Introduction: Spiral Fountain
I made this spiral fountain using a mig welder. What gave me the idea to make a spiral was a laminate metal electric motor coil that I found at the dump. I think it is from a washer or dryer, but I'm not sure. I also used pieces of metal rod I had accumulated from taking apart old printers and other junk items.
The project became improvised after I decided not to use it as a table bottom, which I had intended to enter in the furniture contest. It became a bit involved with all the welding but wasn't too hard to complete after patient persistence. It's a pretty cool project for someone who likes working with recycled metal. I'm sure there are better ways to make a spiral, but this is how I did it.
Supplies
Here is a list of materials:
1 small fountain pump
1 used 10 inch circular saw blade
1 salvaged metal dome cover from an old iMac computer
1 winding nob thingy from an old arc welder
1 1/4" thick piece of pencil rod about 4 feet long
2 approximately 2' lengths of metal rod about 1/4" thick
1 unwound piece of electric motor laminate
Several salvaged sheet metal computer tower casing pieces
1 salvaged spring from an old timer switch (?)
1/4 bucket of ShapeCrete sculpturing concrete
Primer, house paint, Thomson's water seal, various art paints. epoxy glue, wood glue, super glue.
1 old planting pot.
1 handful of fake hand made nails.
1 approximately 3 ' long piece of 1/4" copper tubing.
1 small chrome plated bowl and a tubular metal piece for a spout.
Some tape (either duct tape, or masking tape)
Tools: Mig welder, "peanut" grinder with cut off wheels, bucket for mixing concrete, painting supplies, router, pliers, safety equipment (including welding mask).
Step 1: Unwind Motor Laminate Part.
This motor part has to be disassembled after cutting or grinding off the copper wiring (for selling to a scrap yard). It is pretty simple to do: Remove the plastic by hitting it with a hammer, then unwind the metal by prying it loose with a screwdriver or chisel.
Step 2: Wind Pencil Rod Into a Spiral.
I was lucky enough to have a fairly long piece of (what someone told me is pencil rod) that I found on a beach on the Carquinez Straits in Vallejo California. A bunch of these pieces were tangled up in seaweed on the rocks and I took some home. Another hiker said it used to be a high wire electrical conductor that was cut down and dropped into the water many years ago. You could use any stiff but bendable rod that's around 1/4" in diameter, and weld it together (if it's not long enough). I peeled off its fairly thick rubber coating before figuring out a way to bend it in a spiral with the help of an old compressor tank I had sitting around. The tank needed stripping down with a grinder first, which was pretty easy: Just cut off anything sticking out of the surface. I then used an existing hole on the tank to anchor a rod end while I slowly forced everything to roll on the ground until there was a rough spiral. I adjusted the circumference, which needed tightening, with my shop vise, while checking its curve next to the unwound laminate strip. After some judicious adjusting I had it pretty close and was ready to start welding.
Step 3: Weld Laminate Onto Spiral Rods
Here I needed to use vise grips to clamp the strip of laminate onto various points of the rod for spot welding. I tried to make the tabs uniformly stick out on the spiral. I kept going until it seemed like a good height and then cut off the laminate at each end. Some pieces broke off but this wasn't a problem since I could just weld another one on. I ended up with something a bit like the winding skeleton of a snake.
Step 4: Attach a Base to the Spiral.
I found couple of circular metal pieces that fit perfectly for a base to weld the spiral onto. One was from an old iMac computer I had scrapped a while ago, and another was winding nob plate (?) that came from a Lincoln arc welder. I welded the spiral first onto the i Mac base then added the other disc for more strength and weight. I also welded some 4" pieces of scrap rod onto the bottom spiral turn section to stiffen it up. I was initially planning to use those short re-enforcement rods all the way up, but changed my mind, opting instead to use only sheet metal, which was more than adequately stiff. I also later cut off the nob and bottom arm from that welder part, so nothing would obstruct the design or prevent it from standing flat on its base.
Step 5: Attach Center Pole and Adjust the Spiral
I cut a bunch of four inch long rods to help me with adjusting the spiral so it was at least fairly uniform. This was an imperfect process and I kind of made a mess with too many spot welds and later had to grind off the supports, which were superfluous and in the way. I discovered that each level should be about four inches high and four inches from the center pole. The center pole came from an old lamp and conveniently screwed onto a center hole on the base. I later filled it with cut off rod pieces since I wasn't going to feed any wire through it--making the column more solid for welding onto. I also welded it to the base so it couldn't come loose. In retrospect I probably should have used a thicker non hollow center pole, which would have been stiffer and easier to keep straight, but I did manage to rack any bent areas to an acceptable straightness . I found using an extra temporary screwed on arm on the top helped keep the spiral centered while later attaching sheet metal pieces.
Step 6: Cut Pie Shaped Sheet Metal Pieces With a Grinder.
I made a quick mock up with paper to determine the correct radius for pie shaped pieces and dug out some computer chassis sides from my scrap metal pile. Then using a cut-off wheel on my grinder I roughed out several circles of around 5 inches in diameter that I reduced into slices of sheet metal for attaching to the spiral. I used tin snips but preferred cutting with a peanut grinder since the computer sheet metal was fairly thick and hard to snip by hand. I think I used around five circles' worth of sheet metal to complete the piece, removing the tip of each pie slice so it would fit properly. I also ground off any jagged edges after cutting my fingers a few times while handling the slices.
Step 7: Weld Pie Pieces Onto Spiral.
I found a bunch of old fake hand made nails I had kept in one of my piles of recycled junk, whose wedge shape proved perfect for spacing the inner part of each weld, which needed to be slightly higher whenever attached to the center pole. Otherwise the inside kept creeping too low at each stage for some reason. This whole process took patience and was rather time consuming. Most of my welds were spot welds, and I just kept going up the spiral with pie pieces--whose tips were cut off to make them fit the frame. I had to be careful not to blow through the sheet metal, but didn't worry too much when I did. I would periodically turn the assembly on its side to weld underneath as well, occasionally patching accidental holes. If a part did not fit perfectly I could hammer it tighter and spot weld again too.
Step 8: Add Spring Steel Edge.
This part turned out great and was an accidental discovery. I had some unwound springs sitting around which I decided to use as an edge rail on the spiral. It turned out they fit perfectly and could be held in by the laminate spines that I turned over one by one over them. No welding was needed. It was a bit tedious but I managed with the help of slip joint and regular pliers. Vise grips also kept things in place as I went along. This edge effectively turned my spiral ramp into a miniature pan decking form for later placing of concrete. (It reminded me of the entrance ramp I helped build on a much larger scale at San Francisco's Pac Bell Park a number of years ago while working as a union carpenter).
Step 9: Build and Attach Saw Blade Assembly to the Base.
This was another improvised addition. I initially wanted to make a base that would be gentler on a whatever surface the spiral sculpture would rest on, so I decided to add wood. I also figured more weight and strength wouldn't hurt either, so I took an old damaged 10" circular saw blade from my collection and dug out an appropriately sized piece of pine shelving from my wood pile, that I routed out to house the blade so its teeth would not protrude. The blade had holes I used to screw attach to the wood, and I applied epoxy glue for added holding power. A round over bit on my laminate router made the wood edge fit better in the planting pot and I finally spot welded the saw blade edge onto the base.
Step 10: Prepare for Concrete Placement
Here I just patched any areas where the cement might leak through, using some white duct tape I had left over from another project. Any tape would probably do. Some pieces would later disappear under concrete and not require removing.
Step 11: Mix and Place the Concrete.
I followed directions for proper water to mix ratio for the Shapecrete, and began placing it in the ramp, after I had cleaned up the welds a bit with a grinder and wire brushed off any flux slag. I also used some latex primer I had acquired at the dump. It was easy to smooth and shape the concrete with my hands, and I tried to keep an even layer all the way up. I found it would hold well but flow thicker toward the center, which was more steep, and I had to work it a bit to get it to hold its shape. The sagging wasn't enough a problem to prevent gradually working my way up to the top. I used a torch to accelerate hardening of some problem areas. I also filled holes in the base dome with sand and extra concrete, which added some weight and prevented water from pooling inside it.
Step 12: Attach Copper Tube and Top Bowl.
I wound a copper tubing section up the center pole, and screwed in a chrome plated bowl I found in my junk pile to the top, bending the copper so it would spill water into the bowl. I then spot welded the bowl more securely, and added an improvised spout made from another piece of scrap metal. I welded the spout onto the bowl's side at conveniently placed cut out on its rim. I found it was necessary to make water flow onto the ramp properly. I also trimmed off excess length at the top and added a new support arm at the spiral's end, to hold the top firm.
Step 13: Find and Prepare a Planting Pot.
I found a pot in my back yard that just happened to be a perfect size and shape to hold the spiral assembly . I carefully drilled a hole using a masonry bit, about half way up the side, large enough to feed the pump's power cord through, and patched the drain hole so it would hold water. Then I painted the pot, and water proofed it with Thomson's water seal (another dump score).
Step 14: Remove the Tape and Paint
I removed any visible duct tape and applied primer to the spiral, using grey for the metal parts first, then white "bull's eye" primer for everything else. Then I used Benjamin Moore house paint, green oil base enamel, gold, and transparent stain glass paint. These were found again at the dump's re-use area. Masonry paint would probably be best for the concrete however and you could of course just leave it unpainted.
Step 15: Drill Drain Holes, Notch Edge for Pump Hose, and Attach Hose
I drilled a few holes for water return through the wooden base, and notched its edge to feed the copper pipe through, so it could attach to a flexible plastic hose that went to the pump. I also pushed several small sections of screen in the holes to filter out debris. I attached the hose with some recycled copper wire and super glue since I couldn't find a small enough hose clamp.
Step 16: Fill With Water and Plug In
I finally attached the pump hose, inserted the spiral into the pot and poured water in until it up to the plug hole. After plugging in I tipped the spiral until water flowed down evenly. It's obviously not a perfect spiral but it has character and works great as a water feature either in or outside the home.
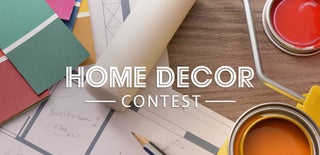
Participated in the
Home Decor Contest