Introduction: Five Cylinder Wobbler Steam Engine
I guess I just could have just made one of the existing designs for the "hula" engine, but I went ahead an designed my own.
If for no other reason, this just shows that there's more than one way to design the same outcome.
So if anyone says something is the "wrong way", well screw them.I hope you enjoy the plans.
After building the engine it really wasn't that difficult and could be a candidate for a somewhat experienced shop class or learning experience.
You'll need a metal lathe, milling machine, rotary table, etc. You need a decently equipped metal shop to make this toy. It's fun to watch it run though.
Enjoy the build...
Step 1: Drawing and Models
Here's the design drawings and step models of the engine...
Attachments
Arm, Frame.pdf
Assy - Crank.pdf
Assy - Crank Plate.pdf
Assy - Cylinder.pdf
Assy - Engine.pdf
Assy - Frame.pdf
Assy - Piston.pdf
Assy - Piston, Master.pdf
Base Plate-1.pdf
Con Rod.pdf
Con Rod, Master.pdf
Crank.pdf
Crank Plate.pdf
Crank Shaft.pdf
Cylinder.pdf
Engine - Step File.zip
Flywheel.pdf
Hub.pdf
Piston.pdf
Post.pdf
Shaft, Cylinder Wobble.pdf
Step 2: Hub - Part 1
I had already made a few parts prior to taking pictures, so I cannot talk about those.
They are bars with holes drilled in them anyways, so those are pretty easy.
Otherwise I started with the main hub. This is probably the most complex part to make. Because I used barstock of the correct OD to start with, I chucked the blank into the four jaw lathe chuck and centered the part. Three jaws are never perfectly centered I can be more accurate with the four jaw. Then I faced off the blank. From there I drilled and bored out the part.
Step 3: Hub - Part 2
After turning down to the correct width, I chucked the part into the mill on my rotary table where I would continue with the most difficult portion of this part - the pockets.
I didn't want to make one massive frame where one screw up can ruin hours if not days or work, so I designed the frame as a bolted assembly. As an industrial machine designer, I use the same philosophy in my designs for work. I prefer multiple simple parts over one excessively complex part.
I did find in machining the pockets it was best to cut the pocket about 0.005" undersized then make one, final climb cut to size. The finish was much better than my first pocket where I used a different technique.
Step 4: Crankshaft 1
It started as a piece of 1-1/2" dia. leaded steel.
I turned it down to 1.44 per the print then drilled/reamed out the center. The crank plate is only 3/8" wide and I didn't want to make a slug 3-4 times longer than the part where I generate a lot of swarf & scrap. So I use the full 12" long bar and supported it with a live center. Then I cut it off with a bandsaw, flipped the part, and turned the part to the correct width.
Step 5: Crankshaft 2
Next was taking the plate to the mill. I used the rotary table to hold the part.I drilled the hole for the shoulder bolt mounting threads. Then I did something I've never done before.I drilled 3/8" holes for the cutout corner. Using those two holes with pins temporarily installed I clamped the part into the vise with a parallel underneath to create a gap. I could then mill out the rest by eye.
Step 6: Base Plate
Considering I wasn't really ready for the frustration of starting the cylinders, I continued on with the engine base of post. I purchased a piece of 1/2" cast aluminum plate, 8 inches square. I wanted it round.
So I drilled a 3/8" holes in the "center" of the plate and an offset 1/4" hole to act as a lathe dog.
Then I took an old piece of A36 steel bar to create a mandrel to mount the plate.
Upon mounting the plate to the mandrel, it was a long process of interrupted cuts to make a round plate. The print shows a final dimension of 6.00" There's no penalty to a larger plate, so in reality my final dimension was 7-1/2 inches.
Step 7: Post
The post is fairly simple and the photos should be self explanatory...
Step 8: The Flywheel
The cast iron casting from PM Research was a bit more flimsy than I was expecting. Normally I'll machine one side of the bore, the OD, and the OD face in the same setup.
When I tried that here, I got excessive chatter on the OD face. So I needed to flip the jaws in my chuck to machine the OD face and still get an acceptable finish.
Step 9: Pistons
Because I need to make five of pistons, the first one was a prototype to figure out how to make them efficiently
I learned two things:
- Deviate from the design and drill/ream the piston all the way through. Add .125 inch to the piston rod and press the two together. The lengths are much more accurate.
- Cross drill/ream and thin down the piston rod after pressing it onto the piston. The press fit is so tight that having those details machined prior to the press fit will smash the cross drilled hole.
Step 10: Cylinder - 1
Onto the cylinder. As with the piston, I only did one to figure out the technique. I made the other four after getting the technique correct.
After cutting the block to size, I drilled/reamed the cylinder bore (.625").
Step 11: Cylinder 2
Flipping the block, I drilled, reamed, and cut the ports, pivot, and reliefs...
Step 12: Cylinder 3
Finally the last part:
Cut the pivot pin.
Thread the pivot pin.
Press the pin into the block.
Cross drilled the pressed assembly and inserted a dowel pin to hold the thing together.
Testing for fit, I needed to turn the piston down a little bit, other than that today went pretty good...
Step 13: Put It Together and Watch It Run!!!
In the end I didn't really modify far from my original plans.
I believe if one followed the plans explicitly, they would have a running engine.
This wasn't a super hard engine and would be a good project for someone that's done a couple of single piston steam engines.
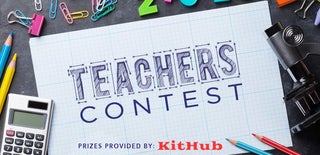
Participated in the
Teachers Contest 2017