Introduction: Entry/Hall Table
My wife requested an Entry/Hall Table to go near the front door of our home. The opening was fairly narrow and long so, the design specifics are fairly particular to this space. The design allows for easy alteration to fit any particular space and would also work well as a sofa table.
The unique feature of this table is that the top appears to be floating about 1/2" above the legs and aprons. This was achieved using a sliding dovetail in-between the front and back apron to install risers which will be shown in detail in the video and discussed further in a future step.
Plans are included as well as a video showing the entire build.
Step 1: Tool and Materials
The following is a list of tools and materials used for this build.
Tools
- Table Saw
- Jointer
- Planer
- Band Saw
- Domino (Optional)
- Router
- Taper Jig
- Random Orbit Sander
- Drill
- HVLP Sprayer (Optional)
Materials
- 8/4 and 4/4 Walnut
- Figure 8 Fasteners
- General Finishes Arm-R-Seal
- General Finishes High Performance (Semi Gloss)
Note: All materials could be substituted with materials of your choice.
Step 2: The Legs
This build all starts with the legs. A shaker style leg was chosen to give the table a light feel. The legs are tapered on the two inside faces to a narrow bottom and the taper starts below the intersection of the rails.
The first step is to make the legs square using the jointer, planer, and table saw. Although particular measurements are called out in the plans, these are only guidelines and can be altered to fit your desired table.
From there, I used the Rockler taper jig to taper the legs to the desired size and then sanded to 180 grit. I also located for the dominos that were used to attach the legs to the rails.
Note: Although I used a specialty jig to achieve the tapers, a simple sled made from plywood and a few scraps could have been used and achieved the same taper.
Step 3: The Aprons
All the aprons will get a slight curve in the bottom. On the long sides of the table, it's important to know where these curves are to be placed to ensure that they don't interfere with the dominos (rail to leg joinery) as well as the location of the stopped dove tails to mount the risers for the top. The risers will be about 6" from the end rails.
Once the stopped dovetails and curves are located, the dominos can be cut as well as the curves. Again, all parts are finish sanded to 180 grit.
Note: The domino isn't required for this build. Traditional mortise/tenon, pocket screws, or dowel joinery could also work for this build.
For the stopped dovetails, a one time use jig was created. This allowed me to be able to accurately locate the sliding dovetails on both the front and back rail to ensure that the riser pieces to raise the top were located exactly opposite of each other. The sliding dovetails were cut using a dovetail bit in the router, a collet, and the one time use jig. I'll cover the actual riser in a future step.
Note: Although sliding dovetails are not difficult to produce, these risers could also be attached using pocket screws, dowels, dominos, or stopped dados. Just remember that these risers support the entire weight of the top as well as what ever is placed on that top later.
Once all the joinery is cut, it's time for a dry fit to ensure everything comes together per the plan. This is a great time to come up with your clamping strategy for gluing up the base. Thinking this through now really pays off during the glue up!
The final step on the aprons is to cut the curves. I cut the curves at the bandsaw but, a jig saw would work as well.
Step 4: The Top
The top is a glue up of two pieces. Attention was paid to ensure that the grain match as well as color match is good. The goal being to ensure that it looks like one slab instead of two pieces.
Once cut to size, a chamfer was added to the underside to give a lighter look to the overall piece using a router and chamfer bit.
Note: Increasing the size of this chamfer makes the top look lighter and gives the appearance of "lifting" off of the aprons further. Size of the chamfer can be increased or decreased to personal taste.
Step 5: The Base Glue Up
Even though this isn't a very big table, the glue up is fairly involved. There are 2 dominos in each rail to leg joint for a total of 16 dominos.
I used epoxy for this glue up to ensure enough "open" time to get all the parts put together and be sure it was square.
Once the clamps are in place, it's important to ensure that all connections are closed up tight and square and any squeeze out is removed. Any epoxy left on the surface will interfere with the finish later and it's easier to remove it before it dries.
Step 6: The Risers
Now that the base is together, it's time to create the risers that slide into the stoped dovetails that were cut earlier.
These are cut to the exact width of the distance between the front and back apron plus the depth of the sliding dovetails. It's important that the risers are 1/2" taller than the height of the aprons to achieve the illusion of a floating top. I used scrap to dial in the fit before committing to to more expensive wood.
The "male" portion of the sliding dovetail is cut at the router table. The dovetail bit is installed in the router table and several test pieces are made to ensure that they fit the female portion of the dovetail correctly. Once set, the actual pieces are cut and then notched at the bottom about 1/2" to cover the "female" portion in the apron but, not go below the level of the curve cut in the apron. It's important that these risers are about 1/2" taller than the aprons when installed as this is what lifts the top above the aprons.
Small curves are marked and cut in the top corners of the riser. This helps hide the risers from view adding to the illusion of a floating top.
Once installed in the table, a forstner bit is used to create the mortise for the figure 8 fasteners. The fasteners are pilot drilled and screws installed to secure them.
Step 7: Attaching the Top
The top is secured using the opposing end of the figure 8 fastener. This allows for expansion and contraction of the top without causing any binding in the connection which can eventually cause issues.
The base is set inverted on the top and centered. Pilot holes are drilled through the other side of the figure 8 fasteners and then secured with screws. Be careful to not drill all the way through the top!
Step 8: Finish
Being a dark wood, my finishing preference is to start with a coat of General Finishes Arm-R-Seal followed by several coats of General Finishes High Performance water based poly. I sanded with 400 grit sand paper between coats and applied about 5 coats.
Although this is what I chose to finish this table with, there are numerous other options that would work very well.
Step 9: Closing
This table has been a great addition to our house! It's often that we have visitors that notice the floating top and question how it's done. The finish holds up well to us tossing our keys and phones on it and looks as good today as the day I put it in its home.
This build took approximately 2 days to complete and the cost will vary depending on choice of materials and finishes.
I've added the plans here and they're available via the link in the previous step.
Some links are affiliate links so making a purchase helps support my work.
Attachments
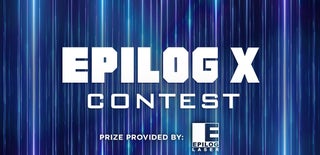
Participated in the
Epilog X Contest