Introduction: Fifth Element Stones
Time to save the world... Well in this case with a little light!
Not that is matters but is is kind of funny to see these colours mimicked in the windows and android start up sequences. You just can't beat well written and quality Science Fiction!
First, each individual stone was slightly scaled down from the movie version to save space on my shelf. I am working on two individual projects in tandem on this one. There is a full size stone being made in conjunction with the smaller ones. I have scaled the measurements up to an 11 inch tall model that has dedicated sensor and software control.
I will focus on the smaller size but will continue to try to confuse you with the large size dimensions.Shown here are the smaller stones with fixed light columns!
small stones do not have movable side sections that extend before lighting.
I wanted these to light up as the movie versions so basic LED circuitry is needed.I chose to make a frosted acrylic column for maximum effect.
Step 1: The Templates and Forms
I have included drawings of the stones but these were uses for reference only and all work was performed using basic hand tools, a table saw and locally available materials.
I chose to make these from Hydrocal. After all they are stones so why not make them from "stone"
Each stone is a trapezoidal prism and by definition has 6 external sides, I call them the long side, the two short sides and the shortest side. This leaves two ends which are left open and called the narrowest sides.
Each small stone height is 8.5 inches, the long side is 3.5 inches, the short sides are 2 3/4 inches and the shortest side is a half an inch. Scaling up the height is 11 inches, the long side is 5 inches, the short sides are 3.9 inches and the shortest side is 3/4 of an inch.
I switch frequently between decimal and fraction. This was just the way I learned construction. If you have trouble finding decimal to fraction on your ruler, try using a digital micrometer gauge for proper sizing.
These are stones hand built with substandard tools so exact tolerances will not work. use a loose fit when making sliding or moving sections.
You will need a form to pour the Hydrocal into. To save time I made 4 for each size.
Several sections of MDF were cut at 8 1/2 inches wide and 11 inches wide
I cut an outline template from 1/2 inch MDF which is then used to set the table saw cutting angle. One end of an 8 1/2 inch section and the 11 inch section of MDF is cut with a bevel then the board is flipped over and another cut is made which creates the short side of the MDF to be 3 1/2 inches for the 8.5 and 5 for the 11. this is repeated 3 more times for each.
This process is then repeated another 8 times with a width of 2 7/8 on the wide side of the 8.5 profile and another 8 for the large size 11 inch at 4.62.
You will also need 4 more sections that are 1 3/4 inches on the wide side of the 8.5 profile and 4 at 1.8 of the 11 inch profile.
All these sections need to be primed and painted on the short side of the 3.5 X 8.5 and profile and 5 X 11 inch profiles and all of the long side of the profile for the remainder.
These will need to dry for 24 hours before assembly.
Attachments
Step 2: Details, the Inner Form and Pouring Hydrocal
The inner form is for the shade and electrics.
I will use time stamps from my video copy to help you along if you want to see the stones from the film.
The inner form is a triangle which runs through the entirety of the stone.
The long side form is 1.95 inches the two short sides are 1.8 inches for the 8.5 inch tall and 3.16 and 2.89 on the 11 inch profile
This is made from paper stock and is rigid yet flexible enough to be easily removed. This is fastened to a smooth base using hot glue. The inner forms are completely covered with packing tape to prevent moisture transfer.
Each outer form is taped together leaving the narrowest ends open.
This is then opened and placed flat painted side up. Each form is detailed with craft foam and hot glue. according to appropriate stone details as described below and shown in the pictures.
I don't fully trust the internet so I chose to watch the movie again on VHS and paused or took screenshots when necessary of the stones as they appeared. In the beginning sequences,9:20ish, Mondoshawans have thick hands so the opening sequences albeit educational do not provide dimensional reference, but B.W. appears to be of average man build so I used myself as a model and came up with the ratios in the following steps from 1:52:39 onwards.
The identifier lines take up a little less than half of the stone side height, about the width of an average mans hand ( not that B.W. is average..;-)
All identifier lines appear to begin and terminate at the center or base line of one full sine wave oscillation. The short sides terminate early and the shortest side is left bare. All lines appear to terminate about 3/4 of an inch from the shortest side on the two short sides.
Ignoring the inaccuracies and obvious prop changes from 1:52:40 through 1:53:15 the following appears to hold true.
Wind has 6 sine oscillations in the sky at the long side which start from the left going downward then rising upward once before terminating on the right. from 1:55:14 the short sides show up then down sine propagation. Backtracking, at 1:52:40 you will see wind and water together. Further at 1:55:09 the extendable side pieces are shown, my scaled build for the large stone has this at 2.25 inches tall and 0.6 inches wide
At 1:53:32 it is shown the Fire has five sine oscillations on the long side which rise from below first going left then right in one full wave and 4 on the short sides which go right then left in one full wave, this is seen at 1:53:32 and again at 1:54:53
Water at 1:53:34 has six waves on the bottom which on the wide side first dip down then up in one cycle for the long side face oriented on the ground, on the short sides it goes from up to down propagating to the right .
Earth shows six flat lines, not at all like the globe of our experienced existence. these are also at the "ground" of the stone, OK they are flat all the way around as seen at 1:54:58!
The center form should be placed on a modeling clay base to allow for a 45 degree bevel from the center form to the outer. This would create a cap with the edge at the stone edge. again time limited so I will show a work around in the large stone sequences. The smaller ones do not need it.
Once you are satisfied with the details the forms are closed an then placed over the center form. this is aligned and fastened to the smooth base. the entire form is edge sealed
Once all the forms are in place. mix a slightly runny mixture of Hydrocal. This is slowly poured into the forms at the smallest flat to allow for pushing of air bubbles out of the mold then vibrated to remove any remaining air bubbles.
Hydrocal mixture is about 4 parts hydrocal to 1 part water.
I used 16 cups of hydrocal for the 8 cast stones shown here.
These need about a day to dry fully but can be removed from the form in a couple of hours.
Step 3: Finishing the Stones
The thin wall casting process left my stones with some voids, holes and imperfect edges.
I used a belt sander with an 80 grit to knock the big flaws down and hand sanded the rest. Just lightly to take off the sharp edges.
These should be sealed with a clear coat but the weather in Calgary is being difficult and the shop heater is broken.
I left the casting voids as this will be corrected in future redoes of this process.
Step 4: Making the Shades
The shades are frosted acrylic from the plastic shop scrap bin, cut with a chop saw and formed with 45 degree angles. These should have been 31.5 ish, again not precision but hand construction rarely is. Lit up they do look AMAZING!
The shades are cut to fit the inner hollow of the cast stones.
Largest is 2 inches wide by 5 inches long.
Small sides are 1.3/4 by 5 inches.
Yes I know that MEK is the best acrylic adhesive but I used what I had after hours.
Cyano Glued together in a prism shape and topped with an acrylic triangle. these make a shade that lights up with the LEDs. the texture of the frosted surface really diffuses the light and make a great glow.
There is significant edge chipping from the cutting process since I didn't have a blade for acrylic. The end result is a perfect mix of a hand built ancient mystical look.
Cutting this way is extremely loud! Days layer and I can still hear it in my head.
Step 5: Wind Blows
Wind is yellow. Making the acrylic glow yellow is from amber LED.
For all the small stones, the shade is friction fit at the top and the LED's are at the base. I used 10 ultrabright LEDs for each stone. The simplest circuits are the best. power in series with a 110 ohm 1/4 watt resistor connected to 10 parallel amber LEDs. Initially I was using a battery but changed to a power brick from a LED strip light kit.
Step 6: Fire Burns
RED. I love RED. Looks wrong in the pics but I assure you this is red for the fire stone!
Again this is 10 ultrabright 5mm LEDs wired as before. The camera seems to pick up pure red in the odd burgundy (not Ron) tint shown here. Plus red LEDs really mess with the camera auto focus.
Step 7: Rain Falls
Rain, and water. these are typically blue, water stone!
Blue LEDs are different to work with. For some reason I was able to power all the stones from a single power supply until I tried to connect the blue. every time it would shut off the other sets of LEDs. no amount of fiddling would allow them to play nice together.
I finally got the power circuit to work by isolating each leg red, green, yellow, blue.
I stand by my hatred of these wretched little demon lights. This stone looks awesome none the less!
Step 8: Earth... Well It Is Not Mentioned in the Movie
Earth. Green is the only way to go with this one!
Green has always been my favorite colour LED, As a wee toddler I was used to seeing red lights on all electronics so when I first saw green I knew I had to have it. I made my very first LED circuit using a green LED from a broken tape deck.
This circuit uses 10 ultrabright green LEDs in parallel.
Step 9: Stone Colour
I initially thought of painting the stones but in the end I just went with the natural colour.
The big stones require some more work and will be addressed shortly
Step 10: It's Spring Cleaning Time
If you made it this far, I have something special for you... Since I love to share the things that I make...
I will be actively selecting and sending one of each of these 4 stones to who ever PM's me with a legitimate request. Just to be clear, no one will get them all, I'm looking for distance from Calgary but I will not say no to ingenuity, all 4 will be sent. I will update this page with your user name and stone once it is sent. This will be not be an entirely random thing and definitely not a first come first sent. I want to have these scattered Feb 29 2016. Do not ask specifically for a stone, try to convince me of your element.
Get creative with you request! I will cover standard shipping for this unique hand made gift. I' m thinking these stones should travel and I would love to see pictures posted here of them from the 4 corners.
Any private information sent to me will not be shared under any circumstances and no! I do not drive a white van!
I am currently actively seeking a new and rewarding career. If you are able to help me in this endeavor, I will personally put the set 4 large size stones on your desk possibly with a case for transport.
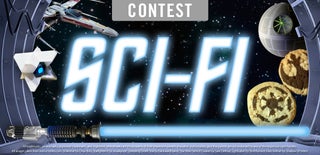
Participated in the
Sci-Fi Contest
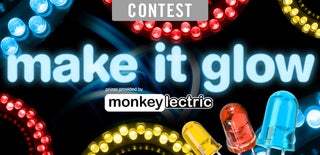
Participated in the
Make It Glow! Contest
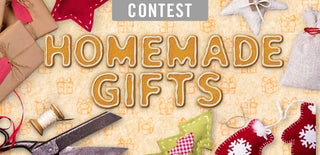
Participated in the
Homemade Gifts Contest 2015