Introduction: From Sketch to Reality: Basic Modeling With Fusion 360
As 3D printers, CNC routers, and laser cutters become more accessible, 3D modeling has become an increasingly vital skill. These devices require 3D models for input, and while online models are an option, creating specific or niche models is often necessary. This lesson is a basic introduction to modeling using Fusion 360.
Scope:
In this lesson we will explore basic tools in Fusion 360, creating a foundation of knowledge to build from. You’ll learn to create sketches, define constraints for accuracy, and extrude sketches into bodies while making a doorstop. This guide will hopefully make the use of CADD seem significantly less daunting.
Timeline:
This lesson can be done in a single sitting (30-60 minutes) if you follow along with the included design (creating a door stop).
About Me:
I am a local educator who creates small lessons with makers in my local area (Orlando Fl) I also help those in online groups who need help getting into CADD and 3D printing related activities. My lessons are provided for free with the hope to grow the community and expand its creativity!
Supplies
You will need a computer and Fusion 360. A modern computer should suffice for basic designs. Fusion 360 has a free version for hobbyist and personal use. This version includes all the features needed for this lesson.
Step 1: Tools in Fusion
For this lesson we will only be using tools in the first two sections: "Create" and "Modify" as well as a section that appears during sketching called "Constraints".
Step 2: New Project
When you start Fusion 360 for the first time, you will be presented with a new blank project. It's important to familiarize yourself with some of the basic camera controls (listed below), and tools that are on screen (in the photo notes). Take some time to look at these, and hover over tools to get a brief description of what each does.
On Screen:
- The first thing to note is the top tool bar. This houses almost all your tools for designing and manipulating your designs and objects.
- In the top right corner, you will notice the view cube. this has a few pre-selectable options and a home view button. You can also click and drag on it to orbit the camera around your design.
- The bottom left is the timeline, a powerful tool that allows you to see each action you have taken, and alter it later if needed. You can also drag the slider backwards to insert new actions.
- In the bottom center of your screen is another small tool bar. This toolbar has buttons for various environment options, as well as buttons for camera orbiting, and panning. Camera panning can also be achieved by holding the middle mouse button and dragging as well.
Step 3: Creating Your First Sketch
Now lets go ahead and start our first sketch! Click "Create sketch" in the top left and you will see 3 squares appear representing planes, as well as 3 colored lines representing each axis. If you click any of these 3 squares you will begin sketching on that plane. For this project we will want to choose a plane suitable for a side profile; we will select the top left plane.
Step 4: Drawing Your Design
Now that you have started your sketch you will want to use the tools at the top to draw a triangle. Use the "line" tool to make a horizontal line 3 inches long, or 75mm. To do this, select the line tool and then place a point at the origin, then enter the desired dimensions in the box given. If your tool has more than one box, like length and angle, you can cycle between these with the TAB key. Again using the "line" tool, add a vertical line on one side by clicking on one of your already placed points; 1.25 inches long, or 32mm. Then, once more use the "line" tool to connect the last 2 points to create your triangle.
Tips:
- Use the ESC key to cancel any active tools
- Hovering over tools will tell you what they do. Don't be afraid to test and experiment! you can always undo them.
- If a dimension is in your way, you can simply click and drag it, to relocate it somewhere out of the way. Do not delete it or the line may have its length altered.
Step 5: Constraining Your Design and Completing Your Sketch
This step, while overlooked by many, is very helpful and important. At the top of your screen you will see some new options while sketching called “constraints”. These lock certain parts of your sketch so that they cannot be altered by new actions or edits. For our doorstop we will be using the perpendicular constraint to make sure the back end stays at a 90 degree angle. Select the tool, then click on the two lines you want to keep perpendicular.
Once you have completed your constrained triangle, your sketch is complete, and you can click the "Finish sketch" button in the sketch menu on the right side of your screen.
Note:
Fusion 360 will sometimes apply a constraint automatically for you when sketching. It will have a small symbol visible near the line, angle, or feature to show you it has been applied. For demonstration purposes I made the triangle skewed to show the process of applying it.
It is also worth noting the order in which you select your lines will affect which line moves, so if they do something unexpected, try undoing and selecting your lines the other way around.
For some, this may be as far as you need to go for modeling. For laser/plasma cutters, or simple router/engraver designs, all you may need is a sketch profile to export. Jump to Step 8 if you are only working with sketches.
Step 6: Extruding Your Sketch!
Now that you have completed your sketch, it's time to turn it into a 3D object. To do this we will use the extrude tool in the top toolbar. You may have noticed that when the sketch was completed you can now highlight and select the inside of your sketch; This is called a profile. To execute the extrude you will want to select the "extrude" tool, and then select the profile (or inside) of your sketch. Once the arrow appears you can simply drag it out to a desired length or you can enter a distance in the value box that appears. For the doorstop we will be extruding the profile 1 inch, or 25mm. Once you have entered the distance you will want to make sure to check one option in the extrude menu. Make sure the operation is "New Body" and then hit enter or select "OK". Once you have completed this you will want to home your camera with the view cube so you can see your triangle in all its 3D glory!
Step 7: Adding the Details.
You now have a 3D triangle; let’s personalize it. To do this, you are going to create another new sketch. Click the "new sketch" button and this time, instead of clicking on one of the planes at the origin, click on the side face of your doorstop. This will allow us to create a sketch on the face of your model. You can press and hold the scroll wheel or use the pan button (on the bottom center toolbar) to move the camera.
Educational point:
This is the point where (in a more complicated design) you could add bolt holes, cutouts, or other details to your objects. You can also create profiles within this sketch that can be extruded or manipulated via the other tools as well.
Step 8: Sketch Out Your Details.
Now that we are sketching on the face of our project it's time for a bit of individuality. At this point you can put a unique design on the side of the doorstop. During this step, it's important to experiment and get familiar with the look and feel of the first three sketching tools (line, rectangle, and center point circle). You can also add some constraints as well.
These designs can range from simple to complex, as long as you are content with it. For my doorstop, I will add two simple shapes. It’s important (and fun!) to add personal touches to projects. Once the design is finished, hit the "Finish Sketch" button.
Tips and Notes:
If you plan to 3D print or cut these out with CNC, make sure that your design meets those capabilities. The angles of the design should be >45 degrees from the front or back to prevent overhangs from the bottom, back, or side, as those will be the applicable print orientations. For CNC, you'll want to make sure there aren’t any profiles that are likely to break or end up too fragile. You will also want to make sure that there are not any floating bodies.
Step 9: Extruding the Details
In this step we will be using the extrude tool. Select "extrude", then select the new shape profile on the side of the doorstop. You can select more than one profile while extruding, so click both shapes to do this in one step. Once selected, drag the arrow in the direction that goes through your doorstop. This could be a positive or negative value, so look closely and see which way the value needs to move. You will know you are going in the right direction because the extrude tool should auto select the "cut" operation. It will also be indicated by showing the extrude as a red cut on your model. Extrude this through your model the full 1 inch or 25mm.
Tip:
When using the extrude tool, you will see an option on the extrude menu called "Extent Type"; this option chooses how far it goes. You can choose "distance", which goes a certain distance, "to object", which will go to a selected object or face and will follow curved faces, or "all", which will make it go infinitely in a direction.
Step 10: Final Touches
For our final operation, we will do some cleaning up. To do this, we are going to apply a simple fillet (or rounded edge) to the 3 corners of the triangle. This will clean up the design, and make it appear more finished. To apply the fillet you will want to select the "fillet" tool in the modify menu, and then select each corner of the triangle. You may have to move your camera around to do this (drag on the view cube). Once selected, apply a .05 inch or 1.2mm fillet to each corner. If you moved the camera while doing this make sure to use the home button near the view cube to reset it.
Step 11: Saving and Exporting
Amazing! You just finished your first 3D model in Fusion 360! Now all that's left is to save and export your model. Begin by locating the file drop down at the top left of the screen; you will see both the export and save commands. When you save, make sure to use a naming scheme that will help you keep track of everything. For students I recommend "Doorstop_LastName" Then use the export button to export your model in a file format that works with your machine you will be using.
Step 12: All Done
Great work on your first 3D model in Fusion 360; have fun experimenting and exploring the program, can’t wait to see what you create!
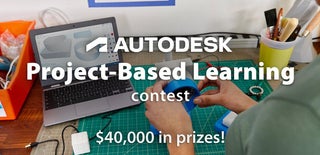
Participated in the
Project-Based Learning Contest