Introduction: Folded Wooden Bowl
Although the idea of fabricating collapsible bowls and cups assembled from folded sheets of plastics is not new, a few a years back I decided to take that idea and translate it into wood veneer.
I’ve worked on this project on and off for a few years now, developing a a variety of “finished” and unfinished prototypes. Very early it became clear to me why plastic was ideal for this use. Besides its strength and flexibility, its working characteristics were homogeneous throughout. Veneer, on the other hand, had special considerations that necessitated numerous design considerations plus more prototyping. Therefore this instructable is as much about the design process as it is about fabrication.
While I had always planned to create original designs, it turned out that new material, veneer, necessitated new designs. In this Instructable I describe my tips for prototyping as I develop one particular design. Hopefully it will help you avoid some of the trouble that I ran into, and expedite your own prototyping process.
Supplies
Tools
- Utility knife and sharp blades
- X-Acto knife and blades
- Metal straight edge
- Good quality scissors
- Drawing compass
- Stapler
- Good quality pencil and eraser
- Fine point Sharpie
- 5/32” leather punch
- 7/32” leather punch
Supplies
- Blue (easy release) masking tape
- Reposition-able spray mount adhesive (I recommend Loctite General Performance 100)
- 8 1/2 x 11 printer paper
For Prototyping
- Poster board
- 14 ply chipboard
For Fabrication
- 2 plies of wood veneer laminated back-to-back at cross grain*
- Sheets of sandpaper 150 and 220 grit
- Lighter Fluid (or Goof Off)
*see text for more information.
Step 1: Modeling the Design in Paper
When I first conceived this project, I had anticipated the the fact that veneer has a grain, yet I had underestimated just how directional its pliability would be. One thing I had not anticipated was that the readily available veneer would to me would come with a paper backing. The solution to this second problem provided a workable solution for the first. I ended up laminating two pieces of veneer back-to-back at cross grain to each other. Nevertheless, the wood grain would continue to present some problems. Repeated prototyping would become necessary to overcome these.
Process
The trick to developing a working design proved to be repeated prototyping in progressively more rigid materials, starting with paper, then poster board, then chip board, and finally veneer.
The prototyping process is as follows:
- Model rough designs in single sheets of paper using staples to fasten them. Then refine those designs with integrated fastening methods (i.e. tabs).
- Create a cut template in a vector (line) based drawing program (i.e. Adobe Illustrator), and scale the design to desired size for the next stage of prototyping.
- Convert (or Save As) the design to a PDF, and print using Adobe Acrobat Reader across several pages if necessary.
- Tape the multiple printed sheets together, and glue to the working material, poster board, chipboard, or veneer.
- Cut and assemble a prototype. Refine the prototype physically adding and/or removing material as necessary, and marking up the paper design with new features using staples and tape as temporary fasteners if necessary.
- Add the new features to the Illustrator drawing (or other vector software).
- Repeat steps 3 through 6 in poster board until you have a working poster board prototype.
- Repeat steps 3 through 6 in 14ply chipboard until you have a working chipboard prototype.
- And finally, using Acrobat Reader again, print out the design again, tape together, glue to veneer, cutout, sand, and assemble the design.
Step 1 - Modeling in Paper
The first step I took was to rapidly model some designs in 8 1/2 x 11 sheets of paper. When I started I had at least a couple of designs in mind, these included a boat shaped vessel, and square bowl with a round bottom. These ideas led to others. You’ll see example of these paper prototypes in the accompanying photo.
The key to this first step was to simply to play with paper, using a pair of scissors and a stapler, cutting, bending and stapling until I came up with rough “vessel” designs. It helped to have a couple of ideas in mind before starting, and these suggested others.
Step 2: Create a Cut Template
The next step was to create a cut template in Adobe Illustrator. Note that the software in the image above is Inkscape another (and free for use) vector-based design program, not Illustrator. I originally used Illustrator.
So why vector-based?
I could have created a template in any design software, vector based or otherwise, but vector based software allowed me to scale the design up or down repeatedly without losing any resolution.
For this Instructable I chose to develop the design which you see above.
You may also notice that the template contains some light vertical and horizontal lines. I added these to serve as registration marks. These were very useful when piecing together a template from a multiple page printout.
Step 3: Print the Cut Template Across Multiple Sheets
My next step was to print the template across as many 8 1/2 x 11 sheets of paper as required by the scale and the design.
For this step Adobe Acrobat Reader (free for use) is extremely useful. You can easily print a PDF across multiple sheets in Acrobat Reader by selecting the “Poster” option in Reader’s print dialogue. See the image above. Of course but you’ll first need to save your cut template as a PDF. Your vector-based software should be able to to this with the “Save As” option. Otherwise there are plenty of free online file conversion tools.
Specifically note the “Overlap” option in the “Poster” print dialogue. In the image above overlap is set to 0.000. I suggest using 0.500. This gives you a 1/2 inch page overlap which will help when piecing together a multiple sheet template.
Step 4: Assemble the Template
Now I reassembled the template from the multiple sheet printout using blue masking tape. Blue masking tape proved useful, because it was easily removable if some of the template pages need realignment.
After assembling the template I sprayed the back of it with Loctite General Performance 100 repositionable adhesive. This particular adhesive has some of the qualities of rubber cement, is low tack, immediately usable, highly repositionable, and leaves behind very little residue. This latter feature would be especially useful when it came to adhering the temporary template to the veneer.
Step 5: Cut Out and Assemble a Poster Board Prototype
In this step I create a poster board prototype.
Poster board prototypes is cheap, and a pleasure to work with. It is strong and pliable which allows for a lot of manipulation. I spent most of my time refining my design in poster board. I suggest you develop numerous iterations before moving on to more rigid materials.
To cut out the poster board from the template, I used a utility knife and a metal straight edge for the long straight cuts, a utility knife or scissors for large circular or curving cuts, a pair of scissors for small outside curving cuts, an X-Acto knife for small inside circular cuts, and the leather punches for the “relief holes”. More on those latter features later when I get to the chipboard prototype.
I tried an Olfa Circle Cutter for small circular cuts, but didn’t have much luck with it. It turned out I could follow small circular designs more closely with an X-Acto knife.
Assembling this first poster board prototype gave me a pretty good idea of the overall shape of the design and potential problems with that. It would be in poster board that potential mechanical or construction problems would reveal them.
A couple of things I discovered in this phase about the design in were that one, the design was turning out to be more rectangular, rather than strictly square, and secondly that it was too easy to push out the bottom of the bowl.
Playing with the prototype a bit, flexing it this way and that (a nice feature of the uniquely pliable poster board), I made some adjustments in my cuts, an adjustment in the shape of the bottom, and added some additional attachments. I usually made these revisions directly to the poster board prototype, adding taped on pieces of poster board where necessary, and drawing new cut marks where needed. I would usually add the revisions by hand to each successive template printout, only adding them to the vector drawing when I was satisfied with them.
It about 4 poster board prototypes in all, before I was satisfied with the poster board prototype.
Step 6: Back to the Drawing Board
When I was satisfied with the design changes, I added them to the vector drawing. I didn’t always do this.
Sometimes it was simply easier to make the changes directly on a freshly printed template. Many of these revisions changes would not make it into the following prototypes, but at some point any new and permanent features would eventually need to be added to the drawing.
Step 7: Repeat
It took me about 4 iterations of the poster board prototype before I felt ready to move on to the next stage, the chipboard prototype.
Step 8: The Chipboard Prototype
Building a chipboard prototype gave me insight regarding mechanical weaknesses in the design. Chipboard is thicker, much more rigid, and weaker than poster board. In fact, the chipboard turned out to be less flexible and weaker than my veneer. The qualities of the veneer fell somewhere in between those of the poster board, and the chipboard.
Even though mechanical failures, mostly cracking, became quickly apparent in this stage, I felt I needed to make only minor adjustments in the chipboard prototype. The veneer would at be stronger if not more pliable than the chipboard. I also planned to work around this by taking advantage of the grain of the veneer.
I made some minor design changes to resolve most of the mechanical problems. However, I was a bit concerned that they might negatively affect the overall shape, as I was trying to keep an overall square shape to the bowl. So I tried to keep the structural changes to a minimum. If I had wanted to, I could have gone back to the poster board to get a better idea of these changes on the shape, but I decided to forward anyway.
It was also in this phase that I found I needed to widen the “tab slots”. The thicker material put stresses on the fracture lines of the narrow slots.
Punch Holes
It’s in this chipboard phase that the leather punches really came into play.
You will notice the punch holes in the design. I have used these in previous projects where the flexing of rigid materials is involved. These holes are there for strain relief. I either enlarged the punch holes or added them at stress points to spread out fracture lines.
It was only two chip board prototype iterations before I felt it was time to start working in veneer.
Step 9: Fabricate the Model in Veneer
I still had some question marks concerning mechanical strength and shape, but it was time to start working in veneer. The only way to know for certain was to fabricate a prototype in veneer.
I had the veneer I was working with professionally laminated by the company I worked for. Nevertheless, some framing shops should be able to the laminate the plies for you. Also, if you like, you can purchase wood veneers with pre-applied pressure sensitive adhesive, and you can laminate these yourself.
Before I started working in veneer there was one more test I need to make, fabrication techniques. Although I had worked with veneer before I tested some of the tools I planned to work with on scraps of laminated veneer. One thing I have learned from working with veneer is that leather-working tools generally work quite well with veneer. These also work well for cardboard, especially dense cardboard.
After testing various options, I ended up using the same techniques and tools for the veneer, as I had with the poster board and chipboard. I used a utility knife, a metal straight edge, an X-Acto knife, and a pair of scissors to cut out the design, yet there were a couple of additional steps, removing the template, and sanding.
On the other prototypes, I left the templates glued to the model. I would remove it from the veneer.
I chose the template adhesive carefully. I knew from experience that yes, it would leave some residue, but very little, and what it left would be easily removable. After peeling off the paper template, I was able to wipe off the remaining adhesive with a shop rag soaked with a bit of lighter fluid. The lighter fluid dried quickly, left no odor, and unlike water would have done, did not swell the wood.
The other additional step was sanding. I had not anticipated this. I have worked with veneer before, and always gotten nice clean cuts using knife blades. But those were hardwood veneers, this was my first experience working in softwood. The softwood left some rough and splintered edges. Honestly I don’t completely recall which softwood this was, but it looks a lot like Fir, or maybe Pine.
So is it this design finished? No, not quite. There are still a few revisions I would like to make. There ended up being a couple of minor, but unanticipated stress lines where fractures are starting to occur. Ironically, these were not ones that became apparent in the chipboard prototypes. I believe I have some ideas on how to resolve these.
I would also like to make the design appear slightly more symmetrical where the tabs are concerned.
I would like to look into cleaner cutting techniques. If I could live with the burn lines (I’m not sure I can), laser cutting might be a useful way to cut out the designs. Nevertheless, utility knives worked pretty well except when cutting out the small outside circles of the tabs. I have already started looking into better tools.
And I would also like to explore decoration (perhaps cut decoration) and finishing.
But those are for another day.
If anyone would like a PDF of the template, or have any questions, please note that in the comments.
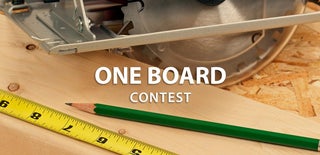
Participated in the
One Board Contest