Introduction: Floating Pinion Demonstrator 2
Floating Pinion Demonstrator 2 is an updated Autodesk Fusion 360 design of my original Floating Pinion Demonstrator design of around 3 years ago. With this update, and the PLA Spring Motor Demonstrator 2 update, I'll finish with an updated model that was very popular with our kids, grandkids, nieces and nephews.
The original Floating Pinion Demonstrator was designed as yet another "proof of concept" tool (I do this quite often) to test whether a 3D printed PLA floating pinion would successfully engage (under spring energy) and disengage (after spring energy is depleted) a 3D printed PLA spring motor from a 3D printed drive train (in this model, simply a drive wheel) in order to allow coasting after the spring energy was depleted. As a result of that successful test, I was able to design a number of 3D printed floating pinion PLA spring powered vehicles.
Like PLA Spring Motor Demonstrator 2, Floating Pinion Demonstrator 2 is a fairly easy print and assembly, and even though it was originally designed as a proof of concept tool, it is still a fun desktop conversation piece. Please note that the drive wheel in this design is unloaded, and as such the spring energy is depleted quite rapidly, so maintain a firm grip on the model or mount the model in a vice or other suitable rigid holding fixture before operation.
As usual, I probably forgot a file or two or who knows what else, so if you have any questions, please do not hesitate to point them out as I do make mistakes in plenty.
Designed using Autodesk Fusion 360, sliced using Cura 3.5.0, and printed in PLA and Tough PLA on an Ultimaker 2+ Extended and an Ultimaker 3 Extended.
Step 1: Print and Prepare the Parts.
I printed the following parts at .15mm layer height:
- Six "Bolt, Frame.stl", 100% infill, Magenta PLA.
- One "Frame, Left.stl", 50% infill, Black Tough PLA.
- One "Frame, Right.stl", 50% infill, Black Tough PLA.
- One "Gear, Floating.stl", 100% infill, Magenta PLA.
- One "Gear, Idler (50, 1.12).stl", 20% infill, Magenta PLA.
- One "Gear, Pawl (50, 1.12).stl", 20% infill, Magenta PLA.
- One "Guide, Gear, Floating.stl", 100% infill, Black Tough PLA.
- One "Knob and Axle.stl", 100% infill, Magenta PLA.
- One "Nut, Gear, Floating.stl", 20% infill, Magenta PLA.
- One "Pawl.stl", 100% infill, Black Tough PLA.
- One "Spring.stl", 100% infill, Black Tough PLA.
- Two "Wrench.stl", 20% infill, Magenta PLA.
Prior to assembly, I test fit and trimmed, filed, sanded, etc. all parts as necessary for smooth movement of moving surfaces, and tight fit for non moving surfaces. If you decide to make your own Floating Pinion Demonstrator 2, depending on the colors you chose, your printer model and your printer settings, more or less trimming, filing and/or sanding may be required. I carefully filed all edges that contacted the build plate to make absolutely certain that all build plate "ooze" was removed and that all edges were smooth. I used small jewelers files and plenty of patience to perform this step. I also used 6mm by 1 right hand threaded taps and dies to prepare the threaded parts prior to assembly.
Attachments
Step 2: Assemble the Floating Pinion and Guide.
I assembled the floating pinion and guide as follows:
- Positioned "Gear, Floating.stl" into "Guide, Gear, Floating.stl".
- Secured "Gear, Floating.stl" in "Guide, Gear, Floating.stl" using "Nut, Gear, Floating.stl".
- Once secured, I insured that "Gear, Floating.stl" moved easily throughout the slot in "Guide, Gear, Floating.stl", then applied a small dot of thick cyanoacrylate glue to secure "Nut, Gear, Floating.stl" to "Gear, Floating.stl".
Step 3: Assemble the PLA Spring Motor.
To assemble the PLA spring motor, I performed the following steps:
- Attached the floating pinion assembly to "Frame, Right.stl" using two "Bolt, Frame.stl".
- Placed "Knob and Axle.stl" into "Frame, Right.stl".
- Pressed "Spring.stl" onto "Knob and Axle.stl" while placing the spring retainer over the axle on "Frame, Right.stl".
- Pressed "Pawl.stl" onto "Knob and Axle.stl".
- Placed "Gear, Pawl.stl" onto "Pawl.stl".
- Placed "Gear, Idler (50, 1.12).stl" onto the axle on "Frame, Right.stl".
- Placed "Frame, Left.stl" onto the spring motor assembly.
- Secured "Frame, Left.stl" to the spring motor assembly using two "Bolt, Frame.stl".
Step 4: Final Assembly.
For the final assembly, I performed the following steps:
Secured one "Wrench.stl" onto "Frame, Left.stl" using double sided tape.
Installed two "Bolt, Frame.stl" into "Frame, Right.stl".
Secured the remaining "Wrench.stl" onto "Frame, Right.stl" using double sided tape.
And that is how I printed and assembled Floating Pinion Demonstrator 2.
Hope you enjoy it!
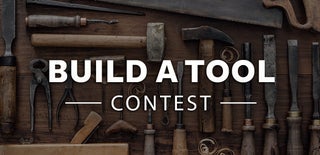
Participated in the
Build a Tool Contest