Introduction: Good Luck Coffe Table Made From Fireworks Rocket Sticks and Pallet Wood
hello and welcome, this is a project that i wanted to make for quite some time. i don´t know why, but a couple of years ago i started to take a long walk at the beginning of each new year, and while underway i collected the balance sticks from the firework rockets. I liked the burn marks and knew that i wanted to build something using them. When i got home i started to free the sticks from mud and from the glued on paper. i sat the cleaned ones down on the table in front of me. The burnmark facing up. When i was finished i could not help but notice the beautiful stripe pattern that all the scars of flight formed. I knew that this had to be present in what ever i was going to build out of them.
Finally on my annual walk 5 days ago i knew that the time was ripe. 2020.
I was not able to upload the video on time but it will be available on my channel 8h after this upload.
https://www.youtube.com/user/MudbrainsTvDIY
When i was a child my grandmother used to tell me that the fireworks on new years keep all the bad stuff in the old year. following this explanation: this coffee table, should be quite capable in keeping bad "things" away. I can use that. (and no i am not superstitious. i just like to imagine what my grandmother would have said)
Enough talk.
Let´s start
Supplies
Materials used
- a healthy amount fireworks rocket balance sticks. (this depends on the area you want to cover. The surface in my build was around 700 mm x 500 mm. with the sticks measuring roughly 6mm x 6mm x 600mm, it took me around 100 of them.)
- one wood pallet. or any other kind of wood that meets the quantity.
- one piece of Plywood, which should be a bit larger than the area covered by the sticks.
- some woodscrews. I used around 15.
- Wood glue (PA Glue)
- Wood Glaze, mine came in a nut-brown
- clear glossy varnish (water based acrylic)
Tools used
the only two power tool i really used were:
- a table saw. I think it could easily be swapped for any other kind of saw
- a belt sander. I think this one was most important, because pallet wood can be really warped.
- 90% of the time i just used different non electrical tools. The Rocket sticks tend to splinter easily adn witrh the hand tools i felt like i had the most control.
- sanding paper, a brush, a electrical drill.
- and most important a carpenters square. always check your 90deg
Step 1: Building the TableTop
The way that i have build the is as you can see in the pictures. I was just offsetting each stick by a certain amount. Once i reached a certain width I cut the stick and did the same thing over.
however
if i would build a second table i would not glue the sticks to each other. It is messy slow and not very effective. i would glue them directly to the plywood and then glue this "sandwich" in one step to the table. I started with the Rocket Stick Panel before i was really sure how i wanted to approach the whole Build.
Step 2: Left and Right Legs in an Upside Down U Shape.
A word of caution in the beginning. Please check, double check and triple check if your wood is free from all kinds of metall. Some pallets had a really long live and the might be nails in places you would not expect them. Inspect every piece of wood you want to used very closely. If you miss a nail or a screw it could become nasty quickly. If a table saw Rips it out............. i think you know what i try to write here. Be cautious
When using pallet wood as the main structural element it is to be expected that the wood is warped, twisted, damaged or even all of the above.
I lay out all pieces that i want to use and try to match them to each other. The way i see it if i am using palett wood i do not expect anything to be perfect. Actually i try to embrace the imperfections and make them part of the piece.
When i was planning the table i wanted it to be a bit wider and higher. The wood made me change the dimensions slightly.
I cut all of the wood to the new found dimensions. usually i add one to two millimiters as a safty margrin.
When i glued the the two U shapes together i made shure that the widht of the connecting part was matched on the open side of hte U shape.
I used weights to hold all parts down flat and then clamped them.
After the glue provided enough stability i filed all faces wich would be used in the next steps (both top parts) Use the carpenters angle
Step 3: Joining the Side Parts
To join th eleft and the right part i use three boards on the top of the table. Make shure that the gap between each of them is not to wide. You want to glue the tabletop to these boards later on. My ply wood was of very poor quality wich made me build the gap quite narrow.
To put the boards in place i first use glue once every thing is angeled to my liking i screw the boards down. To prevent splintering of the wood i first drill a a hole and then countersink it. i helps to get the head of the screw a couple of mm into the wood. I had a whole lot of sanding to perform to get to an even top surface. if the srews would have just been flush it would have been mor difficult.
The last board i attached was the one between the left and right side in the front. I cut it to the measured distance. For some parts it is easier to just meassure the resulting distance. (warped wood)
Step 4: Clolsing the Gaps Between the Boards on the Topside
Next it is time to take care of the Gaps between the boards on the top. To help the stability of the table top (and the whole table there should be one continuous "rim" around the whole are that the top will be glued onto.
I cut the pieces to size and then glued and screwed them into place.
Give the glue some time to dry.
next up Sanding run one.
Step 5: Belt Sanding, Belt Sanding and More Belt Sanding
This part now is quite time consuming. But just take your time and dont rush it. The main objective is to get the top of the table as flat as possible and as pappallel to the ground as possible. This is where pallette wood can be kind of difficult. This is (at least for me a game of patience) Check progress early and often.
In this step i sanded not just the top but all legs too. I decided to just sand the outward facing surfaces of the legs. I like to have the contrast between the very smooth outward looking surfaces and the rough inner ones. I do not want to hide the fact that pallete wood is used. This is the same with my Cardboard sculptures. I like it when the inside reveals, the Process, how the whole was created
Do not get impatient. You will thank yourself
Step 6: Plywood to Top and Front
This should be very straight forward. Place your plywood tonto the table. weigh it down and trace the outline. I gave each side a couple of milimeters wiggle room
The quality of the wood i used was so poor that it took me ages to find some patches of wood that where not completly damaged. Looking back i should have switched the material but i was to stuborn.
it worked in the end but it was not pleasant.
I layed down thik layers of glue, wich i spread with a spatula and then clamped the pieces down with everything i had. In thi sstep i gave the glue more time to dry. There was no trust towards that plywood.
Step 7: Sanding and Filing Run No. Two
After the table was freed from the massive clamping operation i first corrected all overlaps and then went to smooth of all the adges of the table. I made shure that all edges where rounded of (something like a 1mm radius) and that anything that could be a splinter hazard was sanded down.
This step elevated the whole apperance of the table quite a bit.
One of the legs had some severe surface marks which i decided not to touch. I liked that it looked this rough. On another leg was some stenciled on name wich i made sure not to damage while sanding.
The table startred to come together.
Step 8: Glazing the Main Body
I wanted to have more contrast in the table and not just contrast but i wanted the table top top be shiny and the legs and the "Body" mate. It is important to spread the glaze equally for if it is thinker in on spot it will get darker. Remember to apply the glaze with the grain of the wood if you want to keep the texture.
Step 9: Applying the Rocket Stick Stripe Layer
The biggest step forward. Finally the Tabletop and the table are joined together. This is a big Milestone, but it is actually the same procedure as with the application of the plywood.
The only real difference is that this layer is a bit more on the stiff side. This means that it has to be clamped down with more care. I used some really straight pieces of wood and clamped the rocket sticks down using them. This way it was much easier to clamp everything equally. Top and Front are Basicly the same. (but the smaller front panel is easier to clamp.
I did not want to start sanding on filing on this to early. I let it dry overnight.
Step 10: Finishing the Table Top
Now this is the finishing stretch. But with the goal near comes a very time intense part. The rocket stick top has to be fitted to the under structure. I beveled the whole to with a ca. 4mm radius. i think this is really important, because most of the balance sticks are cut from pine tree. If you do not round of the edges even light bumps against the top will result in splintering. Take you time you are nearly done.
Now i started to fill in little gaps that i left open while glueing together the sticks. I think it is easier to fix this holes now for the glued down table top is much more forgiving now. When i assembled it it was kind of brittle. When i do a version two of this table i will glue the sticks directly to the Plywood.
As my last filing step i rounded of the corners on the front plate.
Ready for the gloss coat.
Step 11: Glossy Top Finish. Finaly
I had one last thing to do before i could apply the gloss coat. I masked of the the legs and the body of the table. I just wanted the top to receive the glossy finish. 5 min, done.
As the glossy clear coat i used a water based acrylic varnish. There are no fumes it is dust dry after 30 min and i can put on an additional layer of paint after 12 hours. Good Stuff.
Finished. Happy. 2020 will be good.
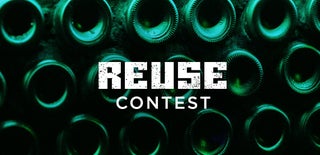
Participated in the
Reuse Contest