Introduction: Fiber Optic Pistol Sight
I recently acquired a Sccy CPX-2 pistol. I love it, but I was having a hard time finding the front sight quickly. After searching online, I found that there are very few options as far as replacement sights, and had read mixed reviews of the sights that are available. So, being a DIY type of guy, I decided to try my hand at modifying what I already had.
Step 1: Gather Supplies
This particular pistol has a pretty low profile front sight which is made of plastic. I knew it would be very cheap to replace if I didn't like how it turned out. Sights made out of other materials may be harder to modify (i.e. - steel, stainless, titanium, etc).
I had purchased a regular fiber optic cable (used for home entertainment systems) to use for a different project. I decided to use this as a "proof of concept".
Tools required:
Small drill bit (physical size of sight will limit this) - I used a bit that was ~1mm
Pin Drill vise
Hacksaw
Flat file
Masking tape
Lighter
Step 2: Drilling
As I mentioned earlier, metal sights will be harder to drill through by hand. This plastic sight is pretty easy to drill through. Before you start, you need to make sure that the drill bit you're planning on using is no bigger than the front face of the sight. If too large of a drill bit is used, it may compromise the integrity of the front of the sight.
The front sight originally has a small divot on the rear face (towards the back of the gun) that is painted white. I started by drilling a small indentation as close to the center of that divot. This indentation will keep the drill bit from wandering.
If you look at the profile of the sight, the rear face is not exactly perpendicular to the top of the sight. Therefore, if we were to drill a hole perpendicular to the rear face, the hole would go through the top of the slide, not through the front of the sight. THAT WOULD BE BAD!!! I needed to angle my bit so the hole stays parallel with the top of the sight and exited through the front face of the sight.
***NOTE: depending on what kind of pin drill you're using, you may want to partially wrap it in masking tape to keep it from scuffing the slide. I failed to do this and now have some small scuffs on the top of the slide (see last two photos).
Step 3: Fitting the Optic
Time to fit the optic. My first trial was using an audio cable fiber optic. I first cut the factory connector off of one end and then stripped off some insulation. For this application, less than 1/2" of optic is needed. This optic is easily cut with a razor blade, wire cutter, or a pair of good scissors. Once it was cut to length, I inserted into the hole in the sight. Using a lighter, I quickly heated each end of the optic which causes it to flare out, as well as smooths it to a polished finish. The flare will keep it from falling out of the sight.
The photos show this audio cable installed. It was very difficult to get a good photo of this. The performance of the optic was only so-so.
Step 4: Letting the Light In...
I started looking at fiber optic sights online again and noticed that all of them have a notch cut out of the top of the sight. This allows light to penetrate a larger surface area of the optic. Theoretically, the more light that comes in, the more light that goes out. My optic only had a very small surface area on the very end of the optic to gather light, in this case 0.785mm² (0.0012 in²). So, I decided to cut a notch out of the top of the sight.
First, I had to cut one of the flared ends off of the optic to remove it. Then I used a combination of multiple shallow cuts with a hacksaw and finished off with a flat file. I cut just to the bottom of the drilled hole, although I'm thinking I may eventually cut/file the notch a little bit deeper so the optic is completely suspended and light can enter from any point around the circumference.
At this point, the performance was a little better, but still not quite satisfactory. I think the problem is due to the audio cable optic being CLEAR. This optic will transmit any color that is in front of it. If you put something red in front of it, it shows red, if you put your hand in front of it, it shows flesh color, but worst of all black.....you guessed it, shows black. The optic basically disappears. I had to get a different optic, so back to the ol' interwebs I went.
Step 5: Fluorescent Fiber
I found a website (http://www.fiberopticproducts.com/flourescent) that sells fluorescent fiber in various diameters and colors. Since the hole I already had was 1 mm, I ordered one piece of green fiber for $5. It's sold by the meter, so I have plenty left over.
Installation is the same as before. Cut what you need, insert into the sight and singe the ends with a lighter.
The second photo shows the fiber glowing very brightly. This is because I hadn't cut a small section off of the 3' long strand. I had just inserted one end into the sight to get an idea of what it'd look like. I was pretty disappointed when I cut the excess off because it no longer glowed like that. I was kind of bummed out actually and started to look at other options. I decided that it was good enough for the time being, as it was still brighter than the white paint.
A couple days later, I went to the range and was surprised at how well the sight worked. The natural sunlight (even being in the shade) lit up the sight much better than the CFL lighting in my house. This is still not even in the realms of night sights, but it definitely helps. I did find a site that sells individual Tritium vials for ~$8 each. They come in 1.5 mm diameter x 6 mm long. I think there is enough material left in this sight to drill the hole .5 mm larger, but for now I'm going to use this for a while.
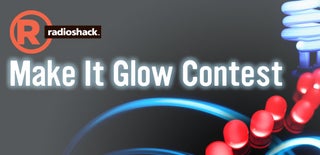
Participated in the
Make It Glow Contest
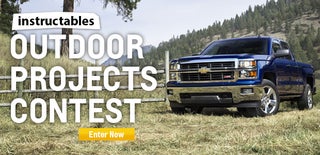
Participated in the
Instructables Outdoor Projects Contest