Introduction: Modern Platform Bed // Hand Tools + Framing Lumber
I used to work for a commercial interior designer as a shop hand. Before I got fired for literally laying down on the job (more on that later), I learned some helpful tips/tricks and how to apply the ethos of doing more with less, to interior design and structural builds. Since then, I’ve been using simple plywood and framing lumber to make furniture and decorations. It’s cheap, strong, readily available, easy to work with and with some clever techniques or design elements, can be made to look like something finer.
Nice looking, solid wooden bed frames are expensive. My goal with this, and maybe all designs, is to hack the system: To have something nice, that I truly love, while saving money to use for other experiences in life. I think that's what I like so much about minimalist design principals, including how to do something with the least amount of time or effort possible. Rather than being about the thing itself, it's also largely about how it fits into the rest of your life and the kind of freedoms it provides.
If you want a nice bed frame for a fraction of the cost of something store-bought, this is one way to go about it.
Key Elements of this build:
- Cheap
- Durable
- Beautiful
- Almost anyone can make it
Fringe Benefits
- Accessible materials
- Requires only minimal hand and power tools to build
- Provides ample storage underneath with minimal view of what’s stored
- Built in night stand
- Customizable
Material Cost: Less than $175
Step 1: Tools & Materials
Tools!
- Circular Saw
- Jigsaw or multitool
- Drill
- Speed Square
- Tape Measure
- Pencil / Marker / Pen
- Ear Protection
- Safety Glasses
- 2 medium sized quick clamps
Materials!
- 9 2"x4"x8' framing boards
- 8 2"x12"x8' framing boards
- 1 2”x12x6’ framing board
- 8 or more screws that are at least 2.5" in length
Step 2: Optional Tools and Materials
- Pocket Hole Jig & Screws
- Wood Putty
- Power Sander
- Hammer
- Chisel
- small "L" brackets
- wood putty
- wood stain
- Wood Glue
- Mineral Oil
- Ployurethane
Although it's not necessary, I opted to use a pocket hole jig to join certain boards with pocket holes joints. Since it’s optional to do so, I won’t get into the specifics but there are tons of helpful resources to learn more about pocket holes and how to use a pocket hole jig. If you opt to go that route, do so with 2.5” pocket hole specific screws (right next to where they sell the jigs at the hardware store). Otherwise, using normal screws and small “L” brackets works well too. Either strategy will allow you to disassemble the bed frame in case you ever need to move it to a different room or building.
Regardless of what strategy you use to fasten the boards, the entire project can be completed for less than $175 in materials. That’s high end furniture durability and aesthetics for a low-end furniture cost!
Step 3: Design
What is a bed frame?
- Raises mattress off the floor
- Provides storage space underneath
- Looks nice and makes a room cozier // more inviting
Less is More
Slot-fit construction (also called interference fit) is ingenious. It uses the material itself to provide rigidity to a structure and negates, or seriously cuts down on, the need for fasteners when done correctly.
Structural Pieces
The frame gets it’s structure from a “Spine” that runs head to foot, that has four “Vertebrae” that run from side to side, intersecting at 90 degree angles. The mattress is supported by the 2”x4”s, running across the top of the notched out skeleton. The vertebrae are notched out to fit the width and depth of the 2”x4”s so that the top edges of the skeleton and the mattress supports are all level with each other. This means that every piece of wood except for the runner board and the headboard are providing support to the mattress.
Aesthetic Pieces
The headboard is just another 2”x12”, fastened to the rear side of the far vertebrae with screws. The runner board is more 2”x12”s, cut to fit around the mattress. It’s placed on top of the skeleton and mattress supports and provides a ledge that prevents the mattress from shifting in any direction.
Dimensions
This design can be tailored to fit a mattress of any size. All of the dimensions listed here are to fit a full sized mattress
- Width (side to side): 71.5”
- Depth (foot to rear edge of headboard support): 83.75”
- Height (floor to runner board upper surface): 12.75”
- Height (floor to Headboard upper edge): 33.125”
Footprint
I opted to use 2”x12” lumber for the runner board. If that footprint is too large, you can always use smaller boards or opt out of the runner completely. The same design without the runner board brings the footprint to little more than the width and depth of your mattress itself.
NOTE: A little helpful tip that I had to realize the hard way, is that framing lumber is never actually the dimensions that give each board it’s name. This has to do with the finishing process while it’s being milled. For a chart with actual vs. nominal lumber sizes, see the images above. Taking that into account can save you a lot of headaches when it comes to designing something from scratch.
Step 4: Purchase Materials
Here’s that list again for ya:
- 9 2"x4"x8' framing boards
- 8 2"x12"x8' framing boards
- 1 2”x12x6’ framing board
- 8 or more screws that are at least 2.5" in length
I got mine at Lowes. You can generally get framing lumber at any lumber yard but it’s good to check in advance. My local Home Depot didn’t have any 8’ 2”x12”s. They only had 12’ers in stock.
- Look for boards that are straight. A little bowing is inevitable but the less the better.
- Lowes and Home Depot will make 90 degree “cross” cut for you at the store if you ask. First 2 cuts are free. Every other cut is $0.50
- Purchase and load the wood and any fasteners you may have pick up, into your car.
- I drive a small SUV. We loaded as many boards as we could into the trunk with the seats folded down and strapped the remainder to the roof. If you do the same, drive slow and take the back roads home.
- Framing lumber falling off the top of your car can be extremely dangerous for you and/or other drivers.
- Once you get home, bring the wood to an area that’s large enough for you to do the work on the long boards. It was cold and dark so we set up inside. We happened to have a large, empty front parlor inside, so that worked out pretty well as a temporary workshop.
Now that you have all of your tools and materials in one place, it’s time to measure for your cuts!
Step 5: Choose Your Boards
Decide which boards are going to serve as each part of the frame. Find the pieces with the best looking grain and set those as the pieces that will be most visible: the headboard and the runner boards.
Step 6: Crosscuts
There are 3 different types of cuts we’re going to make. In order of simplicity those are:
- 90 degree cross cuts
- 45 degree miter cuts
- Notch cut
We'll start with the crosscuts.
Measure
Gather the all of the 2"x4"s and the 2"x12" boards you decided will serve as your skeleton & headboard. Measure and mark the boards at the following lengths. Using the speed square will ensure nice straight, perpendicular lines. For more info on using a speed square: click here!
2"x12"s
- 1x Headboard: 64.125”
- 4x Vertebrae: 75.5”
- 1x Spine: 88.75”
- 1x Front Runner: 75.5"
- 2x Side Runners: 82.25"
2"x4"s
- 2x Headboard Supports: 33”
- 8x Mattress Supports: 77.5”
Cut
- Put on some eye, ear and respiration protection.
- Using the circular saw, cut along the outside edge of the pencil line. Watch the blade to ensure you're cutting where you need to. Move the saw forward with steady and even pressure. Being sure not to move faster than the blade can remove material, and not so slow that the blade heats up the wood, causing burn marks.
Step 7: Miter Cuts
The runner boards, bottom corners of all the skeleton pieces and back corners of the headboard supports are all cut with 45 degree miter cuts to give things a stylized look. The speed square makes quick and easy work of marking 45 degree lines as well.
Measure
Skeleton & Headboard Bottoms: at both ends of the skeleton pieces and headboard, find the middle of the board (5,5/8"). From there, use the speed square to draw a 45 degree angled line toward the inside of the board. Make sure you make the marks so that you'll be cutting away the bottom corners on both sides of each board
Runner Boards: This is a little different since we have not yet cut these to length. For the sides, we're going to leave one end flat and mitre cut the other, with the longest tip of the board measuring 86" from the back of the flat edge. Find that length with a tape measure and use the speed square to mark the angled line. For the front runner board, mark the angled lines so that they come in toward each other with the farthest pointy tips measuring 75.5" apart.
Cut!
Just as before, put that safety gear on and use the circular saw to make the cuts, watching the blade to ensure a straight go at your pencil lines.
Step 8: Cut Skeleton Slots
The slots in the spin are cut so that the vertebrae slide into them from the top. Each slot is measured to be the width of the intersecting board (1.5") and half the depth of the intersecting board (5 5/8"). That's how we get a nice sturdy fit.
Slot Positions
- Spine (measured from front edges): 9 3/8", 34 1/4", 58 7/8", 84 3/8"
- Vertebrae (measured from center of board & slot): 75 3/8
Making The Cuts
- Measure out the positions of the slots on each board.
- Use your speed square to get straight perpendicular lines where you will actually make the cuts.
- Use your circular saw to cut the exterior edges.
- for the flat part in the center of the board that connect the two cuts, use your jigsaw or multitool to fully remove the piece of wood.
Alternatively, you can also use the same method for making the mattress support notches: Make a bunch of perpendicular cuts with the circular saw until the thin pieces of wood can be broken away by hand or with a hammer and/or chisel.
More or less like this video below, but with the different dimensions of 1.5"x5.625" (half the depth and the complete width of a 2"x12") instead.
Step 9: Cut Mattress Support Notches
Measure & Mark
Take the 4 vertebrae and squeeze them together with the quick clamps. Be sure to square up all of the edges. Once clamped, it should look like one giant board. Using a pencil and your speed square, mark where the notches will go for the 2”x4” supports. Each notch will be the width of a 2”x4” AKA 3.5” wide. Draw an “X” in the space that will be removed so that you know exactly where to cut. Using the depth gauge on your circular saw, set the depth of the cut to be the exact depth of a 2”x4” AKA 1.5”.
Cut!
Put that safety gear back on and pick up that circular saw! Start by carefully cutting the exterior edge of each notch across all 4 boards, in smooth steady passes. Then use the saw to cut a bunch of straight lines in-between the two edge cuts. Once you’ve made enough cuts, there will be a bunch of thin slices in-between the two exterior edges. Simply break them off with your hand or use a hammer to knock them away. Once you’ve done this for all 8 notches, remove the clamps and get ready to assemble your new bed!
Step 10: Assembly
- Place the spine where you’d like the bed to go.
- Slot each vertebrae along the spine. You may need to make adjustments to the slots if you didn’t cut them wide enough. It’s ok if that’s the case. I always play things on the safe side when making the cuts because you can always remove more later but you can’t put any back once you’ve cut it off.
- Place the 2”x4” mattress supports in the slots along the vertebrae. If you’d like, you can fasten them down with screws but it’s not necessary.
- Attach the headboard supports to the back of the headboard with screws. Be sure to drill pilot holes slightly narrower than the diameter of the screw before doing so to avoid splitting any of the boards. Use the same method to screw the headboard into the back of the rear vertebrae.
- Place the runner boards on top of the Skelton and attach them together with your chose fasteners:
- "L" brackets from the underside into the vertebrae
- pocket hole from the underside vertebrae into the bottom of the runner boards
- for an easy but maybe less attractive fasten: From the top of the runner down into the top of the vertebrae with screws.
However you got it on there... congratulations! You’re basically done!
Step 11: Finishing the Wood
At this point it’s totally up to you. The bed frame will totally work regardless of what you do at this point. Personally, I like the look of natural wood. All I did to finish mine was sand things down to a fine grit (320) and rub in some mineral oil mixed with bees wax, to bring out the depth and color of the grain. This darkens the wood ever so slightly and brings out a richer contrast in the grain.
Alternatively you can stain the wood to a color of your liking. At that point you can choose to use a sealer like polyurethane after the stain or just use a sealer without staining it. NOTE: You can’t stain the wood once you’ve sealed it, so just know if you go that route, a sealer is always the last step. Sealing wood is an involved process. Since a bed frame isn’t something that’s going to redial come into contact with liquid, it’s not necessary. However, it technically will increase the lifespan of the wood. Water based sealers are a little easier to put on and clean up. Oil based sealers bring out a richer contrast in the wood grain and darken things a little bit.
So you’ve got options!
Step 12: Clean Up
Step 13: Pat Yourself on the Back
After all the hard work, you deserve a nap. Good thing is, you’ve got a beautiful new place to do so. Not only that, but you’ll sleep like a baby due to all of the satisfaction that comes from making something yourself.
Be sure to drop a comment or reach out in any way if you’ve made this project! Would love to see what you think and what you came up with. Feel free to make changes and interpret things as you will.
Happy making, and all the best as you get to now lay down on your finished job!
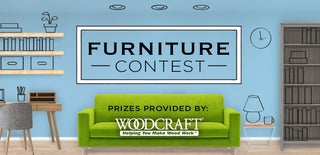
Second Prize in the
Furniture Contest 2017