Introduction: Futuristic Fusion: the NeoAir With Fusion 360
NeoAir: The Futuristic Fusion 360 Air Hockey Table
Have you ever envisioned a game of air hockey that not only transports you to the future but also revolutionizes the way you play and interact with gaming? In this Instructables, we are going to create a game table that not only captures the essence of air hockey but also pushes the boundaries of what's possible in gaming innovation. Furthermore, the futuristic design of our Air Hockey Table with its sleek lines, LED lighting, and minimalist aesthetics will surely captivates everyone around it. it transports players into a world where gaming meets artistry. This not only enhances the gaming experience but also elevates the ambiance of any space it occupies.
But perhaps the most compelling reason to 3D print this model lies in its sustainability and cost-effectiveness. By utilizing additive manufacturing techniques, we've minimized material waste and reduced production costs, making the Fusion 360 Air Hockey Table an environmentally friendly and affordable option for both consumers and educational institutions. Also I have shared the stl files please feel free to download it : D
Supplies
- Fusion 360
- 3D Printer
Step 1: Initial Sketching
- Begin by creating a rough sketch of the air hockey table's overall design, including dimensions for the playing surface, goals, and surrounding frame.
- Use Fusion 360's extruder tool to create basic shapes representing the table components.
- Ensure dimensions are accurate according to the finalized sketches.
- Separate different parts of the table, such as the playing surface and goal assemblies, for individual design attention.
Step 2: Extrusion for Table
- Choose the sketches representing the outline of the table surface and any additional features like goal areas.
- Use Fusion 360's extrude command to give depth to the selected sketches, turning them into 3D objects.
- Determine the desired height of the table surface and extrude the sketches accordingly.
- Ensure uniform thickness across the entire table surface for stability and balance during gameplay.
- Review the extruded table surface for any inconsistencies or irregularities, making adjustments as needed to achieve the desired shape and dimensions.
Step 3: Pocket Creation & Corner Rounding
- Determine the locations of the goal areas at each end of the table.
- Use Fusion 360's sketch tools to outline the shape and dimensions of the goal pockets.
- Apply the extrude command to the sketched goal pockets, creating recessed areas in the table surface.
- Ensure the depth of the pockets is sufficient to catch the puck during gameplay, typically around 1/4 to 1/2 inch.
- Use fillet or chamfer tools to create smooth transitions between the pocket edges and the table surface.
- Review the pocket designs to ensure they meet gameplay requirements and aesthetic preferences, making any necessary adjustments before proceeding.
- Once done, Locate sharp corners on the table components that require rounding.
- Choose the edges that form the corners to be rounded using Fusion 360's edge selection tools.
- Apply the fillet command to the selected edges, specifying the desired radius for rounding.
- Adjust the radius of the fillet as needed to achieve the desired level of rounding, balancing aesthetics with functionality.
- Ensure consistent rounding across all corners of the table components for a cohesive design.
- Review the rounded corners in Fusion 360's preview mode to confirm satisfaction before finalizing the design.
Step 4: Goal Assembly & LED Integration
- Use Fusion 360's sketch tools to outline the shape and dimensions of the goal components.
- Apply the extrude command to the sketched goal components, creating 3D objects for the nets and supports.
- Ensure proper alignment of the goal components with the table surface and each other.
- Use Fusion 360's combine or join tools to merge the goal components together into a single assembly.
- Review the design to ensure the goal assembly is sturdy enough to withstand gameplay, making any necessary adjustments for reinforcement if needed.
- Confirm the design of the goal assembly meets all requirements and aligns with the overall aesthetic of the air hockey table before proceeding to the next step.
- Once done, Determine where LED lighting will be incorporated into the air hockey table design, such as along the edges or underneath the playing surface.
- Use Fusion 360's sketch tools to outline the paths where the LED strips will be placed.
- Apply the extrude command to the sketched LED paths, creating recessed areas or channels for the LED strips to sit in.
- Choose appropriate LED strips or modules for the desired lighting effect, considering factors such as brightness, color, and power requirements.
- Install the LED strips into the recessed areas or channels, ensuring they are securely mounted and properly connected to a power source.
- Test the LED lighting to ensure it functions correctly and produces the desired effect, making any necessary adjustments to the installation or positioning.
- Implement a control mechanism, such as a remote control or programmable microcontroller, to adjust the LED lighting settings as desired.
- Review the LED integration to ensure it enhances the overall aesthetic and gameplay experience of the air hockey table, making any final adjustments as needed.
Step 5: Final Touches
- Conduct a comprehensive review of the entire air hockey table design to ensure all components meet project requirements and specifications.
- Detailing and Finishing: Add final details and finishing touches to enhance the aesthetic appeal of the air hockey table, such as decorative features.
Step 6: Export for 3D Printing
- Choose the appropriate file format for exporting the air hockey table design, such as STL or OBJ, compatible with 3D printing software.
- Organize the design into separate files or components for efficient 3D printing, ensuring each part is correctly positioned and oriented.
- Use Fusion 360's tools to inspect and repair any mesh errors or issues that may affect the 3D printing process.
- Export each component of the air hockey table design as individual 3D printable files, ensuring they are saved with the correct settings and parameters.
- Verify that the exported files are compatible with the chosen 3D printing technology and materials, considering factors such as print bed size and material requirements.
- Conduct a final review of the exported files to ensure they accurately represent the intended design and are ready for 3D printing.
Step 7: Ending Words
This Fusion 360 Air Hockey Table represents a leap forward in gaming innovation, combining advanced design, futuristic aesthetics, and the accessibility of 3D printing technology. Whether you're a student looking to push the boundaries of design, a gamer seeking a unique gaming experience, or an educator aiming to inspire the next generation of innovators, This project offers something truly special. I hope you enjoyed : D
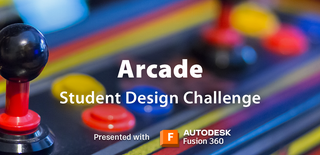
Participated in the
Arcade Student Design Challenge