Introduction: Fold Down Hanger for Coats, Cords, Etc.
As, hopefully, can be seen in the pictures, these are individual racks that fold down for use and up out of the way when not in use.
These can be made to hold heavy cords and cables, or just for coats and clothing. You can adjust the size to accommodate the use to which you put them. Just adjust the measurements, as the steps indicate, and you can enlarge or reduce their size and capacity.
[MATERIALS]
You'll need the following materials to build this project:
1) Solid wood
or
1) Plywood
NOTE: The ones shown are constructed from 3/4" plywood. The thickness of the wood or plywood used is dictated by what the hanger will be called on to support. Generally, I'd not use less than 3/8" thick stock for coat racks to insure adequate strength. As well, thicker material may be easier to work with, when installing the dowel.
2) 3/8" - 1/2" dowel.
NOTE: For heavier loads, I'd use at least a 1/2" dowel, which should be adequate for most applications. For example, I have an 8 gauge, 80' long power cord I would be comfortable hanging on one of these using only a 1/2" dowel, since the dowel in my hangers are 2-1/4" long and 1-1/2" of that is supported by the hanger sides, leaving only 3/4" of the dowel to do the heavy lifting.
3) Sandpaper
NOTE: 150 grit will, probably, be sufficient for most sanding needs. If the cuts were very course, you may need to start out at a lower grit.
4) Glue (regular carpenters glue will be adequate)
[TOOLS NEEDED]
You'll need the following tools to build this project:
1) For the straight cuts, you can use a circular, jig, band or table saw.
2) For the curved cuts, you can use a coping, band or jig saw.
3) For the pivot dowel and mounting screws, you can use an electric hand drill, a brace and bit, or a drill press.
4) To hold the pieces together while the glue hardens, you can use clamps or just can lay weight on the pieces, until the glue sets (keep the pieces aligned to minimize sanding).
5) The sanding equipment you require depends on the quality of your cuts and how well you aligned the pieces during glue up.
If you cut the three pieces with a table saw or otherwise ended up with consistent and straight cuts, and if you kept the pieces aligned during glue up, you may only have to fold a piece of sand paper over and smooth up the ends and edges.
If the assembled hanger is rough, you may need to use a sanding block or a electric pad sander. Of course, if you have it, a belt, drum or edge sander would make short work of bringing the three glued surfaces flat to each other and of truing up the other straight edges.
The grit of sandpaper you need depends on the roughness of your assembled hanger, or on how even the surfaces of the three pieces are to each other. For example, if the center piece is proud (raises above) the others significantly, a 40 grit will bring the three to the same level quickly. Once sanded so all pieces are straight and even, go to 80 or 100 grit, then 150 is good enough for a poly or paint finish.
NOTE: You may find it easier to lay the sheet of sandpaper on a flat surface and run the back of the assembled unit over the paper.
Step 1: Layout and Cutting the Hanger
The following directions are for a hanger similar in size to the examples seen in the pictures:
[HANGER HOUSING/BODY]
1) Cut the two sides 3-1/2" wide by 7" long. You may find it easier and safer to cut a piece about 14-1/4" long, then cut the two 7" pieces from it.
2) Cut the spacer, which will join (be sandwiched by) the two sides, 3/4" wide x 7" long. If you are using 3/4" plywood, this would give you a 3/4" by 3/4" piece.
3) Cut the flip-up/down hanger 2-3/4" (the 3-1/2 sides minus the 3/4" thick spacer) x 7" (the length of the hanger).
NOTE: It is critical the width of this piece be equal to the depth of the gap between the two sides, because the bottom will serve as a stop, when the hanger is flipped down.
4) Glue and clamp the two sides and spacer together. The middle spacer should be flush with the backs, tops and bottoms of both sides.
If there is any glue squeeze out on the inside, use a screw driver and damp cloth to remove all the glue. Of course, you can also wipe off any excess on the outside of the rack housing.
5) Once the glue holding the sides and spacer together has set, sand the back, top and side each is flush with the other pieces and smooth.
[FLIP DOWN PORTION OF HANGER]
6) Draw a circle on one end of the flip-down hanger with a diameter exactly equal to the depth between the two sides. In this example, 2-3/4". This will set up the pivot for swinging the hanger up or down.
If you draw the circle with a template, use the lines to mark center, for later use, when drilling the pivot dowel. If you used a compass, the needle will provide center.
NOTE: Making the circle the same dimension as the width of the hanger piece and cutting away the bottom left, as seen in the picture, allows the hanger to clear the back and pivot.
As seen in the picture, DO NOT cut the bottom right. This part serves as the stop when the hanger is flipped down. This has the added advantage of making the hanger look more like a single piece, when the hanger is flipped up.
Though the ones I built and in the drawing have inside of the lower (larger) circle rounded, not rounding this might look better, since it would leave this part of the hanger square and flush with the housing, when the hanger is open. Of course, you can round that part, like mine, if desired.
7) If you did not mark its center when drawing the larger circle, you can find it by using an L-square to run a line across the top of the circle, which should give you a perfectly square box. Once you have that, you need only draw an X, with the lines from corner to corner.
8) Draw a second circle, approximately 1-1/2" in diameter, on the opposite end of the flip-down hanger This circle will touch two edges ninety degrees from each other (the top of the hanger in the picture. This will be the part on which a coat or other item hangs. Its dimensions are not as critical as those of the larger, bottom circle.
9) Draw a line between the two circles about 1-1/4" in from and parallel to the edge both circles are touching. This 1-1/4" thick measurement should leave the hanger strong enough to handle all but the most taxing uses.
10) Using approximately a 1-1/2" circle, draw part of a circle to join the smaller circle to the line just drawn. This is both for aesthetics and to leave a smooth surface, so things pulled off the hanger will not be snagged.
11) Cut the flip down hanger out and sand all edges smooth to preference.
12) Mark one side of the hanger housing for drilling the pivot hole. There are several ways to do this. For example:
You can place the flip down portion of the hanger on a side of the housing with the bottom of the large circle and the long flat edge aligned flush with the outer and bottom edge of the housing (just like it will install between the two sides), secure it, then drill a hole the same size as the dowel you’ll use.
or
You can measure the radius of the larger circle, then mark this distance [from the edge of the circle to its center] from the bottom and outer edge of the housing. Then, with the flip down piece installed, again with all edges flush, and secured, drill the dowel hole through the three pieces.
NOTE: Try to keep the hole at a perfect ninety to the surface. A drill press would be ideal for this, but it can be done with careful use of a hand drill.
13) Once you have drilled the dowel hole, cut your dowel to a length equal to the width of the housing, or just a little longer than needed (it can be trimmed off and sanded when done installing it).
14) Use a toothpick to apply a minimal amount of glue to the dowel hole on the opposite side you’ll be starting the dowel from (this will avoid pushing glue where you don’t want it). Then pound all but about 1/4" of the dowel through the unglued side, through the center hanger and into the other side.
Add just a little glue to the 1/4" you didn’t pound through, then finish pounding the dowel flush with the side.
Remember, too much glue could cause the flip down part to stick to the body, or could lock the dowel to both the flip down part of the hanger and the body, rendering the hanger inoperative.
15) Once the glue is dry, chisel, cut or sand any part of the dowel extending above the surface of the side so both sides are flat.
Step 2: FINISHING
Apply any finish you desire, if any, to the hanger.
Remember not to allow the finish to flow between the flip down part of the hanger and the body or it will act like a glue, when dry.
Step 3: ALTERING THE DIMENSIONS FOR LARGER HANGERS
If you wish to make the hanger larger, such as for holding hoses or cords, you merely have to alter the length and width of the hanger.
Making the hanger longer (taller) will result in a flip down hanger which reaches out farther, so it can hold more.
Making the hanger wider allows you to thicken the hanger so it has the strength to hold heavier loads.
As with the example, the diameter of the pivoting circle, at the bottom, must be the same as the depth between the two sides so the stop will work when the hanger is flipped down.
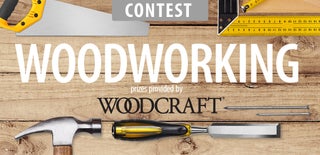
Participated in the
Woodworking Contest 2017