Introduction: Foldable Saw Horse
I have a set of folding saw horses made of plastic that have been very useful to me over the years. I particularly like the way they hang beside my storage shed, saving on valuable back yard space when not in use. Unfortunately one of them has finally failed, as have my repeated attempts at fixing it, so I decided to build a replacement.
Using scrap wood and leftover hardware I devised this simple design based on dimensions I got from the remaining good sawhorse. I wanted it to be light enough and of course storable.
Supplies
Cut list:
4 @ 29.5" x 2.75" x 1.5" legs with 15 degree cut on one end, made from a single ripped in half 2 x 6 board
4 @ 26.5" x 2 3/8" x 3/4" cross members cut from 1x6 material (in my case ash because it was all I had}
2 @ 29.5" x 2 3/8" x 3/4" top rails cut from 1x6 material (ash) with 15 degree angle ripped on one edge
1 @ 26.5" x 3"+ x 3/4" keystone shaped top insert ripped at 15 degrees to a 1"(or so) top dimension. This piece could also be cut to 29.5" if preferred.
2 @ 6.5" x 21" x 3/8"(or whatever thickness you have) plywood for folding section with 15 degree rip on one long edge of each piece.
Supplies:
1.25" or 1.5" inch screws 2" screws for top pieces
3/4" screws for hinges (or whatever will work). Longer screws can be ground flush later.
7 small hinges (2-3" long?) or a few piano hinges if you have them.
4 large door hinges or other larger type that are wide enough to screw into cross members.
Tools: skill saw or chop saw, table saw, grinder, bevel gauge, speed square, hand drill, pencil, countersink bit, screw tip bits, chisel.
Step 1: Rip 2x6 in Two and Cut Legs.
For the legs I ripped down an 8ft (I think) piece of redwood 2x6 (since it was the only 2by material I had), into two lengths of 2 3/4" x 1 1/2" from which I got 4 legs at 29.5"--a number I got simply by measuring the existing folding horse. Though I didn't personally do this until later, it is best to cut one tip of each leg end at 15 degrees now to provide angled feet that will make the opened horse the right height (for one thing). Using a chop saw for this is ideal, though I got the angle close enough with just my skill-saw. I figured out the angle by setting my bevel gauge on top of the plastic saw horse, transferring that to a plywood edge and using my speed square's pivot point on the line to give me 15 degrees.
Step 2: Cut Cross Members and Top Rails.
I ripped my 1x6 ash stock down to 2 3/8".
Next I cut the 2 3/8" material into these lengths:
4 @ 26 1/2" -(cross members)
2 @ 291/2" -(top rails)
1 @ 26 1/2" -top keystone shaped insert--(this could actually be 29.5" too. For some unknown reason I decided to leave the overhangs "empty"--if that makes sense).
I ripped one long edge of each 29 1/2" piece at 15 degrees, using my bevel gauge to set the table saw blade.
Then I marked a line 1.5" from the ends of the two 29.5" top rails, representing the overhangs.
Finally I ripped the two 15 degrees edges of the top "keystone" insert piece ( 26.5"--but on retrospect this could be 29.5" too), using a length of 1by to determine the top thickness (I hope that made sense). I later realized the piece could be made out of 2by or even thicker wood, which would be stronger.
Step 3: Mark and Cut Slots for Cross Members
I think this is called a basic lap joint, where the 1by's are inset into the 2by's. I just used a cross member piece to determine the correct width (2 3/8"). Then marked the un-beveled tops and middle shelf position at 15" from the bottom (beveled edge) of the legs, to the shelf's top edge. To cut the slots I set my skill saw blade to the 1by stock thickness and cut a series of passes to my marks, which I cleaned out with a chisel.
Step 4: Attach Cross Members
I used a countersink bit to pre drill screw holes in the cross members, which I attached using 1 1/4" screws--though one could also use 1 1/2" or even 1" screws. Though I didn't have any, it would also be ideal to apply some wood glue here for extra strength.
Step 5: Attach Top Rails
I attached the top rails using recycled hinges and 3/4" screws, making sure to align the over hang mark to the top edge.
Step 6: Attach Keystone Insert
This is a little awkward to do because of the angles, and it is best to use glue. I had to reposition my holes lower down later, to assure they were more centered on the insert. I didn't initially cut a bevel on top rail edges, opting instead to plane them down (really not the best idea). Sorry about the lack of pictures here. I just couldn't hold the camera while doing it. At this point I had a standing saw horse with no folding shelf.
In the pictures you can see I attached each side with counter sinked screws on the inside, which I thought looked better. This also proved to be important later wtih door hinge placement, since the now inset cross members would prevent accidental removal of pins.
Step 7: Cut Shelf Pieces and Join With Hinges
I cut two halves of the folding shelf after measuring a 13" gap between extended legs, beveling the outside edges of the 6.5" by 21" pieces to provide proper sitting of the door hinges later. I joined the two halves with three small hinges and planed outer angles (but should have cut them on the table saw instead). Since the only screws I could find were too long I ground down their protruding tips. I also drilled a one inch finger hole centered at 2.5" from each outer edge, as on the plastic saw horse.
Step 8: Attach Shelf With Door Hinges.
Here I used four old door hinges to attach the folding shelf to middle cross members. I placed them close to the legs in such a way that their hinge pins could not come out all the way. After that I planed the top Bevel down flat--though if you pre cut them you wouldn't have to do this, and Voila! A folding horse that can hang beside the storage shed.
I think I'll make another one too. This one feels a lot more solid than the plastic one.
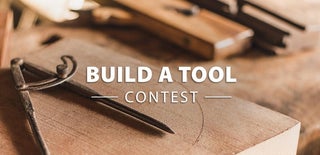
Participated in the
Build a Tool Contest