship Enterprise
In 3D Builder I scaled the model so the primary hull ('saucer') diameter matched that of the circular magnifying lamp housing (250mm).
I edited the model using the tools available in 3D builder to produce the components required to convert the lamp into the Enterprise.
The photographs show an assembled and an exploded view of the model.
The red object is a bracket that is fixed to the underside of the lamp. The green triangular plate slides into the bracket to attach the model. This design allows the model to be easily attached and detached from the lamp. This is necessary as the nacelles can impede adjustment of the lamp. Care should be taken when attaching and detaching the model to avoid damage.
The colours are for the purpose of description. In fact, all components should be printed with white PLA except the parabolic dish assembly (copper PLA) and the characters on the saucer section (black PLA).
I attach the 3mf files of the exploded and assembled views. These are provided for interest. The individual 3mf files for the various components attached to subsequent steps should be used for actual printing.
Step 3: Primary Hull - the 'Saucer'
The lamp has a removable lid that covers the magnifying lens to protect it from dust and fingerprints. In the Enterprise conversion this lid is replaced with a 3D printed version of the upper Primary Hull.
The 3D print features indentations that form the name and registration of the ship. The indentations are filled with 3D printed black characters.
Print the lid using white PLA - I used a nominal layer of 0.35mm with support but applied Variable Layer Height in Prusa Slicer so that more detailed sections were printed with thinner layers. See the attached screenshots.
Print the name and registration using black PLA - no support required. As the characters are small I used a layer height of 0.05mm.
The 3mf files are attached.
Carefully press each character into the correct position on the lid. Note that the characters are shaped to match the curve of the lid so each character can only be fitted successfully into the corresponding indentation.
Duplicate characters (e.g. the 'E's in Enterprise) are not interchangeable. Rotational symmetrical characters such as 'S' must be orientated correctly as the thickness varies from top to bottom.
This is a very fiddly operation, best carried out using the magnifying lamp and tweezers!
The characters can be pushed in fully using a flat metal object such as the handle of a scalpel (with the blade removed for safety).
Note that the full stops in 'U.S.S.' proved to be too small to extrude successfully so the final model features these as raised bumps that can be coloured black using a fine permanent marker pen.
Step 4: Secondary Hull - Front Section
The Secondary Hull front section should be printed with white PLA in the orientation shown using supports. I used a layer height of 0.15mm.
I added location pins to provide mechanical strength when assembling the model. A total of five pins are required:
Three have constant diameter along their length and are shown in white in the exploded view.
Two have a smaller diameter for half of their length - these are shown in blue on the exploded view. This is to allow some adjustment of the nacelles when joining the front and rear sections of the secondary hull. The larger diameter pin sections should be inserted into the secondary hull front section.
Note that the flat end of the pins should be inserted into the pinholes.
Glue the pins into the pinholes, ensuring that the dual diameter pins are located in the nacelles with the smaller diameter sections exposed.
I use Loctite Super Glue: Loctite® Super Glue Liquid Professional
Only small amounts of the glue are required.
Step 5: Secondary Hull - Rear Section
The Secondary Hull rear section should be printed with white PLA in the orientation shown in the first picture with supports. I used a layer height of 0.15mm.
Due to the height limitation of my printer I had to print the the very rear sections of the nacelles separately. Note that these are not interchangeable as the pin holes are slightly offset.
Glue two single diameter pins into the rear ends of the nacelles.
Glue the rear sections of the nacelles in place.
Attachments
Step 6: Assemble Secondary Hull and Nacelles
The next stage is to glue the front and rear sections of the Secondary Hull together.
First press the two parts together without any glue to check alignment. Carry out any required adjustments (e.g. removing any stray PLA that is preventing the sections fitting together well).
If all is OK, separate the sections, apply a small amount of glue to the interface planes and pins and carefully press the sections together, ensuring that the parts align well. It may be necessary to adjust and hold the sections until the glue has started to cure - this usually takes about two minutes. Leave the assembly for about 15 minutes (or longer) to allow the glue to achieve full strength.
Step 7: Dish Assembly
The assembly at the front of the Secondary Hull is made up of four parts; the central pin, base, dish front and dish rear.
The dish is split into two parts so only smooth surfaces are visible. The dish has to be printed with supports and these tend to produce a rough lower surface.
Print the dish components using copper coloured PLA. As they are small a thin layer size should be used such as 0.05mm.
The two sections of the dish should be printed with supports.
The base and pin do not require support material.
Glue the two dish halves together.
Glue the pin into the front of the secondary hull.
Glue the dish base to the hull.
Finally, glue the dish to the pin - there is a change in diameter on which the dish is positioned. Ensure the dish is perpendicular to the pin.
Step 8: Printing and Fitting the Bracket
The bracket should be printed using white PLA to match the colour of the lamp. Layer height 0.15mm.
In the orientation shown in the first picture no supports are required.
To fit the bracket:
- UNPLUG THE LAMP / MAGNIFIER FROM THE MAINS. Whilst the bracket design does not require any modification of the lamp casing this is a sensible precaution.
- Remove the dust lid from the lamp.
- Lift the lamp from its base and lay the lamp on its back.
- Unscrew and remove the existing four M3 x 12mm screws.
- Position the bracket over the screw holes.
- Gently screw in the replacement four M3 x 18mm screws. DO NOT OVER-TIGHTEN THE SCREWS AS THE BRACKET MAY CRACK. The holes in the bracket are close to the edges so the PLA is thin at these points.
- Replace the lamp in its base.
The final picture shows the fitted bracket with the model in place.
Attachments
Step 9: End of Mission
Slide the Secondary Hull up and back into the bracket being careful not to damage the nacelles or dish.
Replace the dust cover with the Primary Hull version.
Mission complete. You now have your very own Starship to orbit above your workbench.
Just try not to say "Engage lightspeed Mr Sulu" or "Fire photon torpedoes" every time you turn on the lamp!
This was my entry in the Space Contest 2021. It won a Runner Up prize so many thanks to everyone that took an interest in this Instructable. I look forward to seeing your versions of this project.
If you want to learn more about using Microsoft 3D Builder please see my Instructable:
'Mini Mansion' - Visualisation Aid for the Blind : 12 Steps (with Pictures) - Instructables
Star Date: 28-09-21
Planet: Swindon, UK
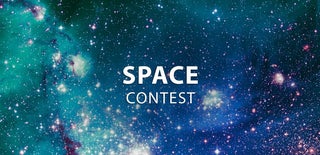
Runner Up in the
Space Contest