Introduction: Flexible Pegboard - Hook System
Upgrade the your traditional pegboard with this flexible solution. The hooks can be bent to match your specific needs. Easily switch out hooks via the modular plug design. This pegboard actually uses pegs. You can BEND THE HOOKS to fit what you need. Don't be limited by the prefab hooks found at the hardware store!
Step 1: Diagram and Animation
Name that tune anyone?
Step 2: What You Need.
Materials Needed:
3/8" hardwood dowel
A solid board at least 3/4" thick.
Wire - fairly stiff. Suggest 12 to 10 guage.
Beads for capping the wire ends
Fast setting epoxy. Or slow if you like to wait.
Tools Needed:
Saw
Drill
Wire cutters
Step 3: Make the Pegboard
Typical "pegboard" employs wire hooks. In contrast, this design uses modular wooden "pegs" not just bare wire hooks. I've demonstrated with a simple foot long 1x2" board. This example looks much like a key hook. The concept can be easily applied to a wall or larger board(s).
Dimensions of this board are: 0.75"x1.50"x12.00"
The receiving pegholes are 3/8" diameter. As you would easily guess, I'm using matching 3/8" dowels for the pegs.
In some of the pictures, you can see two versions of the same foot long board.
The first has holes in the top only (drilled straight down).
The second is the same plus it has holes drilled at 45 degree angle on the face.
I drilled the holes approximately 1" deep. This enables the pegs to seat completely flush if desired.
Cutting angled pegs will allow for front mounted pegs to also be flush.
Step 4: Making Pegs (peg Hooks)
The pegs shown are 3/8" oak dowel rod diced up into 3/4" long pieces.
I do suggest a hardwood variety for the pegs.
I cut the pegs with traditional 90 degree cut.
Also, I cut pegs with parallel 45 degree cuts. Looks a bit like asian cuisine.
Then, I drilled holes longways down the centers of the pegs.
These pegs are a bit tricky to hold still.
For safety, I suggest holding the pegs with pliers as you are drilling.
Alternatively, you could make a quick wooden jig for drilling your pegs.
Just grab a scrap of wood and drill 3/8" holes about 1/2" deep.
The holes you drill should be just large enough to receive the wire that you will be using as a hook.
I found bits in the 3/32" to 1/8" worked well. I cut most of the wire to lengths around 4-5 inches.
I mounted the wires into the pegs with epoxy - but superglue seems to work fine also..
Then, to finish the hook ends, I epoxied beads onto the ends of the hooks. You may need to ream out the beads to fit the wire. It's not mandatory to cap the ends, but I liked the look and feel of them. If you do not cap the, I would suggest smoothing them a bit.
Step 5: Bend the Wires and Hang Some Stuff.
On this one, I also put some rubber hose over the wire. This cool blue hose is used with fish tanks. You can bend the wires with just bare hands. Consider using dowels or pipes as bending jigs to get nice smooth curves. If using pliers - pay attention to denting and scratching of wires. Avoid scratching/denting by padding plier jaws or by using special round nose pliers often used for jewelry making. Those special pliers can be really handy.
REMINDER: You can use this design on boards of many shapes and sizes. Don't limit yourself to just this little example. I plan to make a larger size model of perhaps 4 foot square (and of course have a ton of pegs ready for use).
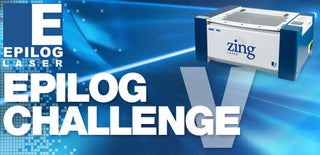
Participated in the
Epilog Challenge V