Introduction: Forklift Blocking to Furniture: 3 Legged Stool
I just want a place to park it...
Hello, my name is Philip and I'm obsessed with chairs.
Now that we've got that out of the way, let me explain: a good chair is (insert your preferred "love it" adjective here). Comfort. Beauty. The End.
Let me tell you the amazing things this stool can help you with. You know how you have to put your socks and shoes on every day? Is your bed too high, the tub too uncomfortable, and the closet- well...a little tight? This stool can help you. Do you have to bathe children and are tired of kneeling on the floor? Check. Are you short and can't reach things on the top shelf? This stool's got your back. Do you play the guitar somewhere that isn't conducive to holding a guitar? Well, I think you know the answer.
So come on, let's build one!
Supplies
You need all the supplies for this one. Technically you could buy dowels and a circular piece of wood and only need a drill- this is a bit more involved. But if you want to you could simplify these steps.
You will need (in no particular order): Wood, Jointer, Planer, Tablesaw, Bandsaw, Pencil, Compass, Plastic or Hardboard for templates and "Go-no go" Jig, Lathe, Lathe tools, Handsaw, Sandpaper (all the sandpaper), Spray bottle of water, Glue, Clamps, Rubber bands, string, center punch/awl, Rasp, File, Drill and Drill-bits.
Step 1: Prepare Stock, Decide on Dimensions
I found the wood to use for this project in the warehouse where I work. They had just done some restroom renovations and delivered new doors for the project. A pallet made out of pine would not hold the weight of so many doors, so these shipped with giant poplar squares underneath the doors to allow clearance for the forklift tines.
I took two of these "square" pieces and cut them in half- along the width and length. From there I took one and glued it up for the seat. The rest of the pieces were used for the legs and stretchers. The thickest part of the legs were 1 1/2", so they need to be at least that thick for the legs.
I had just enough width to create a 13" round seat. After looking at some designs, I decided on 18" legs that splayed out 111 degrees from the base. In the second photo you can see my drawing where I decided on the geometry. I drew 118 degrees on one side and 111 degrees on the other. 111 degrees looked better and didn't make the legs stick out too far from the seat footprint, especially since this will be a short stool. Once the legs are cut level and flush it should give you a seat that is 15-16 inches off the ground.
The legs are 18 inches long, if you look at photo 3, you can see the dimension I chose for the shape of the legs. The base of the leg is 7/8 of an inch, tapering to 1 1/2" at the 5 inch mark- this is where the stretches will attach. The leg then tapers to 5/8" at the 16 inch mark and that tenon is 2 inches long giving you 18" total.
SO! Let's do the "math" part. To draw a circle you need to use a compass and know the RADIUS (key word here) you will use. Since the seat I made is 13 inches, the RADIUS is going to be 6.5 inches. Draw this out and cut out your circle, that will be the seat.
NOW let's talk JOINERY. The legs are going to come up straight through the seat to the top. The harder you sit on this stool, the tighter the joint will get where the legs meet the seat. This makes the stool bomb proof. I chose a radius of 4 inches for the leg mortises (holes drilled in the seat for the legs). Draw that circle on the stool (see photo 1) Now "walk" your 4 inch radius around the circle- that should give you 6 points, that if you connected them, would make a hexagon. Ignore every other mark to get 3 equal points- this is where you will drill the holes for the legs. Connect each of those points with the center of the stool.
Step 2: Turn the Wood on the Lathe
Now comes the fun part. I inherited this lathe from my Grandfather, and this is the first project I'm making on it!
You'd think I'd make a pen or a cup or a small bowl for the first project...but don't you remember I'm obsessed with CHAIRS!
Photo 3 shows how I used the template to mark the dimensions on each piece, then I used a jig called a GO/NO GO to ensure that each part was the correct size (photo 4). The way these work is you turn the piece round, and when it fits, it fits! I used plastic and it kind of melted from testing so much, so I recommend you use hardboard instead- I just happened to have this plastic sitting around. I don't have a pair of calipers- that is what is typically used to measure/test things on the lathe.
Fancy expensive lathes have an attachment for the outside of the spindle to turn large items, but I don't have that. SO instead I created my own with plywood and bolted the seat onto the end, this way I could turn the "dish" shape into the seat and the bevel on the underside. I used a pipe clamp propped up on a ladder as the steady rest for this operation (photos 2 and 5)
By the way- the "dish" in the seat is 1/2" deep at the center and tapers to the edge of the stool. I had also already drilled holes when I decided to bolt it onto the lathe, so I plugged them with 5/8" dowels to avoid tear-out when turning it. (Photo 6) The dowels were friction fit and didn't come loose. They tapped right out after the turning.
Step 3: Drill Holes in Seat and Legs- Dry Fit to Test
OK NOW! This is the part with the most complications- but we don't need to worry about that, we have rubber bands and string!
Remember how I chose 111 degrees for the leg splay? Well the secret is this...make a jig! (like a "Kreg" jig) 111 degrees is 21 degrees off 90- so we'll use that to our advantage. Drill a 5/8" hole straight through a block of wood. You have to mark the center line on the block of wood, you'll need that later to line it up on the seat. After you have drilled the hole in the block, cut the block at 21 degrees and put sandpaper on the bottom (photo 3). Now all you need to do to drill the seat is line up the jig with the line that connects the center with the 3 points along the 4 inch RADIUS (Photo1)
OK, now that the legs are drilled, let's dry fit them (Photo 8) and mark for the stretchers.
I decided to put the stretchers 5 inches up from the bottom of the legs, so take a pencil and tape it to a bevel gauge and mark the legs at that height (Photo 4). Wrap a rubber band around this mark- this is the angle you will need to drill at. Find the center of the leg by wrapping a rubber band around the line you drew and stretching a string tight across (Photo 5) This will show you where you need to drill- mark this with a center punch. Because the angle you need to drill is pretty steep, I started the hole with a screw tip auger, and switched to a forstner bit once I had the hole started. Photo 2 shows the drill bits I used. The metal plate has a 5/8" hole drilled out and lets you test and make sure all your tenons are the correct size before you try to jam them into the holes you drilled.
Using the rubber band as a guide, drill a hole into the center mark you made (Photo 6) You want this hole to be one inch deep at the most shallow point. Once you have drilled the holes, take 2 shorter sticks and push the legs apart, inserting the sticks into the holes you drilled. Strike a mark on the sticks, now when you line up the marks you have the distance (length) you need to cut the stretchers.
A note on the stretchers: Make these about 3/8" longer than your measurement. This will put the legs/stretchers under tension, and your legs will NEVER come unglued. Once the stool is assembled it will be rock solid.
Step 4: Glue Up, and Mistakes to Avoid!
Learn from me- don't make these mistakes:
When I was dry fitting the legs, I didn't tap them in carefully a little at a time. Because the stretchers are pushing the legs apart, they angle in a little bit and I forced one of the legs and it caught on the edge of the mortise and tore out the wood. (Photo 1) Lesson: always tap the 3 legs a little at a time when test fitting. You can see I glued it back down in photo 3 and it's (mostly) invisible now.
You want the joints to be tight, but not TOO TIGHT! I forced one of the stretchers that was a little too big for the hole, and started to split the leg (Photo 2). I removed the stretcher, filed it down a little bit, and added glue to the crack. If it feels like it won't fit- don't force it, shave away the wood a little at a time.
The way the legs attach at the seat are with a wedge glued in a slot. You need to orient the wedges so you don't split the seat in half. There is A LOT of force when you add the wedges, so you want the wedges to be forcing the grain vertically, not side to side as this would risk splitting the seat (Photo 3)
With those red flags out of the way, saw a slot in the top of the legs, deep enough to reach the bottom of the seat. Cut and file wedges for each slot. (Photos 4 and 5)
Time to glue it up! Put glue in each mortise and in each tenon and fit it together. You may need a mallet to persuade it to go together, just remember to not force anything. If it fit together without glue, it will fit together with the glue, it just might be a little sticky. Put glue ON ONE SIDE of the Wedge ONLY and hammer them in. By only putting glue on one side of the wedge you allow it to move seasonally. Wood moves, and if it's nailed or glued where it shouldn't be, it's going to split- just go look at your fence outside...I'll wait. Putting glue on just one side of the wedge will allow a crack to open up if necessary, then it will close back up with the changes in the seasons. Chances are this won't happen if the stool is indoors, but if it's outdoors with big swings in temperature, it's a best practice. After the glue has cured, cut the wedges flush with the seat.
Step 5: Sand, Sand, Sand and Level the Legs
Time to get your sandpaper. The best thing is this: if you sand the pieces on the lathe, you can get a great finish right off the lathe and minimal sanding is needed after the fact.
Still, if you want it to be that much nicer, sand it through the grits. I sanded at 80, 100, 120, 180, 220, Sprayed with water to raise the grain, then 220, 320, 400 and 600. The first 2 photos show the results of that sanding, and it just feels like glass.
Use a level to shim the legs in preparation for marking where to cut the feet of the stool. I decided to flip it upside down and mark the feet level this way...
Step 6: Apply Finish and Buff to a Shine!
I chose a gloss finish and wiped on a few coats, sanding in between the last coats and buffing it to a shine.
I'm really pleased with how this turned out, and look forward to making more places to park it.
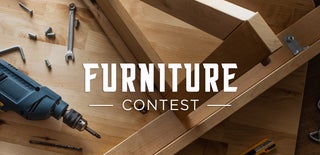
Participated in the
Furniture Contest