Introduction: Fan Assembly for Fireplaces and Heat Radiators
Due to the rising prices of oil, the last years, people returned to using fireplaces for heating their homes.
Furthermore, I recently observed that even the so called energy-efficient fireplaces tend to spread the heat they produce to the surrounding walls. The small fans they are equipped with seem to be incapable of moving enough volume of air so no heat is lost, or at least most of the heat is transferred to the home environment.
Also for all of you that have the same problem with your gas/oil operated water heater bodies, stay with me in this Instructable on how to make a fan assembly in order to extract that precious extra heat during the winter season.
Step 1: Gather Tools and Materials
Tools:
- Drill with 4mm Metal Bit
- Metal Cutter or Metal Handsaw
- Ruler & Marker
- Plier & Cutter
- File
Optional:
- Scrap Wood (for drilling)
- Electrical Tape & Cotton (just borrow some from your wife)
Materials:
- 15mm*15mm Aluminum Angle (Length = 120mm * Amount of fans in series)
- 120mm Computer Fans (choose the ones with the higher CFM figure)
- 16mm M4 Screws with Nuts (4 for each fan used)
- 60-100mm M4 Screws or longer (for assembly base)
- 12V Power Supply (2A are more that enough)
Step 2: Measure and Cut Pieces
After deciding how many fans you will use, clean your workspace and place the aluminum angle on top.
I’m going with 4 * 120mm fans so each piece must be 48cm long.
For each assembly we’ll need 2 pieces of aluminum angle.
I've bought an 1m piece that unfortunately doesn’t fit in the picture.
If your hardware store has the ability to cut the pieces for you then go for it. Mine doesn’t so to cut it down to length I’m going to use a metal cutter.
Use the ruler and the semi-permanent marker to create a line 48cm away from the edge.
Mine is enough for 2 pieces so I will repeat the measurement from the other side.
Now cut them and verify they are the correct length afterwards.
After cutting the pieces file any rough edges and leave them aside.
Step 3: Prepare Fans
Later on, when mounting the fans on the assembly, you may find it difficult to screw the nut due to the structural supports the fans have. If that's the case with your fans, take the time to file down an indentation for the nut as it will save you from the hustle later.
As we will mount the front side of the fans on the aluminum angles, file the support from the intake side of the fan. Most fans have arrows indicating the intake side. If in doubt, wire the fan to the 12V power supply, light a match near the fan and identify the intake side.
Step 4: Drill the Brackets
For this you'll need 4 screws with nuts, 2 of the fans and the aluminum angles handy.
Start with the first fan and place it on the inside of the aluminum angle as shown. Place the scrap wood underneath it and with the 4mm bit, drill a hole on the bracket going throw the 2 holes of the fan. Push a screw through the freshly created hole and lightly tighten the fan in place with a nut. After drilling the first 2 holes, screw the first fan in place with 2 screws but not too tight as we will remove it again.
Then place the second fan directly next to the first one. Hold them in place and do the same drilling procedure for the 2 holes of the second fan. After drilling them, lightly mount fan No2 too.
After mounting the fan No2, remove fan No1 and place it directly next to fan No2. Repeat the process for as many fans as you have.
After you finish drilling the first aluminum angle, do the same for the next aluminum bracket and afterwards file down any rough edges.
Step 5: Mount the Fans
Place both brackets on the workbench and start placing the fans in between them. Make sure the fans are facing the correct way and their cables are aligned properly.
Mount the fans with screws and nuts as shown and tighten them. If you face trouble screwing the nuts, press turn the screw whilst holding the nut with another screwdriver or pair of pliers.
Step 6: Wire the Assembly
I happened to make 2 of these assemblies. One larger and one smaller with PVC angles. I will use the 2 fan version to demonstrate the wiring, but you can scale up to as many fans as you want.
First of all, computer fans either come with MOLEX adapters like the ones I used, or with 3pin or 4pin connectors. Albeit the different connectors, the wiring is the same.
Start by cutting the connectors, making sure the remaining cable length is enough.
Strip the cables and twist them. Do the same for the power supply cables.
Usually the red cable is the positive lead and black is ground. The power supply cable, may seem like black, but one of the wires does have some marking on it. In my case a faded white line. Usually this is the ground cable, but make sure to measure the voltage across it with a multimeter.
Something I did to test the polarity, that I don't recommend, is plugging the power supply to mains and touching the cables to the fans' leads seeing if they rotate. Reverse polarity won't kill the fans immediately but is not advisable to use such method.
Now that we know which way to connect the wires, twist the black and red fan wires together as shown.
Afterwards connect the red wires to the power supply's positive lead and black wires to ground.
Use heatshrink tube to secure the wires and even use solder if you like.
I also recommend using electrical tape after the tube to further protect the wiring.
Step 7: Standing or Hanging Mechanism
Now it's time to add feet or a hanging mechanism to the assembly.
Remove the 4 screws from the edges of the assembly and use the longer screws.
Be sure to check all the above annotated pictures for details.
In a nutshell
- For the standing version, use the head of the screw as the base of the assembly and use 2 nuts to secure the screw to the assembly.
- For the hanging version, push the screw through the assembly with 1 nut and use 2 other nuts as stops.
Step 8: Final Touches
- Standing version
If you plugged in the standing version you probably noticed noises coming from the assembly. That's because the fans create vibrations that cause the screws to make repeated contact with the floor, thus creating rattles.
In order to suppress most of the noise we need to dampen the vibrations.
Cut a small piece of electrical tape and inside put a small piece of cotton. Wrap the tape around the head of the screw and secure it with even more tape around.
Repeat on all the screws and if necessary add a second layer of cotton and tape.
- Hanging version
The wiring for the hanging version is a bit loose. To protect the cables from getting ripped if the assembly falls for some reason, be sure to snug the wires between the screws as shown in the pictures.
Step 9: Enjoy
I hope you all enjoyed this project as much as I did. This seemed like a pretty simple project at first, but a lot of problems occurred while testing it, and it ended up being a lot more time consuming than I first though.
Although the fans do tend to heat up the whole house nicely, so mission accomplished!
If you liked the project, make sure to share it with your friends. Thanks and, until next time, happy tinkering!
-Manos
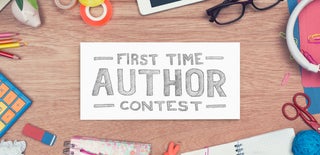
Participated in the
First Time Author Contest 2018