Introduction: Laser Cut Drink Tray
When I started using the laser cutter, I quickly became obsessed. I had a background in graphic design and all of a sudden I had a tool that could turn my two dimensional digital images into three dimensional physical objects... This was mind blowing! I started by making rastered & cut business cards for myself out of recycled scrap paper, as well as coasters and ornaments to give to friends and family. It made sense to sell them too as, once you have the files to make something, it's so easy to reproduce!
A friend was opening a new boutique for the holidays and asked to include some of my stuff. I wanted to have a more complete set, and though a drink tray would be a nice compliment to the coasters. For this new project, I had some goals that I wanted to accomplish:
- Make something more complicated than what I had been doing.
- Use nothing but the same cheap 1/4" plywood that I had been using for everything else. (Roughly $1.25 per 1'x2' sheet after being cut down!)
- Utilize the technique of press-fit construction that I had learned from other brilliant members of AS220 Industries.
- Create an interesting image on the floor of the tray that accents the precision of the laser cutter, out of nothing but the same laser cut wood, stained to be different shades.
In the end, I had problems with the epoxy and didn't have time to make a sellable product for the Christmas pop-up sale, but I've since had the time to work out the kinks, and really love the final product! This project can take a long time to make if you really care about crafting a finely finished wooden object with an epoxied inlay, but when completed can be beautiful and durable enough to kill a bear! Don't do that though... Bears are cool! If you're not too concerned with the finer details and just want something that'll hold drinks and/or food, you can easily make one of these in less than a day :)
If you like this instructable, please consider voting for it for the Full Spectrum Laser contest. If you'd like to learn how to make anything or just have the tools to do so, check out AS220 Industries! In addition to a full Fab Lab there's an incredible print shop, computer lab, photography studio, dark room and audio engineering tools all for public use!
Step 1: Tools & Materials!
- 1/4" plywood: 4 sheets - 12" x 24"
- Laser cutter
- Vector file software such as Adobe Illustrator or whatever your laser cutter calls for
- Wood glue
- Clamps and/or ratchet ties
- Sandpaper - Grits: rough to smooth out hard edges // fine (220 or above) to smooth out the flat surface
Optional
- Epoxy resin
- Wood stain or paint & appropriate applicators
- Krazy/super glue
Step 2: Box Maker!
http://boxmaker.connectionlab.org/
I'll admit it. I cheated a little. I didn't make the Illustrator file from scratch because I didn't have to!
An easy way to get the geometry tight for any press fit construction box type thing, is to start with boxmaker.connectionlab.org. All you do is punch in the dimensions of your box, hit "design it" and viola! You have a PDF vector file that you can use to cut out said box.
IMPORTANT: Since the laser I'm using can only cut through material up to 1/4" thick, I double up the wood by cutting two of everything and gluing them together to make 1/2" thick pieces. If using the same technique, keep that in mind when punching in the dimensions and be sure to put 2x the thickness of the material in the appropriate section if you're going to do the same thing. It's good to use calipers to measure the thickness of the your wood. The more precise you can get with that, the less work you'll have to do later.
Also, be sure to click "advanced options" and set the cut width to something between 0.008-0.004, which is roughly the amount the laser takes away. It's not much, but enough to make a difference if you want a good fit. It's so nice to have the box maker take that into account!
For my purposes, I do this to get the bulk the line work done and then edit the file to turn it into a tray.
Attachments
Step 3: Edit the File!
Since the drink tray has flat edges on top of the sidewalls, remove the lines that create the box joint teeth, and create a new straight one from end to end.
On the side you want your handles, it's as simple as putting a hole. On mine, I put the handles on the short edges and raised the top edge with a subtle curve to make it resemble something more of a traditional handle. This isn't necessary though.
The bed of the laser that I use is 12"x24". For this tray, two separate files are needed to account for the fact that all of the pieces won't fit within those dimensions.
- File 1: The bottom piece
- File 2: The side pieces
Now that the files are created and saved, it's time to use the laser to cut the pieces out of wood!
Step 4: Cut the Pieces!
Again, I doubled all of the pieces up and ended up using 4 sheets of 12"x24"x1/4" plywood. I probably could have fit them on to less sheets if I didn't care about the direction of the wood grain. All in all, I only used 1/4 of the full 4'x8' sheet of wood... aka $20 / 4 = $5 worth of wood. Not bad if you ask me!
Safely Cutting Your Pieces
- Load file and set the print preferences. For this wood I ended up setting them to Speed: 12%, Power: 100%, Freq: 400 Hz. You'll find that every piece of wood is different, so I recommend doing a test cut just in case.
- Turn on the exhaust fan so the room doesn't fill up with the smoke or vapors from your cut material.
- Turn on the laser & place your material on the bed of the laser cutter.
- Set the focus. I use the focus gauge: Turn it upside down and raise and lower the material bed so that with your material on it, it just barely touches the bottom tip.
- Set the home position by pressing the button "x/y off" and positioning the laser to the upper left corner of your material on the bed. I always do this but it's not necessary. By default, the laser I use moves to about an eighth of an inch from the upper left corner of the bed.
- Close the lid and hit go!
Optional: Putting a layer of application tape on the the top and bottom of the wood can prevent burn marks from forming. I usually don't bother as I find it cheaper and less time consuming to just sand them off afterward. A lot of people don't mind, and just leave the burn marks on. Personally, I want it to look as nice as possible and I'm willing to put in the time, but it's entirely up to you!
Step 5: Construction the Tray!
Now that you have your pieces, it's time to put them all together!
- Glue the double layers together.
- Put glue on the joints, and clamp all of the pieces them together.
- Wipe up any access glue.
- If you're going to create an epoxy inlay, fill and gaps or openings with glue.
- Wipe up an excess glue.
- Let the glue dry for the manufacturer recommended amount of time or overnight.
- Take the clamps off and sand any dried glue spots.
- Give the tray a final sanding with a fine grit (220-400)
- Optional: Rub down the whole tray with mineral oil, polyurethane, furniture polish or any other wood finish. Be sure to check the manufacturer label for it's food safety grade if you think anything edible will be coming into contact with the tray.
- Pat yourself on the back. You're basically done!
Step 6: OPTIONAL: Inlay!
With your tray as you have it, it'll hold things and work just fine. For mine, I wanted to utilize the laser to add a geometric inlay that would have taken me a long time to do by hand, and even so, never would have been as precise! Taking time into account, the laser allows me to do things I would never do otherwise and the lines come out flawless and with the beautifully burned, characteristic, dark edges.
- Make the file: It can be whatever you want!
- Cut it out on the laser
- Stain or paint your pieces
- With a drop of crazy glue, place them on the floor of your tray. This will prevent them from floating up once the epoxy is poured.
- Mix and pour the epoxy, following the manufacture instructions. TIP: A quick and easy way to get the bubbles out is by putting the flame of a butane torch a couple of inches from the surface, but be careful not to burn or catch fire to the wood!
- Let it sit for the recommended time and be sure to keep it in a clean environment while drying.
Once it's completely cured, you have a beautifully encapsulated "inlay" on your new custom drink tray!
Attachments
Step 7: Serve Some Tea to Your Mother on Your New Drink Try & Thank Her for the Years of Hard Work and Giving Birth to You
That's right. The icing on the cake. What's a job well done without good ol' mom patting you on the head and telling you how wonderful it is! A real double whammy if you ask me (tea and compliments).
Don't limit yourself to this drink tray though. This project can be done with other materials like acrylic, & the concept of creating laser cut puzzle pieces to turn into a 3D object can be applied to anything you set your mind to: toothbrush holders, gifts for your mom, coasters, gifts for mother's day, light fixtures, Christmas & Chanukah presents for mom, laptop stands, boxes for mom's jewelry or presents for your mom! You name it! If you run out of ideas, ask your mom.
Thanks for reading and my the god of lasers (David Hasselhoff... or Prince... It's probably Prince) be with you!
-Brett
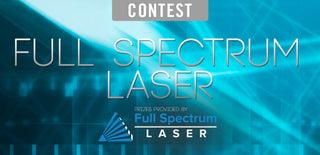
Participated in the
Full Spectrum Laser Contest 2016