Introduction: Extract a Broken Lightning Plug From Your IPad
I dropped my iPad while it was charging. The lightning cable broke, leaving the tip of the plug lodged inside the port. One suggestion was to remove the tip with a tweezers or sharp object, but the lightning plug fits very snugly in its port. How I would do that without damaging the port was beyond me. After studying a photo of the internal works of the iPad, I also determined that opening it up would not be useful, and the risk of breaking the screen in the process made that out of the question.
So this is what I did instead...
Step 1: The Solution
Here is a summary of my steps.
- I drilled a hole in the broken piece of plug.
- Then I glued the drill bit back into its hole.
- And finally, I pulled out the broken stub with the attached drill bit.
This was simple, but wasn't easy. This required a good degree of precision, and a whole lot of patience.
Step 2: Supplies
You will need:
- A power drill (the smaller the better -- a smaller drill will be easier to handle -- a Dremel would have worked quite well).
- An Irwin #65 (.035 inch) wire gauge drill bit. I used a #60, but I suggest using the smaller bit.
- 5 minute epoxy (Devcon S205 is a good one). Superglue will not work.
- Masking tape
- Two or three toothpicks
You will also need an appropriate work surface, and something to secure the iPad while you work. I used...
- A mousepad (or 2) inverted to serve as a non-skid surface.
- Duct tape (to hold the iPad in place).
- A Black and Decker Workmate
also useful although not necessary...
- Some sort of drill guide or jig (improvised or otherwise)
Lacking a jig, a line level taped to the top of your drill helps you keep the drill level as you work.
Step 3: Secure the IPad
I used two mousepads face-to-face, bottom-side up, for a non-skid surface plus duct tape to secure the iPad in place. (The work surface you see above is a couple of two by fours attached to a Black and Decker Workmate. A jig this elaborate is not necessary. This one I had previously assembled for a different project, and this proved ideal for this one too.)
Step 4: Drilling the Pilot Hole
I used wood shims in the channel on my work surface to raise the drill so it aligned precisely with the lightning port in the vertical position on the secured iPad. Using marks on the work surface, making certain I did not drill any deeper than the depth of the broken stub of the lightning plug, and using a slow to medium drill speed, I carefully drilled a hole in the stub with a #60 Irwin wire twist drill.
The two by four rails on my workmate served as the perfect centering guide, but frankly I probably could have done this just as easily without this elaborate jig. I could have done this by hand providing I kept the drill level (the difficult part). As an alternative, taping a line level to the top of your drill will help you keep the drill level as you work. Something I have done in the past.
I reversed the drill, then slowly and carefully withdrew it from the pilot hole.
Step 5: Glue the Twist Drill Back Into the Hole
I cut a strip of masking tape about 1 inch long and exactly the width of the lightning port to protect the bottom side of the port from dripping adhesive. I carefully inserted the masking tape as far into the port as I could, and used a toothpick to press it down lightly.
Then I mixed some fast setting epoxy and rolled approximately 3/8 inch of the tip of the twist drill in the mixed epoxy.
I held the twist drill by its end for about 20 seconds and let any excess epoxy drip from the tip. Only then did I carefully insert the drill back into the pilot hole in the broken tab.
Why the Drill Bit?
You may be wondering why I chose to sacrifice the drill by gluing it back into the stub, rather than gluing say a wire or sewing needle into the pilot hole. Actually, I tried both of the latter, using super glue on a first attempt, followed by epoxy on a second. It turns out that neither the wire or sewing needle created a strong enough bond to remove the broken plug. The twist drill fit the hole perfectly and the groove in the drill allowed more adhesive to reach the opening, while improving its grip.
Even though the quick-setting epoxy cures in just a few minutes, I let it set for about 3 hours before trying to remove the broken stub.
Step 6: Remove the Broken Plug
After letting the adhesive cure thoroughly (about 3 hours), I carefully, but firmly pulled out the drill bit with the broken stub attached. Then I carefully removed the masking tape, making certain not to leave any bits inside (not shown).
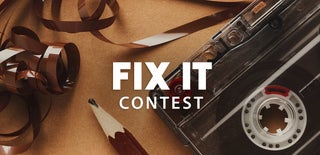
Runner Up in the
Fix It Contest