Introduction: Eumig P8 Power Plug 3D Printed
Being an above-average analog film projector collector/user I have a few gems that need spare parts. This short Instructables might inspire you to get some obsolete electronics fired up again. I was short on power plugs for my Eumig P8 projector(s) so I decided to make my own.
PS before you scroll down to the comments… ELECTRONICS IS DANGEROUS!
Supplies
3D printer (I use my beloved Prusa MK3+)
Fusion 360
Old discarded power outlet for harvesting conductive metal
3mm screw and hex nut x3
Soldering equipment
3D Filament:
- PLA
- Flex 98A
Step 1: Take It a Part!
A good start was opening up the plug I had to see how it was designed and see if it was doable… Turned out the inside was pretty basic. That's what I love about old tech, you understand it at a glance:-)
Step 2: Measure… Twice!
I drew a quick sketch of the original plug and started adding measurements. Digital calipers are a must for this type of work. I made some adjustments but wanted to keep most of the original design.
Step 3: Fusion360 Baby!
No need to wait, I drew up the 1/4 side, since I could mirror it later. The original is also mirrored so you can swap the sides around. Now I could send one part to be sliced (Program to prepare the 3D file for printing) and duplicate it .
I made a test print as soon as I had a viable design, no need to be perfect in the first round because it's never perfect anyway. Doing a 3D prototype is more time-saving than trying to get it right the first time.
And rightly so minor tweaks had to be done.
One challenge when designing for 3D print is to avoid support material. Where can you omit overhangs and other non-3D-friendly constructions? I found printing this upright would be the best option to counter overhangs and support material. Where the opening for the electrical pins are I added a bridge to the design that I knew I later easily could cut off.
There is no other need for adjustments, it's time to assemble!
Step 4: Iterating Stage…
The first print was proof of concept, will it fit? A little tight, back to F360 and adjust. Print… now will the inner workings fit?
I made the cable holder a different color to make it more visible and different from the original. I also went and printed this part in flexible filament, 98A.
Step 5: Inner Workings
How this plug works is straightforward. But where could I source the metal for the inner circuits on my design? Asking for input is a good first step. I was told to check out the metal parts of an extension cord (found one at the dump). And bang on target, these parts were perfect, not exactly the same size but far within the spec. I cut the parts off and bent them to my desired size. Next I did like the original, drilled small holes (2mm) for better attaching the solder. I remembered to thread the cord holder before I solder on the connectors, Jipppppi! Jiggled all in place and boom… I was ready for the big test!
Step 6: Will It Run?
Before screwing the two parts together I tested the half plug in the projector… magic ensued… POWER!
PS when testing electronics, first plug into your appliance the to the wall!!!
Step 7: Final Assembly
I could not wait to put it all together and have a victorious smile spread across my face lit up by the projector lamp!
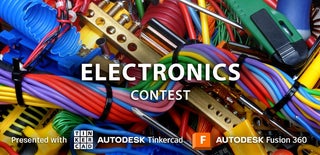
Participated in the
Electronics Contest