Introduction: Solder Strength Test
"The only difference between Science, and screwing around - is writing it down."
I picked up this delightful quote by Alec Jason via Adam Savage, hearing about some fun tests they got to do on the Mythbusters show. That is the basis of this experiment, I'm going to write down some data that will be useful for me when I build anything using solder. I have often wondered just how far I can push it - safely and responsibly of course...so let's do that!
If you read my 2 cents on stained glass design, you know I'm not a fan of stained glass that is 3-dimensional. I still think that 90% of stained glass that is 3D looks bad. That doesn't mean ALL of it is bad, so naturally I want to figure out what works. Something I am interested in trying- is making Calder style mobiles that hang from the ceiling. Because I want to make these out of stained glass, I need to be sure that what I make does not come crashing down because it is not strong enough.
These strength tests should help me understand how much weight these structures can handle.
Supplies
To replicate this test, you need a soldering iron, butane torch, copper wire (14 gauge), copper pipe (3/4" type L) Craft brass tube, and solder (lead free and 60/40.) You will also need some sandpaper to scuff the surface, flux, and some kind of weight to test how strong they are. Wire-cutting pliers and a tube cutter will come in handy as well. If you want to notch the copper pipe like I did, you will need a 3/4" diamond coated drill bit, drill press, and vise- tube notching is really hard otherwise...
Step 1: Let's Get Technical
When you start to think about how well an adhesive works you have to get technical. This is where your eyes might glaze over when you see all these charts and graphs with material property terms like tensile strength and shear strength, etc...
The technical data sheet for the 60/40 solder I use in my work says it has a shear strength of 5700 psi and tensile strength of 6400 psi. That's all nice and well, but I don't know under what conditions those tests were done or the paramaters...so I'm going to make my own test, and explain it in plain English words I can understand.
This nice little video by LOCTITE gives a good explanation of the strength tests done when thinking about glue.
Basically, the glue has to stick to one surface, stick to itself, and stick to another surface. The bond could fail in any of these three areas. If the glue is strong enough to hold everything together, the failure will result in the material itself, then you know that the constraint of your project is not the glue, but the strength of the material itself. (i.e. paper or wood tearing before the glue joint fails)
In my opinion it doesn't get much better than welding when it comes to "adhesives." Soldering seems to be the next best thing when joining metal, and is much more affordable and approachable than welding. I don't want to do any math or try and factor in 6 different variables...I want to know how strong this joint is- strong enough to hang from a window? Strong enough for a toddler to stand on? Strong enough to hang 3 pounds of stained glass from a single wire? That's what I'm going to explore in these tests, and I'll get my answers!
Step 2: Let's Get Practical
There are 2 ways I solder...traditional pipe soldering like you might see plumbers do on water pipe, and soldering with a soldering iron- for electronics or stained glass.
Pipe soldering is similar to jewelry making, the pieces need to be clean and free from oxidation or dirt. Flux is applied to the metal, and the metal is evenly heated with a torch until the solder flows into the joint.
Copper pipe is usually joined with fittings, but I am going to try and do some "tube notching" and see if I can get it to work, because I like how it looks. This is achieved by notching the end of the pipe with a drill bit that is the same diameter as the pipe you are welding (or in my case-soldering). This provides a snug fit so everything is nice and tight.
When soldering with a soldering iron, you touch the soldering iron to the place you want to solder, and then flow the solder. It can be pin-point precision. I really like the work jiripraus does- you should look at his soldering with brass tubes and LED's!
Step 3: Rules of Engagement
We are going to get real scientific here...I am using 2 buckets and my own body weight to test how strong this is. The smaller bucket is 11.2lbs, (5 kg for my metric friends) and the larger bucket is 31.5lbs (14.2 kg).
I weigh somewhere in the vicinity of 200lbs, (90.7 kg) maybe a few pounds heavier, maybe a few pounds lighter...for the purposes of this test...let's call it 200lbs.
The copper pipes and wires will hang from my swing-set in the back yard, where we will see how much weight they can handle.
Step 4: Copper Wire Strength Test
The copper wire I used was scrap wire from a large bundle from an old air conditioning unit. The wire is 14 gauge and surprisingly rigid- perfect for making a mobile out of stained glass, as copper solders really well.
I did 2 different tests- wires soldered end to end, and overlapping by about 2 inches. I did not expect the wires soldered end to end to hold much weight at all, since there is a tiny gap between the wires.
Running the test I was pleasantly surprised. The wires joined end to end held both buckets, but failed when I added my own weight.
The biggest surprise was the wire soldered together with a 2 inch overlap, it even held my weight! I have photo proof if you skip to the end... I had to add the "C" clamps so I had something to hold on to.
Step 5: "Strong Line" (Copper Coated Steel) Strength Test
I love using strong line. It is a very thin, flat, steel wire that is coated in Copper so it will take solder. It's primary purpose is to make stained glass rigid, so the windows won't sag and droop over time.
All that being said, I have used it to encase my "crayon terrazo" and build 3D structures- some recent ones I am really excited about.
In terms of strength, it is every bit as strong as the copper wire, and actually stronger. The downside to this material is it can work harden, which means if you bend it back and forth 8-11 times it will break- a phenomenon of most wires. It is quite robust and versatile...
Step 6: Brass Tubing Strength Test
Brass tubing is a wonder-material. It is sold in many sizes so that they slide inside each other and are telescoping.
The 14 gage wire fits neatly into the brass tube (of the right size) and solders into place very well. I am using this to create little bird perches that will eventually have stained glass birds soldered onto them. The brass to wire connection is just as strong as the other tests, though one area I did have a problem was trying to solder it to a large piece of copper. The copper was too large for me to heat up properly, so the brass tube did not solder very well to the copper plate. I imagine if I heated it up beforehand with the torch it would have connected better, but I was using the soldering iron in this case so it came apart. I think the larger piece of metal was acting like a heat sink and preventing the area to heat up evenly.
Step 7: Copper Tubing Strength Test
The first test was the copper soldered together with the "T" fitting. It held both buckets, and my weight. When I put my weight on it, the copper started to bend. This was the strongest joint since it has some mechanical advantage with the "T" fitting AND solder.
I was pleasantly surprised when my "notched" pipe held the weight of the small bucket, then the large bucket. When I added the small bucket on top of the large bucket, it failed and started to separate where the solder didn't connect to the pipe. I think this would be able to hold the weight of both if I could improve my soldering so the seam went all the way around the pipe, not just 30% of the joint. This happened because the solder followed gravity and pooled at the bottom- I couldn't get it tight enough at the top for it to join. I blame my sloppy set-up and (not metalworking) clamp.
Step 8: Winner and Surprise Findings
The winner of the strength test by a large margin was the copper pipe with fittings. It held together so well I'm sure that the copper would bend, tear or break before the solder joint failed.
The surprise was the copper wire! The piece soldered end to end held both buckets, and the wire overlapped by 2 inches held my weight! (I'm hanging!)
The order of strength (according to my highly scientific observations) are as follow:
- Copper Pipe with fittings
- Notched copper pipe
- Overlapped Strong Line
- Overlapped Copper Wire
- Brass Tubing with copper wire inside
- Copper Wire soldered end to end.
With this information, I am confident I can make 3D objects and stained glass mobiles that will hold together (and hang safely!) and opens up some design possibilities.
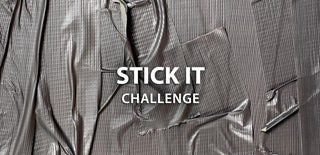
Participated in the
Stick It Challenge