Introduction: Glowing Color-Changing Guitar
In the kingdom of rock and roll it is important to set oneself apart. With millions of people in this world who can play the guitar, simply playing well is just not going to cut it. You need something extra to rise up as a rock god. Consider this guitar the mystical glowing ax bestowed upon you by the Rock Goddess of Bangs; The fabled ax that will lay waste to nonbelievers and shred through the aether with the transcendent glory of rock. With this weapon of unfathomable power, you will be an explosion of light and sound rising up above the writhing masses.
While there are a couple of other glowing guitars out there, this one by and large sets itself apart. For starters, it is frosted to diffuse the glow of the LEDs. This means that the whole body glows instead of being just edge-lit, and you can also see it during the daytime. The other unique feature of this guitar is that it responds to the music being played. The brightness is adjusted by the volume, and the color is controlled by the duration that it is being played. So, the harder you rock, the more colors you will see.
Step 1: Go Get Stuff
You will need:
(x1) Clear acrylic guitar *
(x1) Arduino Micro
(x1) Addressable 3-color LED strip
(x1) LM741 op-amp
(x2) 2N5457 transistors -- alternate: NTE457
(x1) 10M resistor **
(x2) 2.2M resistor **
(x1) 470K resistor **
(x4) 100K resistor **
(x2) 47K resistor **
(x2) 10K resistor **
(x1) 1K resistor **
(x1) 10uF capacitor ***
(x2) 1uF capacitor ***
(x3) 0.1uF capacitor
(x1) 1N4733A zener diode
(x1) Proto Board
(x1) 3' mono audio cable
(x2) 4 x AA battery holder
(x1) Power jack
(x20) 4-40 x 1/2" bolts
(x1) 6" x 6" x 0.025" glossy stainless steel
(x1) 2-part epoxy
(x1) 12" x 24" x 1/6" sheet of acrylic
(x1) electric guitar string set
* Finding a clear guitar is the tricky bit. Best course of action is to search Amazon or Google.
** Carbon film resistor kit. Only kit necessary for all labeled parts.
*** Electrolytic capacitor kit. Only kit necessary for all labeled parts.
Please note that some of the links on this page contain Amazon affiliate links. This does not change the price of any of the items for sale. However, I earn a small commission if you click on any of those links and buy anything. I reinvest this money into materials and tools for future projects. If you would like an alternate suggestion for a supplier of any of the parts, please let me know.
Step 2: Unstring the Guitar
Wind down each of the tuning machine heads and remove all of the strings.
Step 3: Take of the Neck
Step 4: Remove the Control Plate
Make note of where the wires from the pickups and output jack are connecting to the controls.
Once you are sure you have a record of the wiring connections, cut the wires to free the control plate entirely from the guitar.
Step 5: Remove the Bridge
In my case, one of the pickups came along with it. If you have a guitar in which the pickups are not attached to the bridge, remove the pickups seperately.
Step 6: Remove the Jack
Step 7: Remove the Pickguard
Step 8: Detach the Strap Buttons
The body should now have nothing attached to it.
Step 9: Cut
Solder 18" wires to both ends of the 16" LED strip.
Step 10: Route
Next, make another channel that is 16" long by 0.25" deep by 0.6" wide that starts at the edge of the audio jack mounting holes and runs the legnth of the bottom of the guitar.
These channels will hold the two LED strips. Thus, if your LED strip is longer, you will need longer channels.
Step 11: Drill
Drill another 1/4" hole from the back side of the guitar straight down until it intersects with the opposite edge of the same routed channel.
Drill a similar 1/4" hole to meet the closest edge of the other routed channel.
Step 12: Trace
In my case I found they fit upon the back side perfectly between the two pickup channels.
Step 13: Route
Once the perimeter is cut, route out all of the material that is remaining on its inside.
This should approximately leave a 6.25" x 2.85" x 0.65" rectangular electronics compartment.
Step 14: Wire Channels
Step 15: Insert the Strip
Pass the wires that have come out the back through the other 1/4" hole into the other LED compartment.
Solder them to appropriate terminals on the other LED strip such that the two strips are wired in parallel.
Step 16: Cut, Bend, Glue and Clamp
Once you have the two strips, now comes the tricky part.
Lay the LED strip flat in each of the channels and clamp the edge of the acrylic strip to the inside edge of the channel of equal legnth, and then epoxy the corner of the strip in place. Place a clamp on this corner.
Using a heat gun, soften the strip and form it around the counter of the guitar. Epoxy and clamp the strip in place as you go, until it is clamped in the channel and neatly epoxied in place.
Wait for the epoxy to fully set and repeat this process with the opposite channel.
Of course, this is easier said than done and make take a few attempts go get right. One thing I encountered while doing this is that the clamps tend to slip, especially when there is wet epoxy around. I solved this by placing a few thing pieces of scrap wood over the acrylic and then clamping it. This provided just enough traction to keep it from slipping. However, be careful not to get too much epoxy on the wood or you will have an annoying time sanding this away later.
Step 17: More Routing
Flip the guitar over. Using the same bit, and at the same depth as the electronic compartment, make a notch off one edge large enough for a power charging jack to fit.
Step 18: Drill Connections
Make another hole between the electronics compartment through to the control compartment.
These will be used for routing wires between the components.
Step 19: Fill Gaps
Fill in any gaps around the acrylic strip with epoxy. This will prevent sand from getting into the channel during sandblasting.
Step 20: Tape
Step 21: Sandblast
In the very likely eventuality that you do not have a sandblaster at your disposal, you can pay someone else to do this for you. Typically any place that does powder coating will also do sandblasting for relatively cheap.
Should you not want to go through the bother, you can use an appropriate spray paint to get a nice frosted effect.
Step 22: Clean Up
Step 23: Mark Drill Holes
Place the template over the electronics compartment on the back of the guitar such that it covers all of the routed channels.
Use a pencil and make marks in each of the small mounting holes around the perimeter of the back cover.
Step 24: Sandblast Again
Peel the acrylic's protective coating off the opposite side when you are done.
Step 25: Drill and Tap
Use a 4-40 tap to thread the holes.
When you are done, check to make sure they are correct by threading 4-40 bolts into each of the holes. They should twist in without resistance or being loose.
Step 26: Switch Plate
Step 27: Mark
Step 28: Drill and Tap
Thread these with a 4-40 tap.
Step 29: Trim the Arduino
Step 30: Program
Program the Arduino with the following code:
Step 31: Trim (optional)
Step 32: Build the Circuit
The preamp stage is needed to boost the signal from the pickups to a useable level, and consists of an LM741 using a virtual ground created by the voltage divider on pin 3. It was important to me to keep the circuit simple and not to have to mess around with an opamp that required a true split rail supply.
From the preamp, the output then goes to another stage which both clips the wave and constrains it to a voltage between 0 and 5.1 (in theory). However, because I am using a zener diode to clip the waveform and due to the diode's voltage drop, the wave can actually drop a little below 0. This is less than ideal, but I can live with it and it does not seem to bother the Arduino much. That said, it is good to keep in mind that over time this could potentially damage the Arduino pin that is receiving the signal.
Speaking of which, the only place left for the audio to go in this circuit is into analog pin 0 on the Arduino.
Step 33: Trim
Step 34: Wire the Switch
Pick two pins that get toggled on and off when the switch is pressed. This can be tested with the continuity setting on a multimeter, and by pressing the switch on and off.
Once these pins are identified, connect the audio-in wire from the pickups to pin located in the center row, and the Arduino audio cable to the pin located towards the outside of the switch.
On the set of pins directly next to it connect the audio-out cable, and the Arduino return cable.
Also connect the ground wires from the audio cables to the metal frame of the switch.
Now, on the remaining set of pins next to both of these connect two 18" wires which will be used to toggle the circuit on and off by breaking the ground connection.
Additionally, wire the central ground connection to the metal frame of the switch.
Finally, connect together the two unused pins in line with both sets of audio toggle pins. This will serve to bypass the audio signal past the circuit board when the Arduino is turned off.
Step 35: Install
Next position the switch in its compartment, and affix the switch panel using the switch's mounting hardware.
Fasten the switch panel to the guitar using 4-40 bolts.
Step 36: Bridge
Make certain that the wires get routed properly back to the control panel.
Step 37: Output Jack
Step 38: Ground Wire
Step 39: Rewire
Connect the audio output from the volume knob to the audio-in wire from the power switch.
Also wire the audio out wire from the power switch to the audio jack connection.
Finally, connect a ground wire from the power switch to the control panel.
Make certain that all of the cables that should be grounded are (like the pickups, and audio jack).
Step 40: Control Panel
Step 41: Neck
Step 42: Restring
Step 43: Knobs
Step 44: Connect
These include the audio-in connection to the Arduino, the audio-out connection to the power switch, all relevant ground connections and one of the power connections from the power switch.
Step 45: Power
Connect the ground wire from the battery holder to the terminal connected to the of the M-type power jack.
Connect the power wire from the battery holder to the terminal connected to the terminal of the M-type power jack that gets disconnected when a plug is inserted (typically the center terminal). In this way, when the charger is connected, the power gets disconnected from the circuit board and the batteries get charged.
Finally, connect the remaining ground wire from the power switch to the ground terminal on the power jack. Also, connect a red power wire from the remaining terminal on the power jack to the 12v power plane on the circuit board.
Step 46: Batteries
Step 47: Back Cover
Step 48: Reattach the Strap Buttons
Fasten the strap buttons firmly back in place.
Step 49: And It's Done...
At this point, there is nothing left to do but to turn on the LED display by pressing the power switch and rocking out.
While this guitar is entirely rad - like anything else - it could always be better. Potential improvements include more LEDs, smaller rechargeable LiPo batteries, and adding Arduino frequency detection code to light up different colors for different notes.
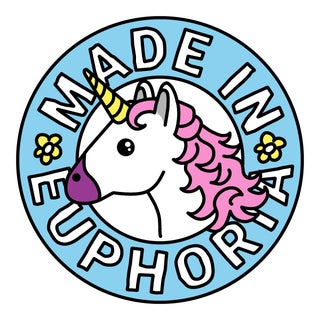
Did you find this useful, fun, or entertaining?
Follow @madeineuphoria to see my latest projects.
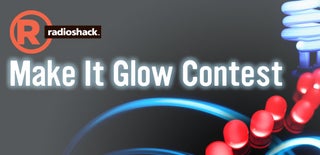
Participated in the
Make It Glow Contest
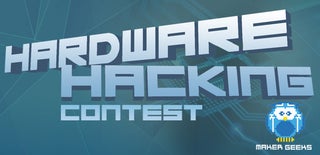
Participated in the
Hardware Hacking